Formula For Maximum Compression Of A Spring
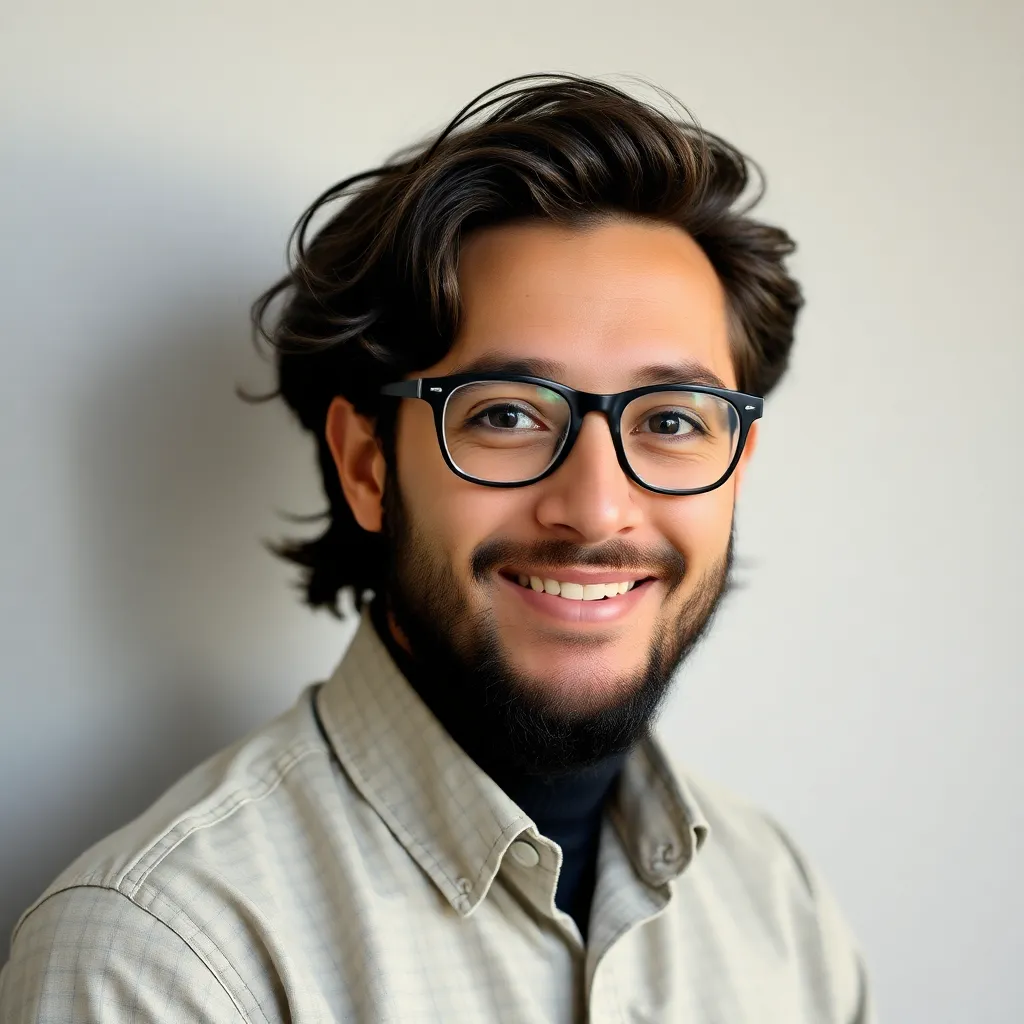
News Leon
Apr 08, 2025 · 6 min read
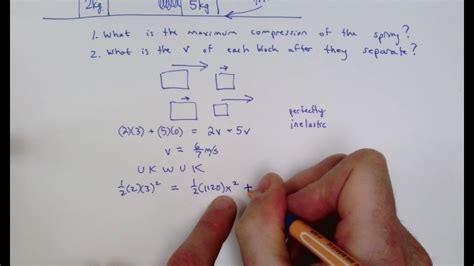
Table of Contents
The Formula for Maximum Spring Compression: A Deep Dive into Spring Mechanics
Understanding the maximum compression a spring can withstand is crucial in various engineering applications, from designing shock absorbers to crafting intricate mechanical devices. This article delves deep into the physics governing spring compression, exploring the formula, its limitations, and the factors influencing a spring's maximum safe compression. We'll explore different spring types and consider real-world scenarios where this understanding is paramount.
Understanding Spring Compression: Hooke's Law and Beyond
The fundamental principle governing spring behavior is Hooke's Law. This law states that the force required to compress or extend a spring is directly proportional to the displacement from its equilibrium position. Mathematically, this is expressed as:
F = kx
where:
- F represents the force applied (in Newtons)
- k represents the spring constant (in Newtons per meter, N/m) – a measure of the spring's stiffness. A higher k value indicates a stiffer spring.
- x represents the displacement or compression of the spring from its equilibrium position (in meters)
This simple equation holds true only within the elastic limit of the spring. Beyond this limit, the spring's material undergoes permanent deformation, and Hooke's Law no longer accurately predicts its behavior. This is a critical point to remember when considering maximum compression.
The Spring Constant (k): A Deeper Look
The spring constant, k, is a vital parameter. It's determined by the spring's material properties (Young's modulus, E), its geometry (wire diameter, d, number of coils, N, and coil diameter, D), and is calculated using different formulas depending on the spring type:
For Helical Compression Springs:
Several approximations exist, but a common and relatively accurate formula is:
k ≈ (Gd⁴)/(8D³N)
Where:
- G is the shear modulus of the spring material (a measure of its resistance to shearing forces).
