What Are The Most Important Parts Of The Control System
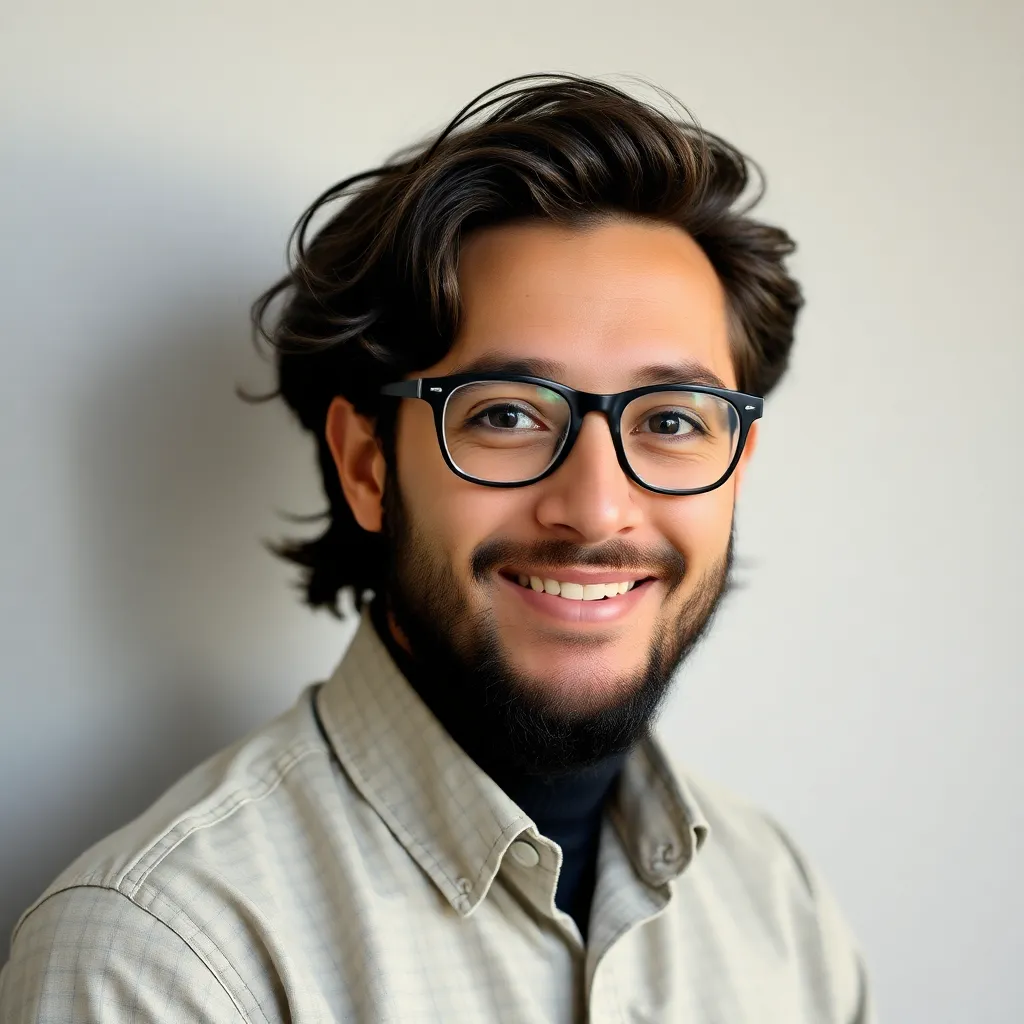
News Leon
Mar 31, 2025 · 7 min read
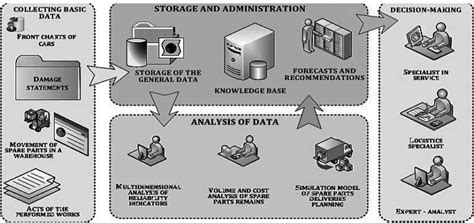
Table of Contents
What are the Most Important Parts of a Control System? A Deep Dive
Control systems are ubiquitous, silently orchestrating countless processes in our daily lives, from the thermostat regulating our home temperature to the complex algorithms guiding autonomous vehicles. Understanding the fundamental components of a control system is crucial for anyone working in engineering, robotics, automation, or even simply wanting to grasp the technological marvels surrounding us. This comprehensive guide will delve into the most important parts of a control system, exploring their roles, interactions, and the overall architecture that makes them function effectively.
