Suggest Two Methods To Prevent Rusting
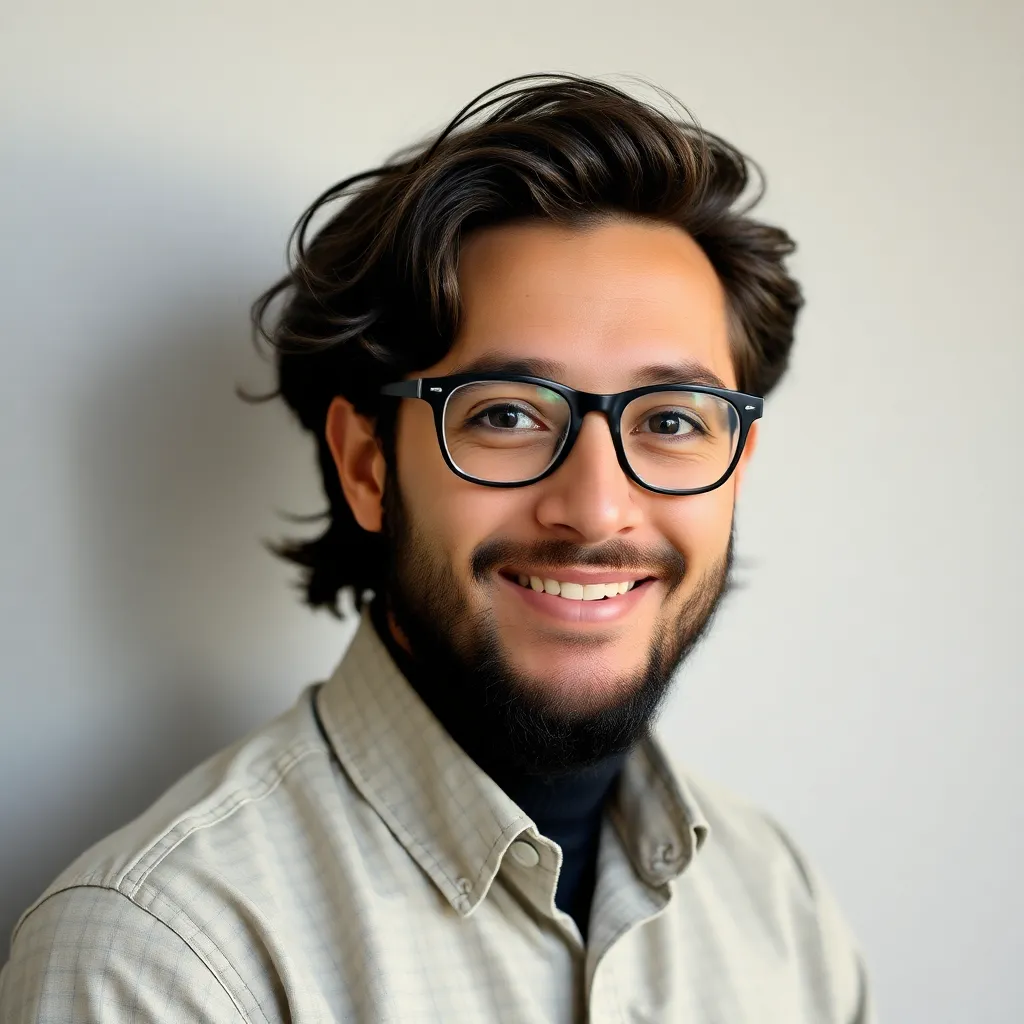
News Leon
Apr 24, 2025 · 7 min read

Table of Contents
Two Proven Methods to Prevent Rusting: A Comprehensive Guide
Rust, the bane of metalwork everywhere, is a common and costly problem. Understanding how to prevent it is crucial for preserving the integrity and lifespan of metallic structures, tools, and equipment. This comprehensive guide delves into two highly effective methods for rust prevention: protective coatings and cathodic protection. We'll explore the science behind these methods, their applications, advantages, and disadvantages, providing you with the knowledge to choose the best approach for your specific needs.
