The Image Shows A Piston System Where Gas Is Compressed
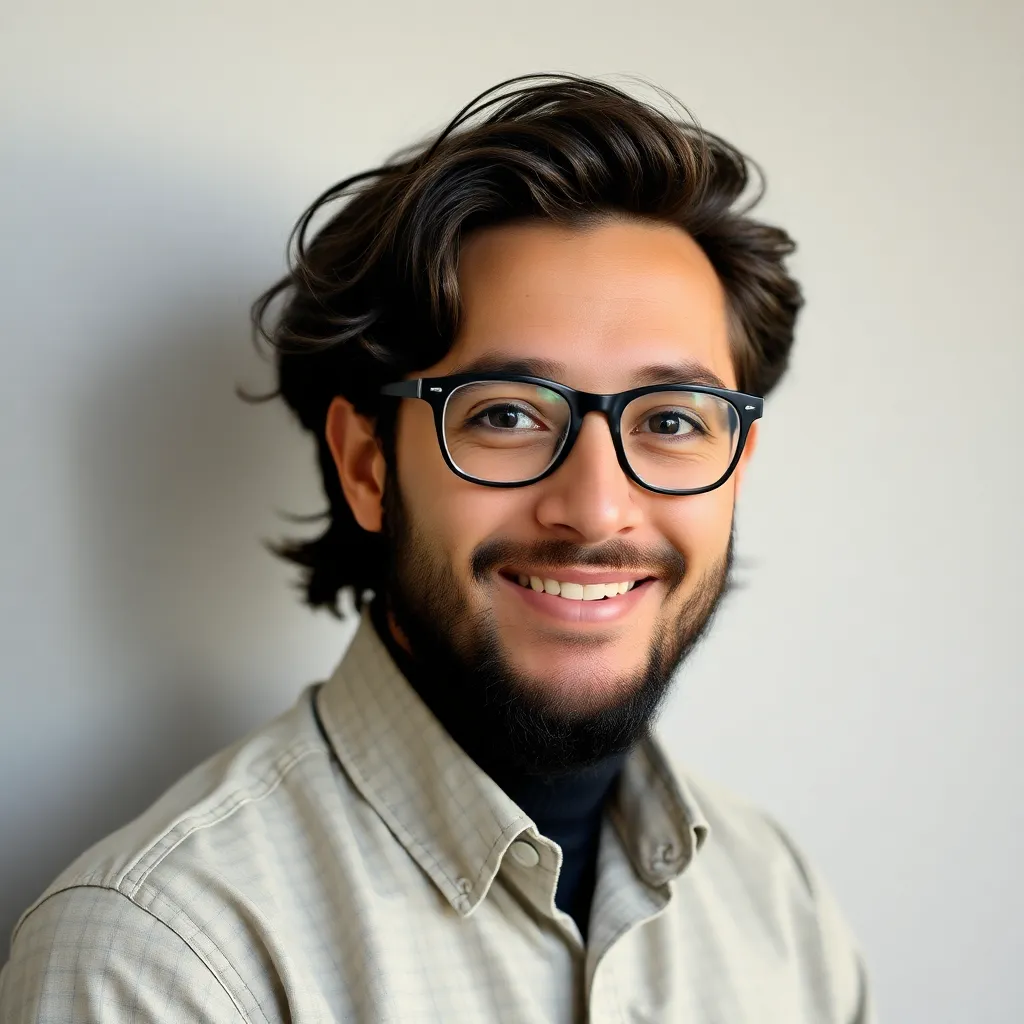
News Leon
Apr 21, 2025 · 5 min read

Table of Contents
The Piston System: A Deep Dive into Gas Compression
The image depicts a piston system undergoing gas compression, a fundamental process in numerous engineering applications. Understanding the mechanics, thermodynamics, and applications of this system is crucial for anyone involved in mechanical engineering, thermodynamics, or related fields. This article will explore the intricacies of piston-driven gas compression, covering its principles, variations, advantages, disadvantages, and real-world applications.
The Fundamentals of Piston-Driven Gas Compression
At its core, a piston system for gas compression involves a cylinder, a piston that moves reciprocatingly within the cylinder, and a mechanism (such as a crankshaft and connecting rod) to drive the piston's motion. As the piston moves from its maximum volume position to its minimum volume position (the compression stroke), the gas contained within the cylinder is compressed, resulting in an increase in both pressure and temperature.
The Ideal Gas Law and its Relevance
The behavior of the gas during compression is often modeled using the ideal gas law: PV = nRT, where:
- P represents pressure
- V represents volume
- n represents the number of moles of gas
- R represents the ideal gas constant
- T represents temperature
This equation highlights the interconnectedness of pressure, volume, and temperature. During compression, as the volume (V) decreases, the pressure (P) increases proportionally, assuming a constant temperature (isothermal process). However, in reality, compression processes are rarely isothermal. Heat transfer occurs, and the temperature (T) also changes, impacting the overall pressure increase.
Types of Compression Processes
Several thermodynamic processes describe how gas behaves during piston compression. The most common are:
-
Isothermal Compression: The temperature remains constant throughout the process. Heat is exchanged with the surroundings to maintain a constant temperature. This is an idealized scenario; practical systems often deviate.
