Explain The Process Of Making Yarn From Fibre Answer
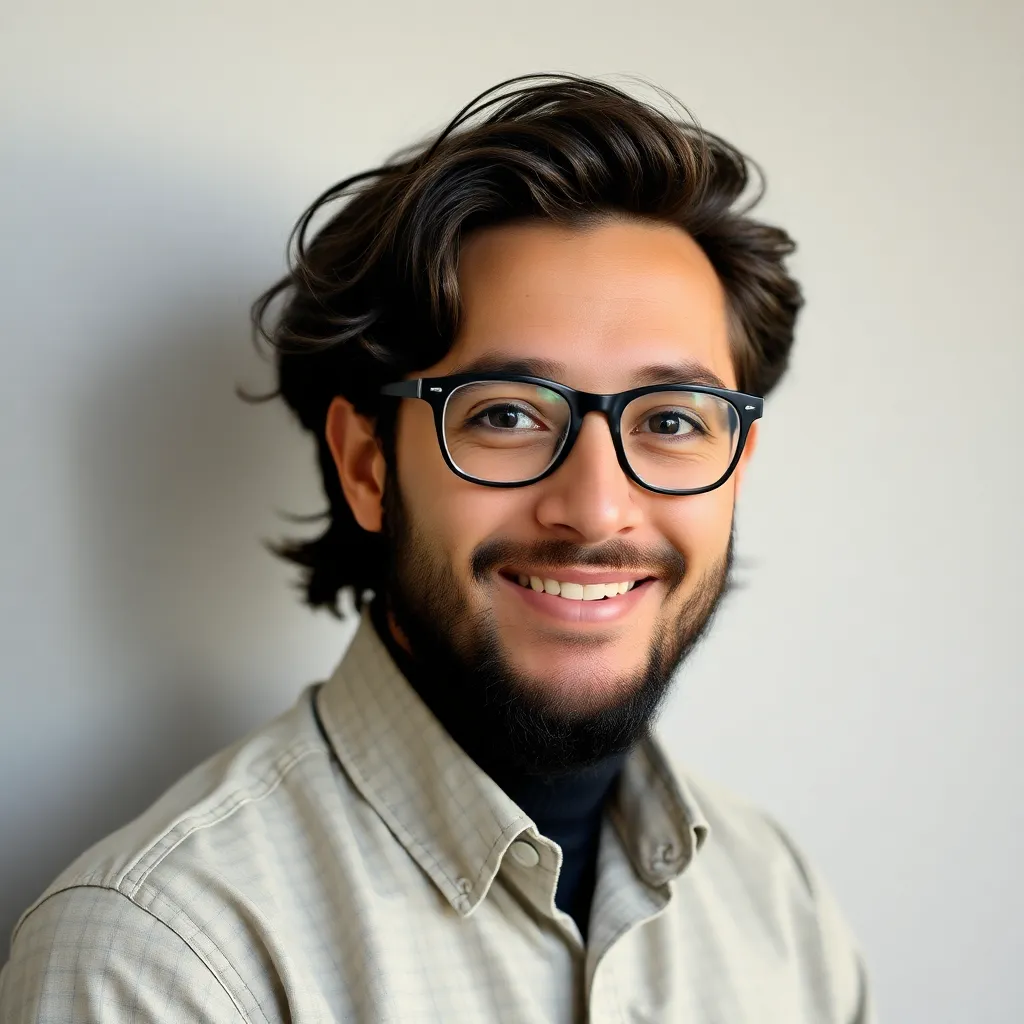
News Leon
Apr 02, 2025 · 7 min read
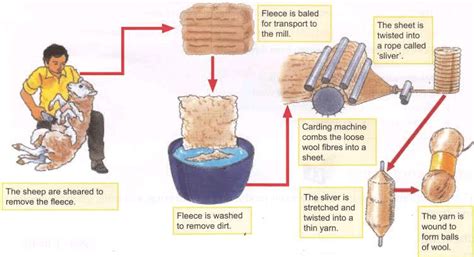
Table of Contents
From Fiber to Yarn: A Comprehensive Guide to Yarn Making
Yarn, the fundamental building block of countless textiles, is more than just thread; it's a testament to human ingenuity and a fascinating journey from raw fiber to finished product. Understanding the process of yarn making unveils a rich history and intricate techniques that have evolved over centuries. This comprehensive guide delves into the fascinating world of yarn production, exploring each step from the initial fiber source to the final spun yarn.