Understanding Rust: The Enemy of Metal
Before diving into prevention methods, it's important to understand the enemy. Rust, or iron oxide, is a form of corrosion that occurs when iron or its alloys (like steel) react with oxygen and water. This electrochemical reaction causes the iron to oxidize, resulting in the formation of a reddish-brown flaky layer that weakens the underlying metal. The process is accelerated by factors such as:
- Exposure to moisture: Water acts as an electrolyte, facilitating the electrochemical reaction.
- Presence of salt: Salt accelerates the corrosion process significantly. This is why coastal areas experience higher rates of rusting.
- Environmental pollutants: Acid rain and other pollutants can contribute to increased corrosion.
- Temperature fluctuations: Extreme temperature changes can stress the metal and make it more susceptible to rust.
Understanding these factors helps in selecting the most appropriate rust prevention method.
Method 1: Protective Coatings – A Barrier Against Corrosion
Protective coatings create a physical barrier between the metal and its environment, preventing oxygen and water from reaching the surface and initiating the rusting process. Various types of coatings are available, each with its strengths and weaknesses:
Types of Protective Coatings:
-
Paints: One of the most common and widely accessible methods, paint provides a relatively inexpensive and easy-to-apply barrier. Different types of paints offer varying levels of protection. Oil-based paints are durable and offer good resistance, but contain volatile organic compounds (VOCs) that are harmful to the environment. Water-based paints are more environmentally friendly and offer decent protection, although they might be less durable. Specialty paints, like those containing zinc or epoxy resins, provide superior protection against corrosion.
-
Polymer coatings: These coatings, such as polyurethane and epoxy, offer excellent adhesion, chemical resistance, and durability. They form a strong, impermeable layer that provides long-lasting protection. However, they often require professional application and can be more expensive than paint.
-
Powder coatings: Applied electrostatically and cured in an oven, powder coatings are extremely durable, resistant to abrasion and chemicals, and offer superior corrosion protection. They are commonly used for metal furniture, appliances, and automotive parts.
-
Metal coatings: These involve applying a layer of another metal to the base metal, often through processes like galvanization (zinc coating), electroplating (applying a thin layer of metal through electrolysis), or metal spraying. Galvanization is particularly effective and widely used for protecting steel structures and components. The zinc coating acts as a sacrificial anode, protecting the underlying steel even if the coating is scratched or damaged.
-
Ceramic coatings: These provide exceptional heat and chemical resistance, making them suitable for applications in high-temperature environments or exposure to harsh chemicals.
Advantages of Protective Coatings:
- Cost-effective (for some types): Paints, for example, are relatively inexpensive.
- Ease of application (for some types): Paints can be easily applied by individuals.
- Widely available: A vast range of coatings is readily available.
- Customization: Different coatings can be chosen to suit specific environmental conditions and requirements.
Disadvantages of Protective Coatings:
- Requires surface preparation: Proper surface cleaning and preparation are crucial for ensuring good adhesion and effectiveness.
- Susceptibility to damage: Coatings can be scratched, chipped, or worn away, exposing the underlying metal to rust.
- Limited lifespan: Coatings eventually degrade, requiring repainting or recoating.
- Environmental concerns: Some coatings contain VOCs, posing environmental and health risks.
Method 2: Cathodic Protection – Electrochemical Rust Prevention
Cathodic protection is an electrochemical method that prevents corrosion by making the metal surface the cathode in an electrochemical cell. This involves introducing a sacrificial anode that corrodes preferentially, protecting the metal structure.
How Cathodic Protection Works:
This method utilizes the principles of electrochemistry. A sacrificial anode (typically zinc, magnesium, or aluminum) is connected to the metal structure to be protected. The anode has a more negative electrochemical potential than the metal, meaning it's more prone to oxidation. When placed in an electrolyte (e.g., water or soil), the anode corrodes preferentially, providing electrons to the metal structure, preventing it from oxidizing and forming rust. This process is continuous, providing long-term protection as long as the anode remains intact.
