Pressure Drop In A Pipe Formula
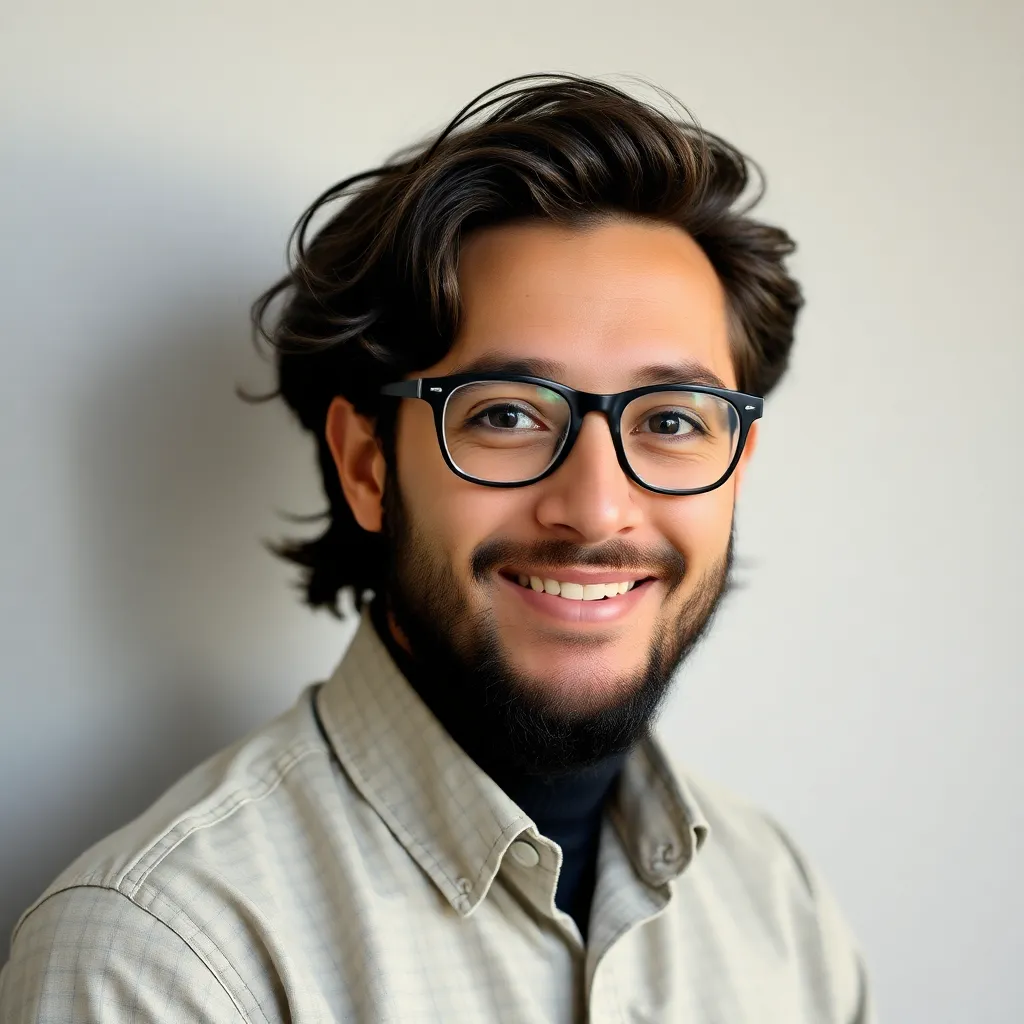
News Leon
Apr 24, 2025 · 7 min read

Table of Contents
Pressure Drop in a Pipe: Formulas, Factors, and Applications
Understanding pressure drop in pipes is crucial in various engineering disciplines, from designing efficient water supply systems to optimizing industrial fluid transport. Accurate calculation of pressure drop is essential for ensuring system performance, selecting appropriate pumps or compressors, and preventing equipment failures. This comprehensive guide delves into the formulas used to calculate pressure drop, the factors influencing it, and various applications in different fields.
