A Sanding Disk With Rotational Inertia
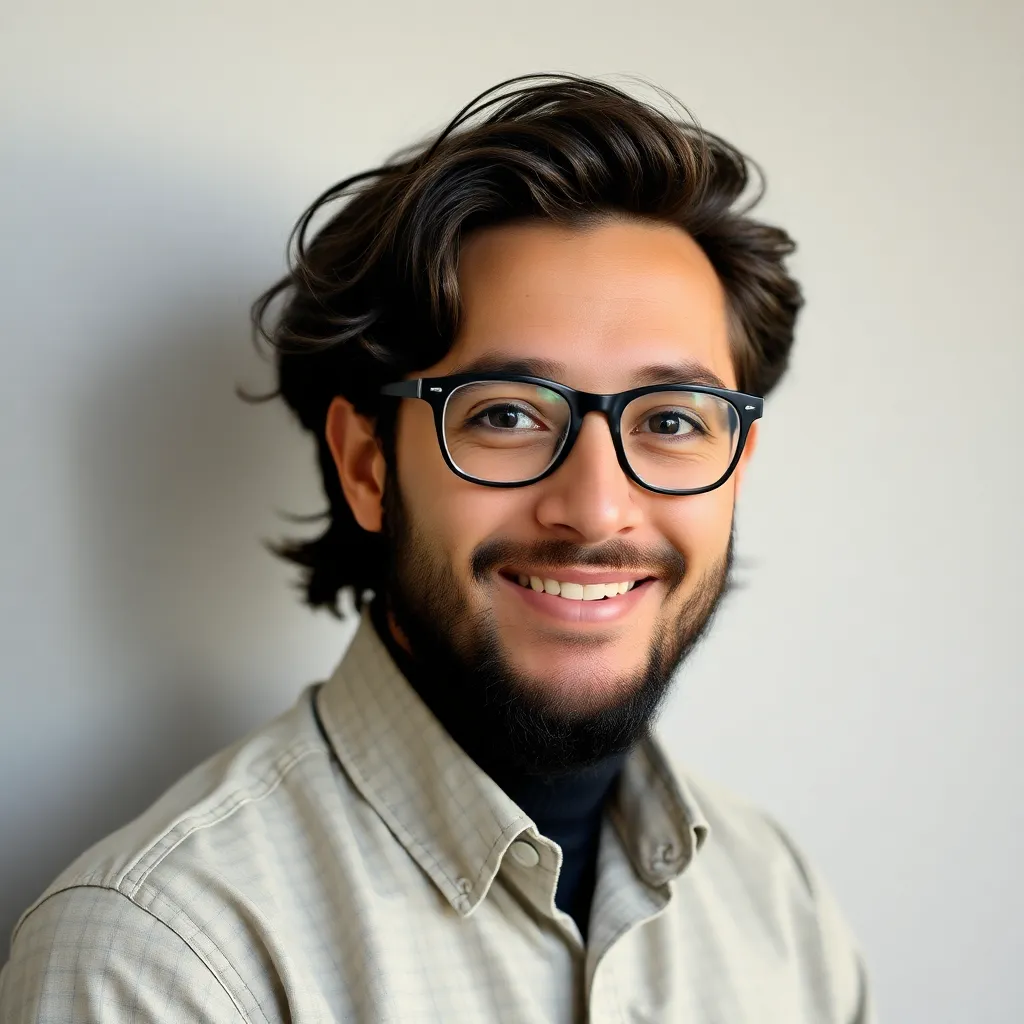
News Leon
Mar 18, 2025 · 6 min read
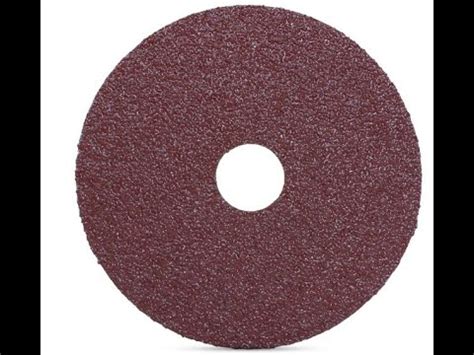
Table of Contents
A Sanding Disc with Rotational Inertia: Understanding the Physics Behind the Grind
Sanding discs are ubiquitous tools in various industries, from woodworking and metalworking to automotive repair and even dentistry. While their application might seem straightforward, a deeper understanding of their physics, particularly rotational inertia, reveals a fascinating interplay of forces and energy that significantly impacts performance and efficiency. This article delves into the mechanics of a sanding disc, exploring the concept of rotational inertia, its influence on sanding effectiveness, and the practical implications for users.
