Range Of Possible Sizes For Side X
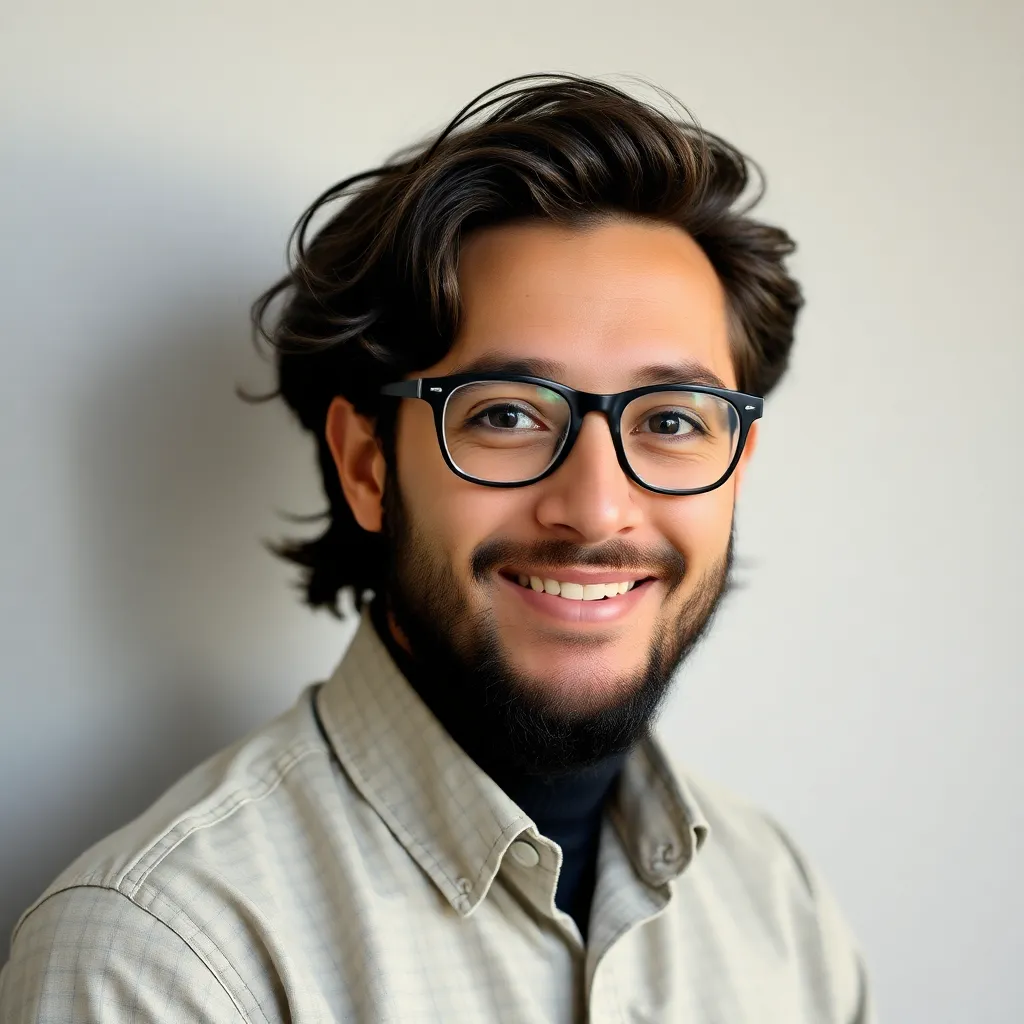
News Leon
Mar 22, 2025 · 6 min read
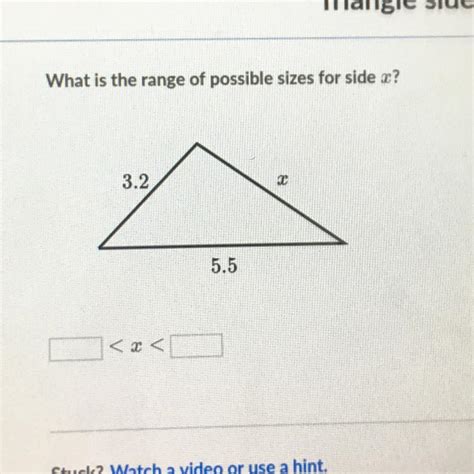
Table of Contents
Range of Possible Sizes for Side X: A Comprehensive Guide
Determining the appropriate size for "Side X" – a crucial component in various applications, from construction and engineering to design and manufacturing – requires a nuanced understanding of several factors. This comprehensive guide delves into the multifaceted aspects influencing the selection of Side X dimensions, offering a detailed exploration of the possible size ranges and the considerations that govern them. We’ll explore the impact of material properties, design constraints, functional requirements, and applicable standards to provide a robust framework for making informed decisions.