- d is the wire diameter.
- D is the mean coil diameter.
- N is the number of active coils.
Note: This is a simplified formula. More precise calculations might require considering end conditions (e.g., plain ends, squared and ground ends) and other factors.
Determining Maximum Compression: Factors to Consider
Calculating the maximum compression a spring can safely handle involves going beyond Hooke's Law and considering several crucial factors:
1. The Elastic Limit: Beyond Hooke's Law
The elastic limit is the point beyond which the spring will not return to its original shape after the force is removed. This is a crucial limit. Exceeding it leads to permanent deformation and compromises the spring's functionality. The elastic limit is a material property and is typically determined through tensile testing.
2. Material Properties: Strength and Fatigue
The choice of spring material significantly impacts its maximum compression capabilities. High-tensile strength materials, such as spring steel, can withstand greater stress before yielding. However, even within the elastic limit, repeated compression and relaxation can lead to material fatigue, eventually causing failure. The number of cycles a spring can endure before failure is a vital consideration in applications involving repeated compression.
3. Buckling: A Critical Consideration for Long Springs
Long, slender springs are susceptible to buckling under compression. Buckling occurs when the compressive force exceeds the spring's ability to resist lateral bending. The critical buckling load depends on the spring's geometry and material properties and is often calculated using Euler's buckling formula or more sophisticated approaches for non-ideal conditions.
4. Solid Height: The Ultimate Limit
Every spring has a solid height, the minimum height it can achieve when fully compressed. Attempting to compress it beyond this point will lead to extremely high stresses and almost certain failure. The solid height is easily determined by calculating the total wire length and considering the end conditions.
5. Spring Set: Permanent Deformation
Even if the elastic limit isn't reached, repeated compression may lead to spring set, a gradual permanent deformation over time. This phenomenon is associated with microscopic changes within the material structure and affects the spring's functionality.
6. Safety Factor: A Critical Margin
Engineers always incorporate a safety factor when designing with springs. This factor accounts for uncertainties in material properties, manufacturing tolerances, and potential overloading. Typical safety factors range from 1.5 to 3, depending on the application's criticality. This means that the maximum design stress is significantly lower than the material's yield strength.
Calculating Maximum Safe Compression: A Practical Approach
Determining the maximum safe compression involves a multi-step process:
-
Determine the spring constant (k): Using the appropriate formula for your spring type and geometry.
-
Identify the material's properties: Obtain the yield strength (σy) and shear modulus (G) from the material datasheet.
-
Calculate the maximum allowable stress: Divide the yield strength (σy) by the safety factor (SF). For example, with a safety factor of 2, the maximum allowable stress would be σy/2.
-
Estimate the maximum allowable force: This depends on the spring's design. For helical compression springs, the maximum shear stress is often used. An approximation of this stress is:
τ = (8FD)/(πd³)
Where: τ is the shear stress, F is the force, D is the mean coil diameter, and d is the wire diameter. Solving this equation for F, while substituting the maximum allowable stress, gives the maximum force.
-
Calculate the maximum compression (x): Using Hooke's law, solve for x: x = F/k. This gives the maximum safe compression distance, given the maximum allowable force.
-
Verify against solid height: Ensure the calculated maximum compression (x) is significantly less than the spring's solid height.
-
Consider buckling: For long springs, calculate the critical buckling load and ensure the maximum allowable force remains significantly lower.
Different Spring Types and their Compression Limits
While the principles discussed above apply broadly, specific considerations arise for various spring types:
-
Helical Compression Springs: The most common type, the formulas and considerations above directly apply. The length and diameter significantly affect buckling tendencies.
-
Conical Springs: These springs have a variable coil diameter, resulting in non-linear force-displacement characteristics. Specialized calculations are necessary to accurately determine their maximum compression.
-
Belleville Springs (Disc Springs): These springs offer high force capacity in a compact design but exhibit highly non-linear behavior. Precise analysis often requires finite element analysis (FEA).
-
Leaf Springs: Used in vehicles and other applications, these require intricate analysis considering bending and shear stresses.
Conclusion: Safe Spring Design is Paramount
Understanding the formula for maximum spring compression is crucial for safe and reliable design. Remember that this isn't a single equation but rather a process that involves carefully considering material properties, spring geometry, potential failure modes (yielding, fatigue, buckling), and incorporating a suitable safety factor. Overlooking any of these factors can lead to spring failure, potentially causing damage or injury. Always consult engineering handbooks and standards for detailed guidelines specific to your application. Precise calculations, particularly for complex spring designs or high-stress applications, might require employing advanced analytical techniques, including FEA. By applying these principles diligently, engineers can ensure the safe and efficient use of springs in countless engineering marvels.
Latest Posts
Latest Posts
-
What Happens When A Star Exhausts Its Core Hydrogen Supply
Apr 08, 2025
-
Find The Value Of X In A Kite
Apr 08, 2025
-
Which Of The Following Is True Regarding The Sarcoplasmic Reticulum
Apr 08, 2025
-
Draw Significant Resonance Structures For The Following Compound
Apr 08, 2025
-
Difference Between A Mirror And A Lens
Apr 08, 2025
Related Post
Thank you for visiting our website which covers about Formula For Maximum Compression Of A Spring . We hope the information provided has been useful to you. Feel free to contact us if you have any questions or need further assistance. See you next time and don't miss to bookmark.