Understanding Rotational Inertia
Before diving into the specifics of sanding discs, let's establish a firm grasp on rotational inertia. In simple terms, rotational inertia (also known as moment of inertia) is a measure of an object's resistance to changes in its rotation. Unlike linear inertia, which resists changes in linear motion, rotational inertia resists changes in angular velocity. The greater the rotational inertia, the more difficult it is to start, stop, or change the rotational speed of an object.
Several factors determine the rotational inertia of an object:
-
Mass: The more massive an object, the greater its rotational inertia. This is intuitive – a heavier object is inherently harder to spin.
-
Mass Distribution: The distribution of mass relative to the axis of rotation is crucial. Mass concentrated farther from the axis of rotation contributes more significantly to rotational inertia than mass close to the axis. This is why a long, slender rod is harder to spin about its end than a short, thick disc of the same mass.
-
Shape: The shape of the object directly influences its mass distribution and hence its rotational inertia. Different shapes will have different rotational inertia even if they have the same mass.
Calculating Rotational Inertia
The precise calculation of rotational inertia depends on the object's shape and mass distribution. For simple shapes like solid cylinders or discs, readily available formulas exist. For more complex shapes, integration techniques are often necessary. The formula for the rotational inertia (I) of a solid disc about an axis perpendicular to the disc and passing through its center is:
I = (1/2)MR²
Where:
- M is the mass of the disc.
- R is the radius of the disc.
This equation highlights the influence of both mass and radius on rotational inertia. A larger radius significantly increases rotational inertia, even with the same mass.
The Sanding Disc: A Case Study in Rotational Inertia
Now, let's apply this understanding to the sanding disc. A sanding disc, essentially a thin disc of abrasive material, is designed to rotate at high speeds, effectively removing material from a workpiece. Its rotational inertia plays a crucial role in its performance and usability.
Impact of Rotational Inertia on Sanding Performance
High rotational inertia can be both advantageous and disadvantageous:
Advantages:
-
Consistent sanding: A higher rotational inertia provides more resistance to variations in the sanding pressure, leading to more consistent sanding action. This is beneficial for achieving uniform finishes.
-
Smoother operation: The greater inertia can dampen vibrations and fluctuations in the rotational speed, resulting in a smoother, more controlled sanding process. This is especially important for delicate work or when using high-speed sanders.
Disadvantages:
-
Slower acceleration/deceleration: Higher rotational inertia means the disc takes longer to reach its operational speed and longer to stop. This can be inefficient and inconvenient for frequent speed adjustments.
-
Increased energy consumption: Overcoming the rotational inertia requires more energy, leading to increased power consumption. This is a significant factor in portable sanders where battery life is crucial.
-
Potential for kickback: In certain scenarios, particularly with higher inertia discs, a sudden change in sanding pressure or a snag in the material can lead to a significant kickback, posing a safety hazard.
Optimizing Rotational Inertia for Different Applications
The optimal rotational inertia for a sanding disc depends heavily on its intended application:
-
Fine Detail Work: For intricate detail work, a lower rotational inertia is desirable. This allows for better control and quicker changes in speed, preventing accidental damage. Smaller, lighter discs are preferred.