Understanding the Context of Side X
Before diving into specific size ranges, it's crucial to define what "Side X" represents within your particular application. This variable acts as a placeholder, symbolizing a crucial dimension in various contexts. To illustrate, consider these examples:
- Construction: Side X could be the length of a beam, the width of a foundation, or the height of a wall.
- Engineering: Side X might represent the diameter of a pipe, the length of a lever arm, or the thickness of a structural component.
- Design: In a design context, Side X might be the width of a furniture piece, the length of a graphic element, or the height of a container.
- Manufacturing: Side X can represent the diameter of a shaft, the dimension of a machined part, or the width of a printed circuit board.
The inherent variability in the meaning of "Side X" necessitates a flexible approach to determining its appropriate size. The guidelines and considerations outlined below will adapt to these various contexts.
Factors Influencing the Size of Side X
The optimal size range for Side X is not a universal constant. Numerous factors interdependently influence its selection. These can be broadly categorized as:
1. Functional Requirements:
This is arguably the most crucial factor. The intended function of the component directly dictates the required size range. For instance:
-
Strength and Load-Bearing Capacity: If Side X represents a structural member, its size must be sufficient to withstand anticipated loads without failure. This involves careful consideration of material properties, stress analysis, and safety factors. Insufficient size could lead to structural collapse, while excessive sizing can lead to unnecessary material costs and weight.
-
Clearance and Fit: In mechanical systems, Side X might define the clearance between moving parts. Too little clearance can cause binding and friction, while excessive clearance can compromise precision and stability. Precise tolerance specifications are essential in such cases.
-
Capacity and Volume: If Side X is related to storage or containment, its size must accommodate the intended volume of material or substance. Consideration must be given to potential expansion or contraction due to temperature changes or other factors.
-
Ergonomics and User Experience: In design contexts, Side X might influence the usability and comfort of a product. Ergonomic considerations are paramount, ensuring the dimensions are suitable for human interaction and prevent discomfort or strain.
2. Material Properties:
The physical properties of the material used to construct the component heavily influence the feasible size range. These properties include:
-
Strength and Stiffness: Strong and stiff materials allow for smaller cross-sections to achieve the required load-bearing capacity. Conversely, weaker materials necessitate larger dimensions to maintain structural integrity.
-
Durability and Resistance to Degradation: The material's resistance to corrosion, wear, and tear impacts its long-term performance and dictates the necessary size to ensure sufficient lifespan. Consider environmental factors and anticipated usage conditions.
-
Weight and Density: Lighter materials allow for larger dimensions without significant weight penalties. This is especially important in applications where weight is a critical constraint.
-
Workability and Manufacturing Considerations: Some materials are easier to shape and fabricate than others. This can influence the practical limits of achievable dimensions during manufacturing.
3. Design Constraints:
Various design constraints impose limitations on the size range of Side X:
-
Space Limitations: The available space within a system or structure often dictates the maximum feasible size. This is particularly relevant in compact or confined environments.
-
Weight Restrictions: In certain applications, weight is a critical factor. This might impose upper limits on the size of Side X, necessitating the use of lighter materials or optimized designs.
-
Aesthetic Considerations: In design contexts, the size of Side X might be influenced by aesthetic principles, aiming for a visually appealing and harmonious form.