Understanding Pressure Drop
Pressure drop, also known as head loss, refers to the decrease in fluid pressure as it flows through a pipe. This decrease is caused by frictional forces between the fluid and the pipe wall, as well as other factors such as changes in pipe diameter, fittings, and valves. The pressure drop directly impacts the system's efficiency and requires careful consideration during design and operation.
Key Factors Affecting Pressure Drop
Several factors contribute to pressure drop in a pipe. Understanding these factors is vital for accurate calculation and effective system design.
1. Pipe Length and Diameter
The longer the pipe, the greater the frictional resistance and consequently, the higher the pressure drop. Conversely, a larger pipe diameter reduces frictional resistance and results in a lower pressure drop. This relationship is inversely proportional – a doubling of diameter significantly reduces the pressure drop.
2. Fluid Properties
Fluid properties like viscosity and density significantly influence pressure drop. High-viscosity fluids experience greater frictional resistance, leading to higher pressure drop. Density also plays a role; denser fluids exert more force on the pipe walls, increasing pressure drop.
3. Flow Rate
The flow rate, or the volume of fluid passing through the pipe per unit time, is directly proportional to the pressure drop. Higher flow rates lead to increased frictional resistance and therefore a greater pressure drop.
4. Pipe Roughness
The roughness of the pipe's inner surface significantly impacts pressure drop. Rough pipes create more turbulence and friction, resulting in higher pressure drops compared to smooth pipes. Pipe roughness is often quantified using the Darcy-Weisbach friction factor.
5. Pipe Fittings and Valves
Elbows, bends, tees, and valves introduce additional resistance to fluid flow, causing significant pressure drops beyond those caused by friction alone. These fittings create localized turbulence and flow restrictions. The extent of pressure drop depends on the type and number of fittings.
6. Fluid Temperature
In some cases, fluid temperature can impact viscosity and thus pressure drop. For instance, the viscosity of many liquids decreases with increasing temperature, leading to a reduction in pressure drop. Conversely, the viscosity of some non-Newtonian fluids can increase with temperature, resulting in an increase in pressure drop.
Formulas for Calculating Pressure Drop
Several formulas are used to calculate pressure drop in a pipe, each applicable under specific conditions.
1. Darcy-Weisbach Equation
The Darcy-Weisbach equation is a widely used and versatile formula applicable to a broad range of flow regimes (laminar and turbulent). It is considered the most accurate method for calculating frictional pressure drop.
ΔP = f (L/D) (ρV²/2)
Where:
- ΔP is the pressure drop (Pa)
- f is the Darcy friction factor (dimensionless)
- L is the pipe length (m)
- D is the pipe inner diameter (m)
- ρ is the fluid density (kg/m³)
- V is the average fluid velocity (m/s)
The Darcy friction factor, f, is a dimensionless parameter that depends on the Reynolds number (Re) and the relative roughness (ε/D), where ε is the pipe roughness. For turbulent flow, the Colebrook-White equation or Moody chart are often used to determine f. For laminar flow (Re < 2000), f = 64/Re.
2. Hazen-Williams Equation
The Hazen-Williams equation is an empirical formula primarily used for water flow in pipes. It's simpler to use than the Darcy-Weisbach equation but less accurate, especially for non-water fluids or non-circular pipes.
ΔP = 4.52 * L * Q<sup>1.85</sup> / (C<sup>1.85</sup> * D<sup>4.87</sup>)
Where:
- ΔP is the pressure drop (psi)
- L is the pipe length (ft)
- Q is the flow rate (gal/min)
- C is the Hazen-Williams roughness coefficient (dimensionless)
- D is the pipe inner diameter (in)
The Hazen-Williams roughness coefficient, C, is an empirical value that depends on the pipe material and condition.
3. Manning Equation
The Manning equation is another empirical formula commonly used for open channel flow, but it can be adapted for pressure flow in partially full pipes. It's particularly useful for situations where the flow is relatively shallow.