-
Heavy Material Removal: For heavier material removal, such as sanding rough wood or metal, a higher rotational inertia can be beneficial. The consistent sanding action and resistance to fluctuations improve the efficiency of the process. Larger, heavier discs with a greater radius are often used.
-
High-Speed Sanding: High-speed applications benefit from discs with a carefully optimized rotational inertia. While higher inertia offers consistency, excessive inertia might lead to difficulties in controlling the tool at high speeds. Material selection and disc design play crucial roles in mitigating this.
Material Selection and Design Considerations
The material composition and design of the sanding disc itself contribute significantly to its rotational inertia. Factors to consider include:
-
Abrasive Material: The type of abrasive material (e.g., aluminum oxide, silicon carbide) impacts the overall mass and density of the disc. Denser materials will contribute to higher rotational inertia.
-
Backing Plate: The backing plate material and its thickness significantly affect the overall mass and hence the rotational inertia. Steel backing plates, for example, result in higher inertia compared to lighter materials.
-
Disc Diameter and Thickness: As previously discussed, the diameter plays a crucial role. A larger diameter, even with the same material, leads to considerably higher rotational inertia. Thickness also affects the mass and hence the inertia.
-
Disc Construction: Some sanding discs incorporate additional features like ventilation holes to reduce weight and improve heat dissipation. These design elements directly impact the mass distribution and rotational inertia.
Practical Implications and Safety Considerations
Understanding the role of rotational inertia in sanding discs has practical implications for users:
-
Tool Selection: Choose sanding discs with appropriate rotational inertia based on the intended application. Don't use a disc with excessively high inertia for delicate work, and vice-versa.
-
Safety Procedures: Always adhere to safety guidelines when using power tools. Be aware of the potential for kickback, especially with high-inertia discs. Maintain a firm grip and avoid sudden changes in sanding pressure.
-
Maintenance: Regularly inspect your sanding discs for wear and tear. Damaged discs can exhibit unpredictable behavior, increasing the risk of accidents.
-
Work Technique: Employ proper sanding techniques to maximize efficiency and minimize the risk of damage. Consistent, controlled pressure is crucial, regardless of the disc's rotational inertia.
Future Trends and Innovations
Ongoing research and development in sanding technology are constantly exploring ways to optimize the performance and safety of sanding discs. This includes advancements in:
-
Material Science: The development of new abrasive materials with improved properties, leading to potentially lighter yet more effective discs with optimized inertia.
-
Disc Design: Innovative designs aimed at optimizing mass distribution and reducing vibration while maintaining sufficient inertia for consistent sanding.
-
Smart Technology Integration: Integrating sensors and feedback mechanisms to monitor and control the sanding process, providing real-time information about rotational speed, pressure, and other critical parameters. This can help to prevent accidents and optimize performance.
Conclusion
The seemingly simple sanding disc is a testament to the intricate interplay of physics and engineering. Understanding rotational inertia and its impact on performance is vital for both manufacturers and users. By carefully considering the factors influencing rotational inertia, and selecting appropriate discs for specific applications, one can achieve superior sanding results while minimizing safety risks. Ongoing innovation in materials science and disc design promises further improvements in sanding technology, enhancing efficiency and making the process safer and more effective for various applications across diverse industries. The future of sanding is one of refined control, precise results, and enhanced safety, all built on a solid understanding of fundamental physics.
Latest Posts
Latest Posts
-
How Many Valence Electrons Does Mn Have
Mar 18, 2025
-
Lines Of Symmetry On A Trapezoid
Mar 18, 2025
-
Two Same Words With Different Meanings
Mar 18, 2025
-
Select The Correct Statement About Equilibrium
Mar 18, 2025
-
Draw The Major Product Of The Following Reaction
Mar 18, 2025
Related Post
Thank you for visiting our website which covers about A Sanding Disk With Rotational Inertia . We hope the information provided has been useful to you. Feel free to contact us if you have any questions or need further assistance. See you next time and don't miss to bookmark.