-
Adiabatic Compression: No heat exchange occurs between the gas and its surroundings during the compression process. This leads to a significant temperature increase. Adiabatic compression is a more realistic model for many practical piston systems, particularly those with good insulation.
-
Isobaric Compression: The pressure remains constant during the compression process. This typically requires a controlled release of gas or a variable external pressure.
-
Polytropic Compression: This encompasses a wide range of compression processes that fall between isothermal and adiabatic. It is represented by the equation PV<sup>n</sup> = constant, where 'n' is the polytropic index, a value that depends on the specific conditions of the compression.
Components of a Piston Compression System
A typical piston compression system comprises several key components:
-
Cylinder: A strong, usually cylindrical, chamber that confines the gas during compression. The cylinder material must withstand high pressures and temperatures.
-
Piston: A cylindrical component that moves within the cylinder. It is usually fitted with piston rings to create a seal, preventing gas leakage. The piston's design influences the efficiency and effectiveness of the compression process.
-
Connecting Rod: This links the piston to the crankshaft, transmitting the piston's reciprocating motion to the rotational motion of the crankshaft.
-
Crankshaft: Converts the reciprocating motion of the piston into rotational motion, which can be used to power other machinery or drive the compression process.
-
Valves (In some systems): Intake and exhaust valves regulate the flow of gas into and out of the cylinder. These valves are crucial in systems where the compressed gas is further utilized, for instance, in internal combustion engines.
Advantages and Disadvantages of Piston-Driven Gas Compression
Advantages:
-
High Compression Ratios: Piston systems can achieve very high compression ratios, leading to significant pressure increases.
-
High Efficiency (Under Optimal Conditions): Well-designed piston systems can achieve high thermodynamic efficiency, particularly under adiabatic conditions.
-
Versatility: Piston systems can be adapted to handle various gases and compression ratios.
-
Established Technology: Piston technology is mature, reliable, and readily available.
Disadvantages:
-
Mechanical Complexity: Compared to other compression methods, piston systems can be mechanically complex, potentially leading to higher maintenance requirements.
-
Moving Parts Wear: The reciprocating motion of the piston and the rotational motion of the crankshaft result in wear and tear on the moving parts, requiring periodic maintenance and replacement.
-
Lubrication Requirements: Effective lubrication is crucial to minimize wear and friction in the piston system.
-
Noise and Vibration: Piston systems can generate significant noise and vibration, requiring sound dampening measures.
Applications of Piston-Driven Gas Compression
Piston-driven gas compression finds widespread applications across various industries:
-
Internal Combustion Engines: The most prominent application is in internal combustion engines (ICE), where the piston compresses the air-fuel mixture before ignition. This compression is crucial for efficient energy conversion.
-
Refrigeration and Air Conditioning Systems: Piston compressors are used in refrigeration and air conditioning systems to compress refrigerants, enabling heat transfer and cooling.
-
Pneumatic Systems: Compressed air generated by piston compressors powers pneumatic tools and systems in various industrial settings.
-
Industrial Processes: Piston compressors are used in various industrial processes requiring compressed gases, such as chemical processing, gas handling, and manufacturing.
-
Diving Equipment: High-pressure air tanks used in scuba diving are often filled using piston-driven compressors.
Advanced Considerations and Future Trends
The design and optimization of piston compression systems are ongoing areas of research and development. Several aspects are continuously being improved:
-
Material Science: The development of new materials capable of withstanding higher pressures and temperatures is essential for increasing efficiency and extending the lifespan of piston systems.
-
Computational Fluid Dynamics (CFD): CFD simulations are used to optimize the design of piston systems, minimizing energy losses and maximizing efficiency.
-
Control Systems: Advanced control systems enable precise control over the compression process, leading to better performance and reduced energy consumption.
-
Hybrid and Electric Systems: The integration of piston compressors with hybrid and electric powertrains is becoming increasingly important for achieving higher overall system efficiency in applications such as automotive systems.
Conclusion
Piston-driven gas compression remains a crucial technology in numerous engineering applications. Understanding the fundamental principles, types of compression processes, components, advantages, disadvantages, and real-world applications is vital for engineers, technicians, and anyone involved in related fields. Ongoing advancements in materials science, computational techniques, and control systems continue to improve the efficiency, reliability, and performance of piston compression systems, ensuring their continued importance in the future. The ongoing research and development in this area promises to further refine and enhance the performance of this fundamental engineering process. Further research into minimizing friction, optimizing sealing mechanisms, and developing more durable materials will continue to improve the efficiency and longevity of piston-based gas compression systems.
Latest Posts
Latest Posts
-
Which Of The Following Is An Incorrect Association
Apr 22, 2025
-
List The First 5 Multiples Of 6
Apr 22, 2025
-
Lcm Of 4 6 And 5
Apr 22, 2025
-
What Fraction Of An Hour Is 45 Minutes
Apr 22, 2025
-
Shayss Rebellion Was Significant Because It Demonstrated
Apr 22, 2025
Related Post
Thank you for visiting our website which covers about The Image Shows A Piston System Where Gas Is Compressed . We hope the information provided has been useful to you. Feel free to contact us if you have any questions or need further assistance. See you next time and don't miss to bookmark.