The Core Components of a Control System
A typical control system comprises several essential components, each playing a vital role in maintaining desired performance. Let's break down these crucial parts:
1. The Process (or Plant): The Heart of the Operation
The process, often referred to as the plant, is the system being controlled. This is the entity whose behavior we aim to manipulate and regulate. Examples include:
- A robotic arm: Its position and movement are controlled to perform tasks.
- A chemical reactor: Temperature, pressure, and flow rates are regulated for optimal reaction.
- A heating system: Room temperature is maintained at a setpoint.
- An aircraft's flight control system: Altitude, speed, and direction are regulated.
The process possesses inherent dynamics and characteristics that influence the design and performance of the control system. Understanding the plant's behavior—its transfer function, time constants, and any nonlinearities—is fundamental to effective control.
2. The Sensors: Gathering Intelligence from the Process
Sensors are the eyes and ears of the control system, constantly monitoring the process variables. These variables are the specific aspects of the plant's behavior that need to be controlled. Examples include:
- Temperature sensors (thermocouples, RTDs): Measuring temperature in a reactor.
- Pressure sensors: Monitoring pressure in a pipeline.
- Position sensors (encoders, potentiometers): Determining the position of a robotic arm.
- Flow sensors: Measuring fluid flow rates.
- Level sensors: Monitoring liquid levels in a tank.
The accuracy, precision, and response time of sensors directly impact the control system's performance. Sensor noise and drift can significantly affect the system's ability to maintain accurate control.
3. The Controller: The Brain of the Operation
The controller is the decision-making unit of the control system. It receives feedback from the sensors regarding the process variables and compares this information to the desired setpoint (the target value). Based on this comparison (the error), the controller calculates the necessary adjustments to the actuator. Different types of controllers exist, each with its strengths and weaknesses:
- Proportional (P) controllers: The control action is proportional to the error. Simple to implement but may exhibit steady-state error.
- Integral (I) controllers: The control action is proportional to the integral of the error, eliminating steady-state error but potentially introducing overshoot and oscillations.
- Derivative (D) controllers: The control action is proportional to the rate of change of the error, improving stability and reducing overshoot.
- Proportional-Integral-Derivative (PID) controllers: A combination of P, I, and D actions, providing a robust and widely used control strategy. PID controllers are highly versatile and can be tuned to achieve optimal performance for a wide range of processes.
- Advanced controllers: These include model predictive control (MPC), fuzzy logic controllers, and neural network controllers. These advanced strategies offer more sophisticated control capabilities, especially for complex and nonlinear processes.
The choice of controller depends heavily on the specific process characteristics and desired performance objectives.
4. The Actuators: Taking Action to Control the Process
Actuators are the muscles of the control system, translating the controller's output into physical actions that manipulate the process. Examples include:
- Electric motors: Driving robotic arms, pumps, and valves.
- Hydraulic actuators: Providing powerful forces for heavy-duty applications.
- Pneumatic actuators: Utilizing compressed air for various control tasks.
- Heating elements: Adjusting temperature in a furnace.
- Valves: Regulating fluid flow rates.
The actuator's power, speed, and accuracy are crucial for effective control. Proper selection of actuators is vital to ensure that the controller's commands can be implemented effectively.
Feedback Loops: The Essence of Control
The interaction between the sensors, controller, and actuators forms a closed-loop system, also known as a feedback control loop. This loop is fundamental to achieving stable and accurate control. The feedback loop functions as follows:
- Sensors measure the process variable.