The Source: Exploring Different Fibers
The journey begins with the fiber itself – the raw material that forms the foundation of our yarn. Fibers can be broadly categorized into two types: natural and synthetic.
Natural Fibers: Nature's Gift
Natural fibers are derived from plants or animals and boast unique characteristics that influence the final yarn properties. Some prominent examples include:
-
Cotton: A staple fiber renowned for its softness, breathability, and absorbency. Cotton plants are harvested, and the fibers are separated from the seeds through a process called ginning. The length and quality of cotton fibers significantly impact the quality of the resulting yarn. Long-staple cotton yields stronger and smoother yarns compared to short-staple cotton.
-
Wool: Obtained from sheep, wool fibers are known for their warmth, elasticity, and moisture-wicking properties. The process of wool production involves shearing the sheep, cleaning the fleece (scouring), and sorting the fibers based on length and quality. Different sheep breeds yield wool with varying characteristics, affecting the final yarn's texture and performance. Merino wool, for instance, is prized for its softness and fine fiber diameter.
-
Silk: A luxurious fiber produced by silkworms, silk boasts an unparalleled sheen and smooth texture. The process involves harvesting cocoons, unwinding the silk filaments, and twisting them together to create silk yarn. The quality of silk yarn depends on factors like the silkworm breed and the careful handling during processing.
-
Linen: Derived from the flax plant, linen fibers are strong, durable, and possess excellent drape. The production process involves retting (softening the fibers), scutching (removing woody parts), and hackling (combing the fibers). Linen yarn is known for its crispness and coolness, making it suitable for summer clothing.
-
Hemp: A strong and durable fiber obtained from the hemp plant. Hemp is increasingly popular due to its sustainability and versatility. The processing involves harvesting, retching, and decorticating (separating the fiber from the core). Hemp yarn offers excellent strength and is used in various applications.
-
Jute: A coarse, strong fiber used primarily for burlap and other industrial textiles. Jute is harvested, retted, and then processed into yarn. Its strength and low cost make it a popular choice for certain applications.
Synthetic Fibers: Man-Made Marvels
Synthetic fibers are created artificially, offering a range of properties tailored to specific needs. These fibers are usually made from petroleum-based polymers and often offer advantages like durability, water resistance, and easy care. Examples include:
-
Polyester: A widely used synthetic fiber known for its strength, wrinkle resistance, and durability. Polyester yarn is versatile and used in a variety of textiles.
-
Nylon: Another popular synthetic fiber, nylon is renowned for its strength, elasticity, and abrasion resistance. It's frequently used in hosiery, sportswear, and carpets.
-
Acrylic: A versatile synthetic fiber that mimics the feel of wool but is more affordable and easier to care for. Acrylic yarn is often used in sweaters, blankets, and other knitted items.
-
Rayon: A semi-synthetic fiber made from cellulose. Rayon is often used to blend with other fibers, creating yarns with unique properties.
From Fiber to Yarn: The Spinning Process
Once the fibers are selected and prepared, the crucial process of spinning begins. This transforms individual fibers into continuous strands of yarn. Several methods exist, each with its own advantages and limitations.
1. Carding: Untangling and Aligning Fibers
Carding is a crucial preliminary step, particularly for short staple fibers like cotton. This process uses rotating cylinders covered with fine wire teeth to untangle and align the fibers, creating a continuous web. Carding eliminates snarls and prepares the fibers for the next stage.
2. Combing: Refining the Fiber Alignment
Combing is an optional step used for finer yarns, typically with longer staple fibers like wool or high-quality cotton. Combing removes shorter fibers and further aligns the longer ones, resulting in a more even and luxurious yarn.
3. Drawing: Attenuating and Parallelising
Drawing involves gently stretching and thinning the carded or combed web, further aligning the fibers and increasing the length of the fiber strand. This process repeats multiple times, improving fiber parallelism.
