The Material Used For Fuse Has Low Melting Point
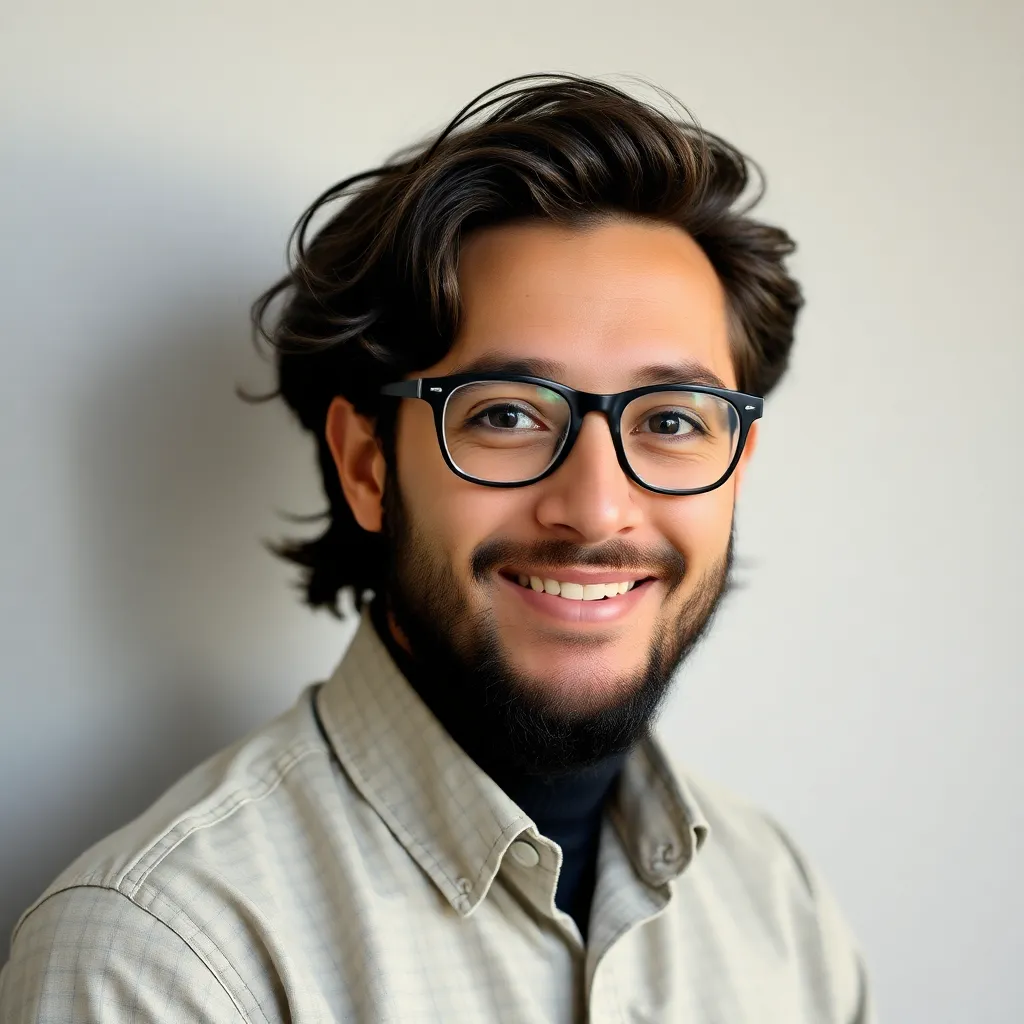
News Leon
Mar 19, 2025 · 6 min read
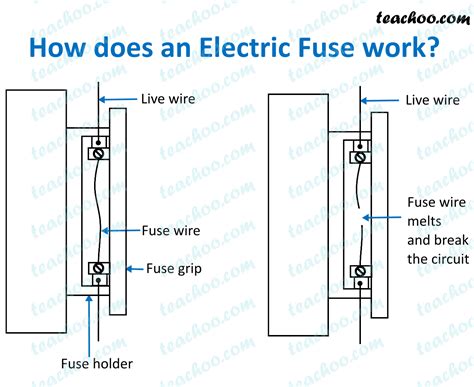
Table of Contents
The Material Used for Fuses Has a Low Melting Point: A Deep Dive into Fuse Technology
Fuses, those unsung heroes of electrical safety, are ubiquitous in our homes and industries. Their seemingly simple design belies a sophisticated interplay of materials science and electrical engineering, all centered around one crucial characteristic: a low melting point. This article delves deep into the reasons behind this critical design choice, exploring the materials science behind fuse construction, the various types of fuses available, and the importance of their low melting point in protecting electrical circuits and equipment.
Why a Low Melting Point is Crucial for Fuse Functionality
The primary function of a fuse is to protect an electrical circuit from overcurrent. Overcurrents can be caused by a variety of factors, including short circuits, overloaded circuits, and equipment malfunctions. If left unchecked, these overcurrents can lead to overheating, fires, and damage to expensive equipment. This is where the fuse's low melting point comes into play.
When an overcurrent occurs, the excessive current flowing through the fuse causes significant heat generation due to resistive heating (I²R losses). The material used in the fuse, specifically chosen for its low melting point, melts before the excessive current can damage other components in the circuit. This melting action breaks the circuit, effectively stopping the flow of current and preventing further damage. The low melting point ensures a rapid and reliable response to overcurrent situations, minimizing the risk of fire or equipment damage.