-
Cost and Budget: Material costs and manufacturing processes contribute to the overall cost. Finding a balance between functional requirements and cost-effectiveness influences the final size selection.
4. Applicable Standards and Regulations:
Industry standards and building codes often prescribe minimum or maximum size ranges for specific components. Compliance with these standards is crucial to ensure safety and legal adherence. Examples include:
-
Building Codes: Stipulate minimum dimensions for structural members and other components based on load-bearing capacity and safety requirements.
-
Industry Standards: Provide guidelines and specifications for various components, ensuring interoperability and consistent quality.
-
Safety Regulations: Enforce minimum dimensions to ensure safe operation and prevent potential hazards.
Determining the Range of Possible Sizes for Side X: A Practical Approach
A systematic approach is necessary to determine the appropriate size range for Side X within a given context. This involves:
-
Clearly Defining the Requirements: Start by specifying the intended function of Side X, including load-bearing capacity, clearance requirements, volume needs, and other functional specifications.
-
Material Selection: Choose a material that meets the required strength, durability, weight, and cost requirements.
-
Stress Analysis and Calculations: Conduct appropriate engineering calculations, such as stress analysis and finite element analysis, to ensure the selected size can withstand anticipated loads.
-
Tolerance Specification: Determine acceptable tolerances for the dimensions of Side X, considering manufacturing capabilities and functional requirements. Tight tolerances may increase manufacturing costs.
-
Consideration of Manufacturing Processes: Assess the feasibility of manufacturing Side X to the desired dimensions using the chosen material and manufacturing process. Evaluate potential limitations and associated costs.
-
Compliance with Standards and Regulations: Ensure the chosen size adheres to all applicable industry standards, building codes, and safety regulations.
-
Prototyping and Testing: If feasible, construct prototypes to verify the functionality and performance of the chosen size. This allows for iterative refinements and adjustments before finalizing the design.
Examples of Size Ranges for Side X in Different Contexts
While specific numerical ranges are impossible without knowing the precise application, we can provide illustrative examples:
-
Wooden Beam (Construction): The size range for a wooden beam supporting a roof might span from 4 inches x 6 inches to 12 inches x 12 inches or even larger, depending on the span, load, and species of wood.
-
Steel Pipe (Engineering): The diameter of a steel pipe carrying high-pressure fluid could range from ½ inch to several feet, depending on the pressure, flow rate, and fluid characteristics.
-
Furniture Leg (Design): The diameter of a furniture leg might range from 1 inch to 4 inches, influenced by factors such as the overall size of the piece, the material used, and aesthetic considerations.
-
Machined Part (Manufacturing): The dimensions of a machined part can vary widely, from millimeters to meters, depending on the component's function and the machining tolerances.
Conclusion: The Importance of a Holistic Approach
Determining the appropriate size range for Side X demands a holistic and systematic approach. It is not a simple matter of selecting an arbitrary value. The optimal size range is a result of a careful balancing act between functional requirements, material properties, design constraints, and applicable standards. By considering these multifaceted aspects, designers and engineers can make informed decisions that result in reliable, safe, and cost-effective solutions. Remember that iterative design and testing are often necessary to fine-tune the dimensions and ensure optimal performance. This comprehensive approach minimizes risks and optimizes the overall design, ensuring that "Side X" contributes effectively to the success of the project.
Latest Posts
Latest Posts
-
Acceleration Is Always In The Direction
Mar 22, 2025
-
Which Of The Following Best Describes A Hormone
Mar 22, 2025
-
Is A Hydrogen Bond Stronger Than A Covalent Bond
Mar 22, 2025
-
Which Of The Following Is An Equation
Mar 22, 2025
-
A Toroid Having A Square Cross Section
Mar 22, 2025
Related Post
Thank you for visiting our website which covers about Range Of Possible Sizes For Side X . We hope the information provided has been useful to you. Feel free to contact us if you have any questions or need further assistance. See you next time and don't miss to bookmark.