4. Spinning: Twisting into Yarn
Spinning is the heart of yarn production. It involves twisting the aligned fibers together to create a coherent and continuous strand. Different spinning techniques exist:
-
Ring Spinning: A traditional method employing a rotating spindle and traveler to twist the fibers. Ring spinning produces a strong and relatively smooth yarn.
-
Open-End (Rotor) Spinning: A faster and more cost-effective method, rotor spinning utilizes a rotating rotor to trap and twist the fibers. This method produces a slightly less smooth yarn compared to ring spinning.
-
Air-Jet Spinning: A high-speed method that uses jets of air to twist the fibers. Air-jet spinning produces a finer and more even yarn, particularly suitable for delicate fabrics.
-
Worsted Spinning: A method typically used for longer staple fibers like wool, worsted spinning involves combing the fibers to create a highly aligned and parallel strand, leading to a stronger, smoother, and more refined yarn.
5. Winding: Creating Yarn Packages
Once the yarn is spun, it needs to be wound onto bobbins, cones, or other packages for further processing or use. This ensures the yarn is neatly stored and ready for use in weaving, knitting, or other textile applications.
Yarn Properties: Understanding the Differences
The properties of the final yarn depend on several factors:
-
Fiber type: Different fibers possess unique characteristics, influencing the yarn's softness, strength, drape, and other qualities.
-
Fiber length: Longer staple fibers generally produce stronger and smoother yarns.
-
Spinning method: Different spinning techniques yield yarns with varying characteristics in terms of strength, evenness, and surface texture.
-
Twist: The amount of twist applied during spinning significantly impacts the yarn's strength and texture. Higher twist results in a stronger but potentially stiffer yarn.
-
Yarn count: This refers to the fineness of the yarn, expressed as the number of yards per unit weight (e.g., yards per pound). Higher yarn counts indicate finer yarns.
Beyond the Basics: Specialty Yarns and Techniques
The world of yarn extends beyond the standard spinning methods. Numerous specialty yarns cater to specific needs and aesthetic preferences:
-
Plied yarns: Created by twisting two or more single yarns together, plied yarns are stronger and more durable than single yarns.
-
Cabled yarns: Formed by twisting plied yarns together, cabled yarns offer increased strength and a unique texture.
-
Fancy yarns: These yarns incorporate unique effects like slubs, knots, or boucles, adding visual interest to the final fabric.
The Importance of Yarn Quality Control
Throughout the entire process, rigorous quality control is vital. This involves monitoring fiber quality, ensuring consistent spinning parameters, and inspecting the finished yarn for defects. Quality control ensures consistent yarn properties, resulting in high-quality textiles.
Yarn's Impact and Future Trends
The production of yarn is a testament to human ingenuity and its importance in our daily lives cannot be overstated. From the clothes we wear to the carpets under our feet, yarn is omnipresent. As the world becomes more conscious of sustainability, the future of yarn production looks towards eco-friendly practices and innovative materials. Exploring and harnessing new fibers, improving spinning techniques, and reducing waste are key challenges for the industry. The future of yarn is dynamic, promising new possibilities and creative innovations.
This detailed exploration of yarn production, from fiber selection to the final yarn product, highlights the intricate processes and craftsmanship involved. Understanding these nuances provides a deeper appreciation for the textiles we encounter daily and underscores the ongoing evolution of this crucial industry.
Latest Posts
Latest Posts
-
What Is The Overall Tone Of This Passage
Apr 03, 2025
-
The Mass Of A Mole Of Nacl Is The
Apr 03, 2025
-
Desktop Is A Computer Term Which Refers To
Apr 03, 2025
-
Which Of The Esters Cannot Undergo Claisen Self Condensation
Apr 03, 2025
-
1 A 2 X 2 Integral Formula
Apr 03, 2025
Related Post
Thank you for visiting our website which covers about Explain The Process Of Making Yarn From Fibre Answer . We hope the information provided has been useful to you. Feel free to contact us if you have any questions or need further assistance. See you next time and don't miss to bookmark.