What Factors Determine Which Type Of Deformation Takes Place
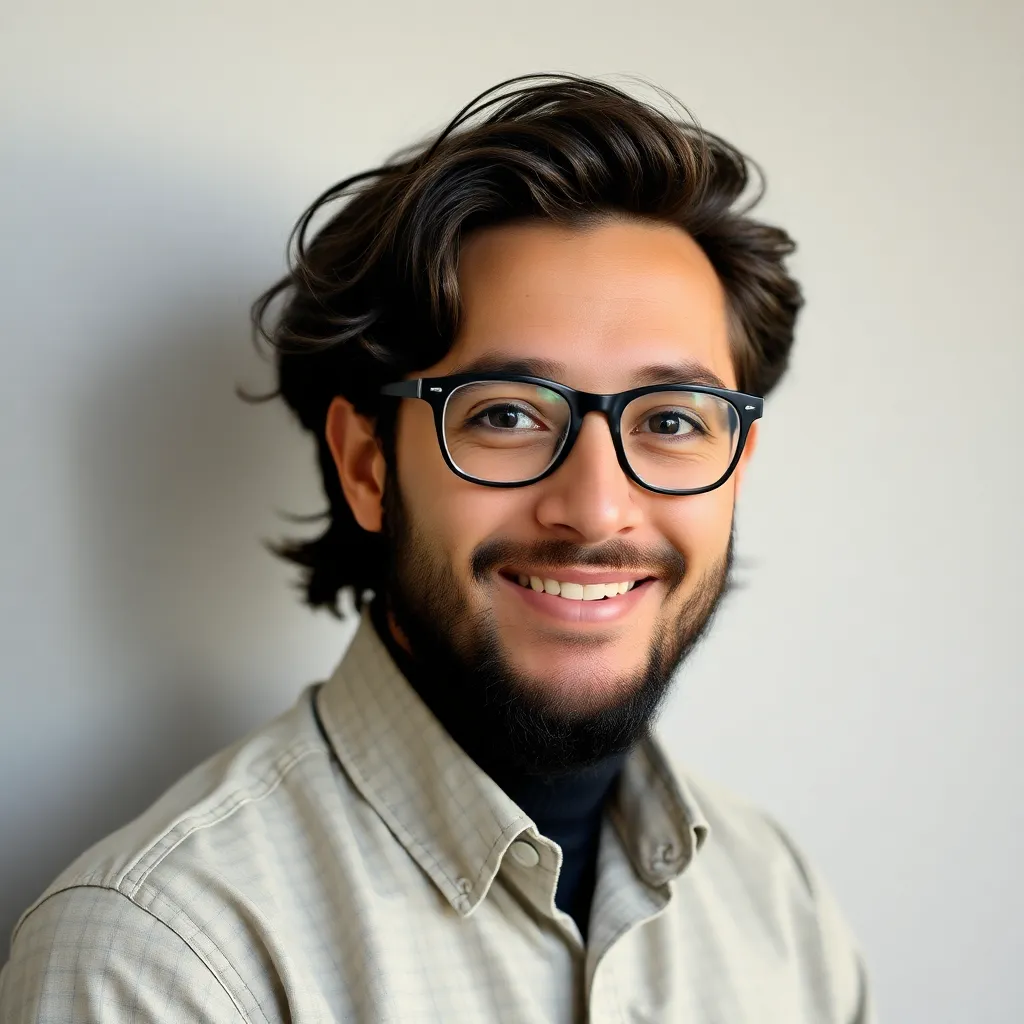
News Leon
Apr 09, 2025 · 7 min read

Table of Contents
What Factors Determine Which Type of Deformation Takes Place?
Understanding the factors that govern the type of deformation a material undergoes is crucial in numerous fields, from engineering design and geology to materials science and even medicine. Deformation, simply put, is any change in the shape or size of an object. This can range from the subtle stretching of a rubber band to the catastrophic fracturing of a rock under immense pressure. This article delves deep into the complexities of material deformation, exploring the key factors that dictate whether a material will deform elastically, plastically, or fracture.
The Three Fundamental Types of Deformation
Before we explore the controlling factors, let's establish a clear understanding of the three primary types of deformation:
-
Elastic Deformation: This is a reversible change in shape or size. When the stress is removed, the material returns to its original configuration. Think of stretching a rubber band – it returns to its original length once you let go. The deformation is proportional to the applied stress, following Hooke's Law within the elastic limit.
-
Plastic Deformation: This is an irreversible change in shape or size. Once the stress is removed, the material retains its deformed configuration. Think of bending a paperclip – it won't spring back to its original shape. Plastic deformation involves the permanent rearrangement of atoms within the material's crystal structure.
-
Fracture: This represents the complete failure of a material, resulting in its separation into two or more pieces. Fracture occurs when the stress exceeds the material's ultimate strength, leading to the propagation of cracks and ultimately, failure.
Key Factors Determining Deformation Type
Numerous factors interact to determine which type of deformation will occur. These can be broadly categorized as:
1. Material Properties: The Intrinsic Factors
The inherent characteristics of a material significantly influence its response to stress. These properties include:
-
Strength: This refers to a material's ability to resist deformation. High strength materials are more likely to deform elastically under lower stresses, while exhibiting plastic deformation or fracture only at higher stress levels. Low strength materials may undergo plastic deformation or fracture even under relatively low stresses. Different types of strength (e.g., tensile, compressive, shear) are relevant depending on the type of stress applied.
-
Ductility: This measures a material's ability to undergo significant plastic deformation before fracturing. Ductile materials can be significantly deformed before failure, exhibiting extensive plastic deformation. Brittle materials have little to no plastic deformation capacity and tend to fracture suddenly at their yield strength. Examples of ductile materials include copper and mild steel, while glass and cast iron are brittle examples.