- The controller compares the measured value to the setpoint.
- The controller calculates the error (the difference between the setpoint and the measured value).
- The controller generates a control signal based on the error.
- The actuator implements the control signal, affecting the process variable.
- The process variable changes, and the cycle repeats.
This continuous feedback mechanism allows the control system to constantly adjust its actions to maintain the desired setpoint, even in the presence of disturbances.
Types of Control Systems
Control systems can be broadly classified into several types, each suited to different applications:
-
Open-loop control systems: These systems do not utilize feedback. The controller's output is not influenced by the process variable. Open-loop systems are simpler but less accurate and prone to disturbances. Think of a simple timer controlling the duration of a heating element.
-
Closed-loop control systems (feedback control systems): These systems utilize feedback to maintain accurate control. The controller's output is adjusted based on the measured process variable, making them more robust and accurate. The majority of sophisticated control systems fall into this category.
-
Linear control systems: These systems exhibit linear relationships between input and output. Analysis and design are simplified using linear mathematical tools.
-
Nonlinear control systems: These systems exhibit nonlinear relationships. Analysis and design are more complex, often requiring advanced techniques.
-
Single-input, single-output (SISO) systems: These systems have one input and one output.
-
Multiple-input, multiple-output (MIMO) systems: These systems have multiple inputs and multiple outputs, requiring more sophisticated control strategies.
Advanced Control Techniques
While PID controllers are widely used, advanced control techniques provide enhanced performance for complex systems:
-
Model Predictive Control (MPC): MPC uses a mathematical model of the process to predict future behavior and optimize control actions over a prediction horizon. This allows for proactive control, handling constraints and optimizing performance.
-
Fuzzy Logic Control: Fuzzy logic handles uncertainty and vagueness in system models and control rules. It's particularly useful when precise mathematical models are unavailable or difficult to obtain.
-
Neural Network Control: Neural networks learn from data to approximate complex relationships between inputs and outputs, adapting to changing system dynamics.
Importance of Proper Tuning and System Design
Regardless of the chosen control strategy, proper tuning and system design are essential for achieving optimal performance. Control system tuning involves adjusting the controller parameters (e.g., Kp, Ki, Kd in PID controllers) to achieve desired performance characteristics, such as minimizing overshoot, settling time, and steady-state error. This often involves trial and error, simulation, or utilizing advanced tuning methods. System design considerations include sensor selection, actuator choice, controller type, and overall system architecture.
Troubleshooting and Maintenance
Maintaining control system functionality is crucial. Troubleshooting involves identifying and resolving issues that affect the system's performance. Regular maintenance, including sensor calibration, actuator checks, and software updates, ensures continued reliable operation and prolongs the lifespan of the system.
Conclusion: A Symphony of Interconnected Components
Control systems, at their core, are a symphony of interconnected components working in harmony to achieve a desired outcome. Understanding the roles of the process, sensors, controller, and actuators, along with the importance of feedback loops and proper tuning, is vital for anyone involved in designing, implementing, or maintaining these crucial systems. From the mundane to the extraordinary, control systems quietly shape our world, empowering us to automate processes, optimize efficiency, and achieve feats beyond human capability alone. The intricacies of these systems continue to evolve, with advancements in computational power and control algorithms continuously pushing the boundaries of what's possible.
Latest Posts
Latest Posts
-
Which Is Greater 2 3 Or 3 5
Apr 02, 2025
-
Find The Area Of A Shaded Triangle
Apr 02, 2025
-
Which Of The Following Would Decrease Glomerular Filtration Rate
Apr 02, 2025
-
The Slope Of Speed Time Graph Indicates
Apr 02, 2025
-
What Is The Approximate Size Of A Nucleus
Apr 02, 2025
Related Post
Thank you for visiting our website which covers about What Are The Most Important Parts Of The Control System . We hope the information provided has been useful to you. Feel free to contact us if you have any questions or need further assistance. See you next time and don't miss to bookmark.