Another method of cathodic protection involves the use of an impressed current. In this case, a direct current is applied to the metal structure, making it the cathode. The current flow prevents the oxidation of the metal, protecting it from corrosion. This method requires an external power source and is typically used for large structures, such as pipelines and tanks.
Types of Cathodic Protection:
-
Sacrificial anode protection: This method utilizes a sacrificial anode, as described above. It's relatively simple to install and maintain, and requires no external power source. It's commonly used for smaller structures and buried metallic components.
-
Impressed current cathodic protection (ICCP): This method employs an external power source to drive a current to the metal structure, making it the cathode. This is typically used for large structures in harsh environments, as it provides a higher level of protection than sacrificial anode protection.
Advantages of Cathodic Protection:
- Long-lasting protection: Can provide decades of protection with proper maintenance.
- Effective in harsh environments: Effective even in highly corrosive conditions.
- Minimal maintenance (for sacrificial anode): Sacrificial anode systems require only periodic anode replacement.
- Can protect entire structures: Effective for large, complex structures.
Disadvantages of Cathodic Protection:
- Higher initial cost: Can be more expensive than protective coatings, particularly for ICCP systems.
- Requires specialized expertise: Installation and maintenance often require specialized knowledge and equipment.
- Potential for hydrogen embrittlement: In some cases, cathodic protection can lead to hydrogen embrittlement, weakening the metal.
- Environmental considerations: The corroded anodes need proper disposal.
Choosing the Right Method: A Practical Guide
The optimal rust prevention method depends on several factors:
- Type of metal: The type of metal and its susceptibility to corrosion play a significant role.
- Environmental conditions: Exposure to moisture, salinity, and pollutants influences the choice of method.
- Size and complexity of the structure: Large structures might require cathodic protection, while smaller items might benefit from coatings.
- Budget: Protective coatings are generally more budget-friendly than cathodic protection.
- Lifespan requirements: Cathodic protection offers longer-lasting protection compared to coatings.
For smaller items, like tools or metal furniture, protective coatings like paint or specialized metal coatings (galvanization) often suffice. For larger structures such as pipelines, bridges, or ships, cathodic protection is usually the more effective and reliable solution.
Maintenance and Inspection: Key to Long-Term Success
Regardless of the chosen method, regular maintenance and inspection are crucial to ensure long-term protection. For protective coatings, this involves regular visual inspections to check for damage and promptly repairing any scratches, chips, or peeling. For cathodic protection systems, regular monitoring of anode potential and current flow is necessary to ensure effective protection. Timely anode replacement is crucial for sacrificial anode systems.
Regular maintenance and inspections help prevent small problems from escalating into major issues, thereby extending the lifespan of metallic structures and minimizing repair costs.
Conclusion: Proactive Rust Prevention is Cost-Effective
Rust prevention is a critical aspect of maintaining the integrity and longevity of metallic structures. Choosing the appropriate method—whether protective coatings or cathodic protection—depends heavily on factors like the environment, the size and type of metal, and budget constraints. Both methods, when properly implemented and maintained, can significantly extend the life of metal structures and save considerable costs associated with repairs and replacements in the long run. Prioritizing proactive rust prevention is always the most cost-effective and environmentally sound approach.
Latest Posts
Latest Posts
-
1 Minus The Product Of 4 And A Number
Apr 24, 2025
-
Formic Acid And Sodium Formate Buffer Equation
Apr 24, 2025
-
Does A Weak Acid Have A Strong Conjugate Base
Apr 24, 2025
-
Is Ink A Compound Or A Mixture
Apr 24, 2025
-
The Kneecap Or Patella Is An Example Of
Apr 24, 2025
Related Post
Thank you for visiting our website which covers about Suggest Two Methods To Prevent Rusting . We hope the information provided has been useful to you. Feel free to contact us if you have any questions or need further assistance. See you next time and don't miss to bookmark.