-
Elastic Modulus (Young's Modulus): This quantifies the stiffness of a material – its resistance to elastic deformation. A high elastic modulus indicates a stiff material that requires a large stress to produce a small amount of elastic strain. A low elastic modulus represents a more flexible material. This is crucial in determining the extent of elastic deformation before yielding occurs.
-
Yield Strength: This is the stress at which a material begins to undergo plastic deformation. Once the yield strength is exceeded, the material will permanently deform. This is a critical parameter in engineering design, as exceeding the yield strength compromises the structural integrity of the component.
-
Ultimate Tensile Strength (UTS): This represents the maximum stress a material can withstand before fracturing under tensile loading. Reaching the UTS signifies impending failure.
-
Hardness: Hardness, while not directly defining deformation type, significantly influences the material's resistance to indentation and scratching. Hard materials tend to show less plastic deformation under compressive stresses.
-
Crystal Structure: The arrangement of atoms in a material's crystal lattice plays a critical role. Different crystal structures exhibit varying degrees of ductility and strength. For instance, face-centered cubic (FCC) metals generally exhibit higher ductility compared to body-centered cubic (BCC) metals. The presence of grain boundaries also affects the material's overall strength and ductility. Smaller grain sizes generally lead to higher strength and lower ductility.
2. Applied Stress: The Extrinsic Factors
The type and magnitude of stress applied to a material significantly influence its deformation behavior:
-
Magnitude of Stress: As discussed previously, a higher stress increases the likelihood of plastic deformation or fracture. Below the yield strength, only elastic deformation occurs. Between the yield strength and the ultimate tensile strength, plastic deformation dominates. Beyond the ultimate tensile strength, fracture occurs.
-
Type of Stress: Different types of stress (tensile, compressive, shear) can lead to different deformation responses. A material might be ductile in tension but brittle in compression. The orientation of stress relative to the material's microstructure also matters.
-
Rate of Loading: The speed at which the stress is applied affects the material's response. Higher loading rates often lead to less plastic deformation and a greater tendency towards brittle fracture, due to limited time for atomic rearrangements to occur. This is a critical consideration in impact situations.
-
Temperature: Temperature profoundly influences a material's behavior. Higher temperatures often promote plastic deformation, reducing the yield strength and increasing ductility. Conversely, lower temperatures can enhance brittleness and reduce ductility. This is why many materials are more susceptible to fracture at low temperatures.
3. Environmental Factors: The External Influences
While less prominent than material properties and applied stress, environmental factors can still play a role:
-
Corrosion: The presence of corrosive environments can weaken a material over time, reducing its strength and making it more prone to failure. Corrosion can also induce stress concentrations, accelerating fracture.
-
Radiation: Exposure to radiation can alter a material's microstructure, affecting its strength and ductility. Radiation damage can lead to embrittlement.
-
Presence of Cracks or Defects: Pre-existing flaws or defects in a material (e.g., voids, inclusions) can significantly reduce its strength and act as stress concentrators. These flaws can initiate crack propagation, leading to premature fracture, even under relatively low stresses. This is a major consideration in fracture mechanics.
Interplay of Factors: A Complex Relationship
It's crucial to remember that these factors don't act in isolation. They interact in a complex manner to determine the ultimate deformation behavior. For example, a highly ductile material subjected to a low stress at high temperature will exhibit significant plastic deformation. The same material under high stress at low temperature might fracture before exhibiting much plastic deformation. A seemingly strong material with a critical flaw might fail at much lower stress levels than expected.
Engineering Implications and Applications
Understanding these factors is essential for engineers in various disciplines. Choosing appropriate materials for specific applications requires careful consideration of the expected stresses, environmental conditions, and desired deformation behavior. For example:
-
Aerospace Engineering: Selecting materials for aircraft components requires materials with high strength, high fatigue resistance, and exceptional fracture toughness to withstand the extreme stresses and fluctuating temperatures encountered during flight.
-
Civil Engineering: Designing bridges and buildings necessitates materials with high compressive strength, durability, and resistance to environmental factors like corrosion and temperature fluctuations.
-
Mechanical Engineering: Designing machine components requires materials with appropriate yield strength, ductility, and wear resistance to function reliably under various load conditions.
-
Biomedical Engineering: Biomaterials for implants must be biocompatible, have appropriate mechanical properties to withstand physiological loads, and exhibit minimal wear and corrosion.
Conclusion: A Holistic Perspective on Deformation
Predicting the type of deformation a material will undergo is a multifaceted challenge. The interplay between material properties, applied stress, and environmental factors determines whether a material will deform elastically, plastically, or fracture. A thorough understanding of these factors is crucial for making informed decisions in materials selection, design, and safety assessment across a wide range of engineering and scientific applications. Further research and advancements in materials science are continuously refining our understanding of this complex phenomenon, leading to the development of stronger, more durable, and safer materials for various applications. By considering the holistic interplay of these factors, engineers and scientists can push the boundaries of material performance and create innovative solutions for the challenges of the modern world.
Latest Posts
Latest Posts
-
How To Convert Rev Sec To Rad Sec
Apr 18, 2025
-
Reaction Of Calcium Oxide With Water
Apr 18, 2025
-
What Is The Monomer Of A Polypeptide
Apr 18, 2025
-
How Many Centimeters Is 8 Mm
Apr 18, 2025
-
What C5h12 Isomer Will Give Only A Single Monochlorination Product
Apr 18, 2025
Related Post
Thank you for visiting our website which covers about What Factors Determine Which Type Of Deformation Takes Place . We hope the information provided has been useful to you. Feel free to contact us if you have any questions or need further assistance. See you next time and don't miss to bookmark.