The speed at which the fuse melts is directly related to the amount of current flowing through it. Higher currents generate more heat, causing the fuse to melt faster. This fast response time is crucial in protecting sensitive electronics and preventing catastrophic failures.
The delicate balance: Melting point and current rating
The selection of a fuse with an appropriate melting point and current rating is critical. A fuse with a too high a melting point might not melt quickly enough, allowing excessive current to flow for an extended period and causing damage. Conversely, a fuse with a too low a melting point might blow even under normal operating conditions, causing unnecessary disruptions. Therefore, manufacturers carefully select materials and design fuses to match specific current requirements, ensuring optimal protection without unnecessary tripping.
Materials Commonly Used in Fuses and Their Melting Points
Several materials are commonly used in fuse construction, each chosen for its specific properties, including its low melting point, high conductivity, and predictable melting behavior.
1. Lead Alloys: A Historical Workhorse
Lead alloys, particularly those containing tin and antimony, were historically the most common material used in fuses. These alloys offered a good balance of low melting point, relatively high conductivity, and good mechanical properties. However, due to environmental concerns surrounding lead's toxicity, their use has significantly decreased in recent years. The melting point of lead-tin alloys typically ranges from around 180°C to 320°C depending on the exact composition.
2. Copper: High Conductivity, but Higher Melting Point
Copper is a highly conductive material, making it attractive for fuse applications. However, its relatively high melting point of 1085°C means it's not typically used as the sole melting element in low-voltage fuses. Instead, copper is often used for the fuse body or terminals, providing a robust and conductive structure. Its use is more common in high-voltage fuses where the higher melting point offers greater resilience.
3. Zinc: A Modern Alternative
Zinc offers a good compromise between melting point and conductivity, making it a popular choice for modern fuse elements. Its melting point is around 420°C, significantly lower than copper but higher than many lead-tin alloys. Zinc's relatively low cost and good mechanical properties also make it attractive for mass production.
4. Silver: High Cost, High Performance
Silver possesses exceptionally high conductivity and a melting point of 962°C. While its high melting point makes it unsuitable for standard low-voltage fuses, it finds applications in specialized high-current, fast-acting fuses where its superior conductivity is critical. The high cost of silver, however, restricts its widespread use.
5. Other Alloys: Tailored for Specific Applications
Various other alloys, often containing combinations of metals like aluminum, bismuth, and cadmium, are used in specialized fuse applications. The exact composition and consequently the melting point of these alloys are tailored to meet specific requirements for current rating, speed of response, and operating conditions.
Different Types of Fuses and Their Material Choices
Different types of fuses employ variations in design and material selection to achieve specific performance characteristics. The choice of material directly impacts the fuse's speed of response, current rating, and overall performance.
1. Cartridge Fuses
Cartridge fuses are a common type, with the fuse element enclosed within a cylindrical cartridge. These commonly utilize zinc or specialized low-melting-point alloys. The cartridge material provides mechanical protection and helps to contain the arc formed during melting.
2. Blade Fuses
Blade fuses are characterized by their flat, blade-like design. They often employ similar materials to cartridge fuses but with a different physical configuration to improve space efficiency and ease of connection.
3. Miniature Fuses
Miniature fuses are smaller versions designed for use in compact applications. Materials selection is crucial here, as space constraints might necessitate the use of specialized, high-density alloys with low melting points.
4. High-Voltage Fuses
High-voltage fuses often utilize materials with higher melting points, such as copper or specialized high-temperature alloys, to withstand the increased voltage stress and arc energy generated during operation.
The Importance of Consistent and Predictable Melting Behavior
Beyond the low melting point itself, the consistency and predictability of the melting behavior are equally crucial. The fuse must melt reliably at its rated current, avoiding premature failures or delayed responses. Factors such as material purity, manufacturing processes, and aging effects can all influence the melting behavior. Manufacturers invest significant effort in quality control to ensure the consistent performance of their fuses.
Conclusion: A Balancing Act for Electrical Safety
The low melting point of the material used in fuses is not merely a convenient design choice; it's the cornerstone of their effectiveness in protecting electrical circuits and equipment. The careful selection of materials, coupled with precise manufacturing techniques, ensures a rapid and reliable response to overcurrent situations, preventing damage and mitigating the risks of electrical fires. The ongoing development of new materials and fuse designs continues to improve safety and performance, underscoring the importance of this often-overlooked component in our electrically powered world. The future of fuse technology likely involves a continued focus on finding materials that offer a balance between low melting points, high conductivity, and environmentally friendly properties. The search for the ideal fuse material is an ongoing process driven by the ever-increasing demands of our increasingly complex electrical systems.
Latest Posts
Latest Posts
-
What Are The Raw Materials Required For Photosynthesis
Mar 19, 2025
-
Which Of The Following Is Not An Organic Substance
Mar 19, 2025
-
At A Price Below Equilibrium Price There Is
Mar 19, 2025
-
Which Of The Following Cannot Travel In A Vacuum
Mar 19, 2025
-
What Is The Molecular Mass Of Helium
Mar 19, 2025
Related Post
Thank you for visiting our website which covers about The Material Used For Fuse Has Low Melting Point . We hope the information provided has been useful to you. Feel free to contact us if you have any questions or need further assistance. See you next time and don't miss to bookmark.