V = (1/n) * R<sup>(2/3)</sup> * S<sup>(1/2)</sup>
Where:
- V is the flow velocity (m/s)
- n is the Manning roughness coefficient
- R is the hydraulic radius (m) – the cross-sectional area divided by the wetted perimeter
- S is the slope of the energy line (dimensionless)
The pressure drop can then be calculated using the energy equation, considering the change in elevation and velocity head.
Determining the Appropriate Formula
The choice of formula depends on several factors:
- Fluid type: The Darcy-Weisbach equation is the most general and applicable to various fluids, while the Hazen-Williams equation is primarily for water.
- Flow regime: For laminar flow, the simplified Darcy-Weisbach equation (with f = 64/Re) can be used; for turbulent flow, the full Darcy-Weisbach equation with a more complex determination of the friction factor is required.
- Pipe geometry: The Darcy-Weisbach equation can be adapted to non-circular pipes, while the Hazen-Williams equation is primarily for circular pipes.
- Accuracy requirements: The Darcy-Weisbach equation offers higher accuracy but requires more complex calculations, while the Hazen-Williams equation is simpler but less accurate.
Applications of Pressure Drop Calculations
Accurate pressure drop calculations are crucial in numerous applications across various engineering fields:
1. Pipeline Design
In designing pipelines for transporting oil, gas, or water, pressure drop calculations are essential to determine the required pump power, pipe diameter, and material to ensure efficient and reliable transportation. Inadequate pressure drop calculations can lead to insufficient flow or excessive energy consumption.
2. HVAC Systems
In heating, ventilation, and air conditioning (HVAC) systems, pressure drop calculations are crucial for designing ductwork and selecting appropriate fans to ensure proper airflow and temperature control. Incorrect calculations can lead to inadequate ventilation or inefficient energy usage.
3. Process Industry
In chemical, pharmaceutical, and food processing industries, precise pressure drop calculations are vital for designing and optimizing process equipment, ensuring the desired flow rates and preventing equipment damage due to excessive pressure.
4. Biomedical Engineering
In biomedical engineering, accurate pressure drop calculations are crucial for designing and simulating blood flow in artificial organs and vascular systems. Understanding pressure drop is vital for designing efficient and biocompatible medical devices.
5. Irrigation Systems
In agricultural irrigation systems, pressure drop calculations are important for designing efficient water distribution networks and selecting appropriate pumps to ensure sufficient water delivery to crops.
Advanced Considerations
While the formulas discussed provide a good starting point, several advanced considerations can improve the accuracy of pressure drop calculations:
- Minor losses: These losses occur due to pipe fittings, valves, and other components. They can be significant and often require adding correction factors to the basic pressure drop formulas.
- Non-Newtonian fluids: For fluids whose viscosity changes with shear rate (non-Newtonian fluids), more complex models are required to accurately predict pressure drop.
- Temperature variations: If fluid temperature varies significantly along the pipe, the pressure drop calculation should account for changes in fluid properties.
- Compressible fluids: For gases at high pressures, the compressibility of the fluid must be considered.
Conclusion
Accurately calculating pressure drop in pipes is a critical aspect of many engineering disciplines. Selecting the appropriate formula and considering all relevant factors—pipe length and diameter, fluid properties, flow rate, pipe roughness, and fittings—is essential for efficient system design and operation. While simplified equations like the Hazen-Williams equation offer ease of calculation, the Darcy-Weisbach equation provides superior accuracy across a broader range of conditions. By mastering pressure drop calculations, engineers can optimize system performance, minimize energy consumption, and ensure the safe and reliable operation of fluid transport systems.
Latest Posts
Latest Posts
-
How Many Lines Of Symmetry Are In A Circle
Apr 24, 2025
-
What Is The Derived Unit For Density
Apr 24, 2025
-
Does Dimethyl Ether Have Hydrogen Bonding
Apr 24, 2025
-
Which Of The Following Represents A Physical Change
Apr 24, 2025
-
The Boot Process Consists Of How Many Steps
Apr 24, 2025
Related Post
Thank you for visiting our website which covers about Pressure Drop In A Pipe Formula . We hope the information provided has been useful to you. Feel free to contact us if you have any questions or need further assistance. See you next time and don't miss to bookmark.