For Every Part Produced By A Factory
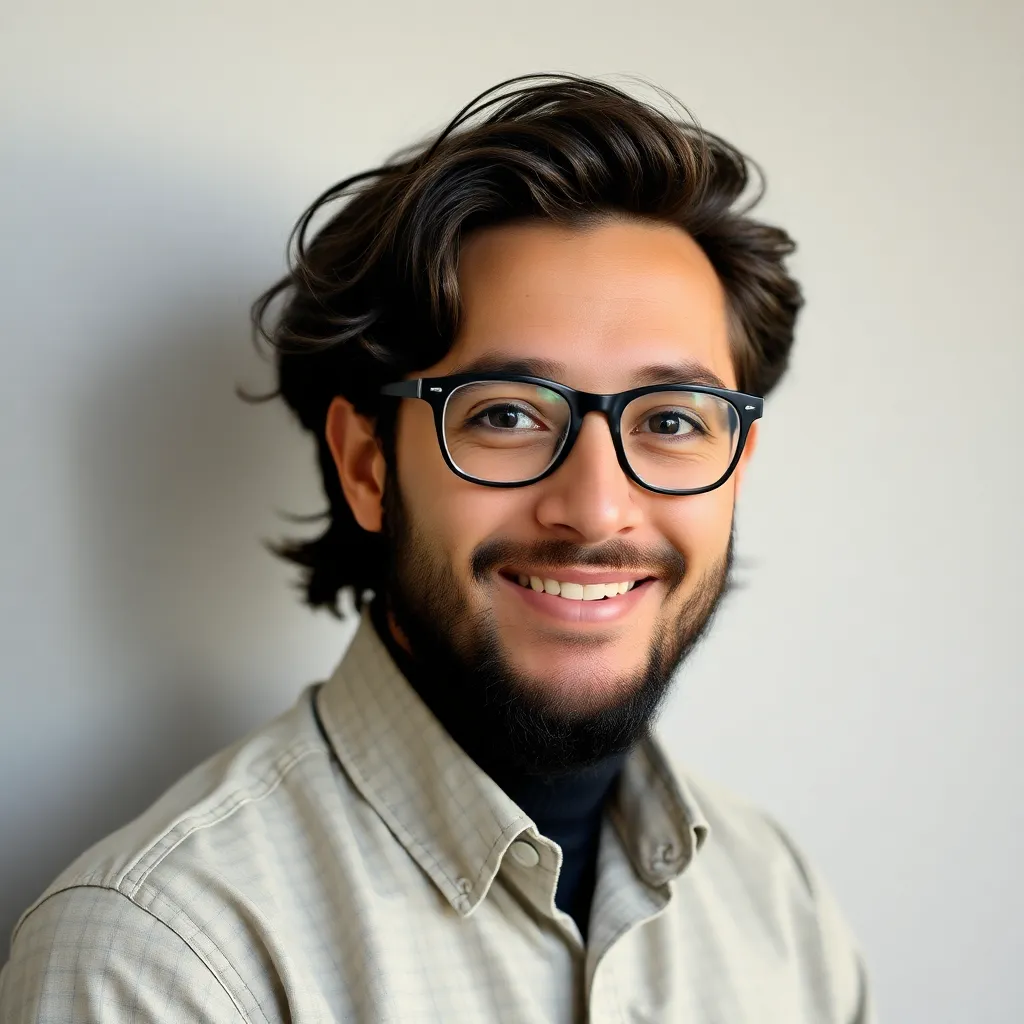
News Leon
Mar 18, 2025 · 6 min read
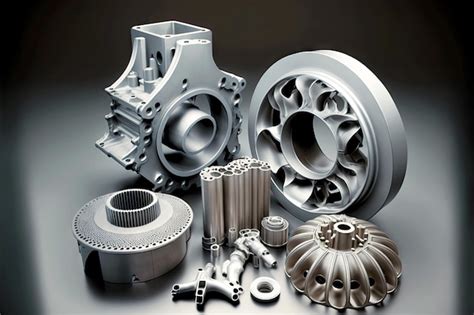
Table of Contents
For Every Part Produced by a Factory: A Deep Dive into Manufacturing Efficiency and Quality Control
The hum of machinery, the rhythmic clang of metal, the precise movements of robotic arms – these are the hallmarks of a modern factory. But beneath the surface lies a complex web of processes, each meticulously designed to ensure that for every part produced, quality, efficiency, and cost-effectiveness are paramount. This article will explore the multifaceted journey of a single part, from initial design to final delivery, highlighting the crucial steps involved in ensuring flawless manufacturing.
From Blueprint to Reality: The Design and Engineering Phase
Before a single part is even conceived, extensive design and engineering work lays the groundwork for success. This phase is critical for determining the part's functionality, material selection, manufacturing process, and overall cost-effectiveness.
Detailed Specifications and Design for Manufacturing (DFM):
This initial stage involves creating detailed specifications for the part. Every dimension, tolerance, material property, and finish is meticulously documented. Crucially, Design for Manufacturing (DFM) principles are applied. DFM is a crucial methodology that considers the manufacturing process from the very beginning of the design phase. It focuses on selecting materials and designs that are easily and cost-effectively produced using available machinery and techniques. Ignoring DFM can lead to significant delays, increased costs, and even the impossibility of producing the part.
Material Selection: A Balancing Act:
The choice of material directly impacts the part's properties, performance, and cost. Engineers carefully consider factors such as strength, durability, weight, corrosion resistance, and cost-effectiveness. Common materials include metals (steel, aluminum, titanium), plastics (polypropylene, ABS, nylon), and composites (carbon fiber, fiberglass). The selection is always a compromise, balancing the ideal properties with the realities of manufacturing and budget constraints.
Prototyping and Testing:
After the design is finalized, prototypes are created and rigorously tested. This stage often involves 3D printing for rapid prototyping, followed by testing for functionality, durability, and compliance with specifications. This iterative process allows engineers to identify and rectify any design flaws before mass production begins, significantly reducing the risk of costly mistakes later on.
The Manufacturing Process: Precision and Efficiency
Once the design is approved, the manufacturing process begins. This stage encompasses a diverse range of techniques, each tailored to the specific part and material.
Machining:
Machining involves using tools to shape and remove material from a workpiece. Common machining processes include milling, turning, drilling, and grinding. CNC (Computer Numerical Control) machines offer high precision and repeatability, essential for producing parts with tight tolerances. Modern CNC machines are often integrated with automated systems for enhanced efficiency.
Casting:
Casting involves pouring molten material into a mold, allowing it to solidify and form the desired shape. This is a cost-effective method for producing complex shapes in high volumes. Different casting techniques exist, including sand casting, die casting, and investment casting, each with its own advantages and limitations.
Forging:
Forging involves shaping metal by applying compressive forces. This process creates strong and durable parts with excellent mechanical properties. Forging techniques range from open-die forging to closed-die forging, offering varying levels of precision and complexity.
Additive Manufacturing (3D Printing):
Additive manufacturing, or 3D printing, is a rapidly evolving technology that builds parts layer by layer from a digital design. This offers significant advantages in prototyping and producing complex geometries that would be difficult or impossible to create using traditional methods. While not yet as cost-effective as traditional methods for mass production in all cases, 3D printing continues to advance rapidly.
Assembly and Sub-Assemblies:
Many parts require assembly, either as a standalone component or as part of a larger sub-assembly. This can involve manual assembly, automated assembly lines, or a combination of both. Precise assembly techniques are crucial to ensure the part functions as intended.
Quality Control: Ensuring Perfection in Every Part
Quality control is an integral part of the manufacturing process, ensuring every part meets the specified standards.
In-Process Inspection:
Inspections are carried out at various stages throughout the manufacturing process. This involves visual inspection, dimensional measurements, and material testing. Early detection of defects prevents the propagation of faulty parts through the production line.
Statistical Process Control (SPC):
SPC uses statistical methods to monitor and control the manufacturing process. By tracking key parameters and identifying trends, manufacturers can quickly identify and correct any deviations from the desired specifications. This proactive approach ensures consistent quality throughout the production run.
Non-Destructive Testing (NDT):
NDT methods examine parts without causing damage. Techniques like ultrasonic testing, radiographic testing, and magnetic particle testing are used to detect internal flaws, such as cracks or voids, that might not be visible through visual inspection. This is particularly crucial for parts subjected to high stress or critical applications.
Final Inspection and Testing:
After the manufacturing process is complete, a final inspection is conducted. This comprehensive check ensures the part meets all specifications and is free from defects. Depending on the application, this might include functional testing, performance testing, and environmental testing.
Packaging, Logistics, and Delivery: The Final Mile
Once a part passes final inspection, it's carefully packaged for transport. Packaging protects the part from damage during shipping and handling. The choice of packaging material depends on factors like the part's fragility, size, and transportation method.
Efficient logistics are crucial for timely delivery. This involves careful planning of transportation routes, warehousing, and inventory management. Effective tracking systems monitor the part's journey from the factory to the customer. Modern supply chain management systems integrate all these aspects for seamless and efficient delivery.
Continuous Improvement: The Pursuit of Excellence
The pursuit of perfection is an ongoing process. Continuous improvement initiatives, such as Lean Manufacturing and Six Sigma, aim to optimize every aspect of the manufacturing process, maximizing efficiency and minimizing waste. Data analysis and feedback mechanisms play a crucial role in identifying areas for improvement and implementing effective changes.
Regular employee training and upskilling also contribute to improved quality and efficiency. A skilled workforce, equipped with the latest technologies and processes, is essential for delivering high-quality parts consistently.
The Future of Manufacturing: Automation, AI, and Sustainability
The manufacturing landscape is constantly evolving, with automation, artificial intelligence (AI), and sustainability driving significant changes. Automated systems are increasing efficiency and precision, while AI-powered systems are enabling predictive maintenance, optimized production planning, and enhanced quality control.
Sustainable manufacturing practices are gaining prominence, with a focus on reducing waste, conserving energy, and using eco-friendly materials. This involves implementing closed-loop systems, adopting circular economy principles, and minimizing the environmental impact of the manufacturing process.
For every part produced by a factory, the journey is a testament to human ingenuity, precision engineering, and a commitment to quality. From initial design to final delivery, every stage is crucial in ensuring the part meets its intended purpose and contributes to the success of the product it forms a part of. As technology advances, the process will only become more sophisticated, efficient, and sustainable, pushing the boundaries of what's possible in the world of manufacturing.
Latest Posts
Latest Posts
-
Word That Has Two Different Meanings
Mar 18, 2025
-
Is Soil A Homogeneous Or Heterogeneous Mixture
Mar 18, 2025
-
What Does Isinstance Do In Python
Mar 18, 2025
-
What Is The Difference Between Political Parties And Interest Groups
Mar 18, 2025
-
Electromagnetic Radiation At Its Maximum Wavelength Is
Mar 18, 2025
Related Post
Thank you for visiting our website which covers about For Every Part Produced By A Factory . We hope the information provided has been useful to you. Feel free to contact us if you have any questions or need further assistance. See you next time and don't miss to bookmark.