Dinitrogen Gas Combines With Dihydrogen Gas To Produce Gaseous Ammonia
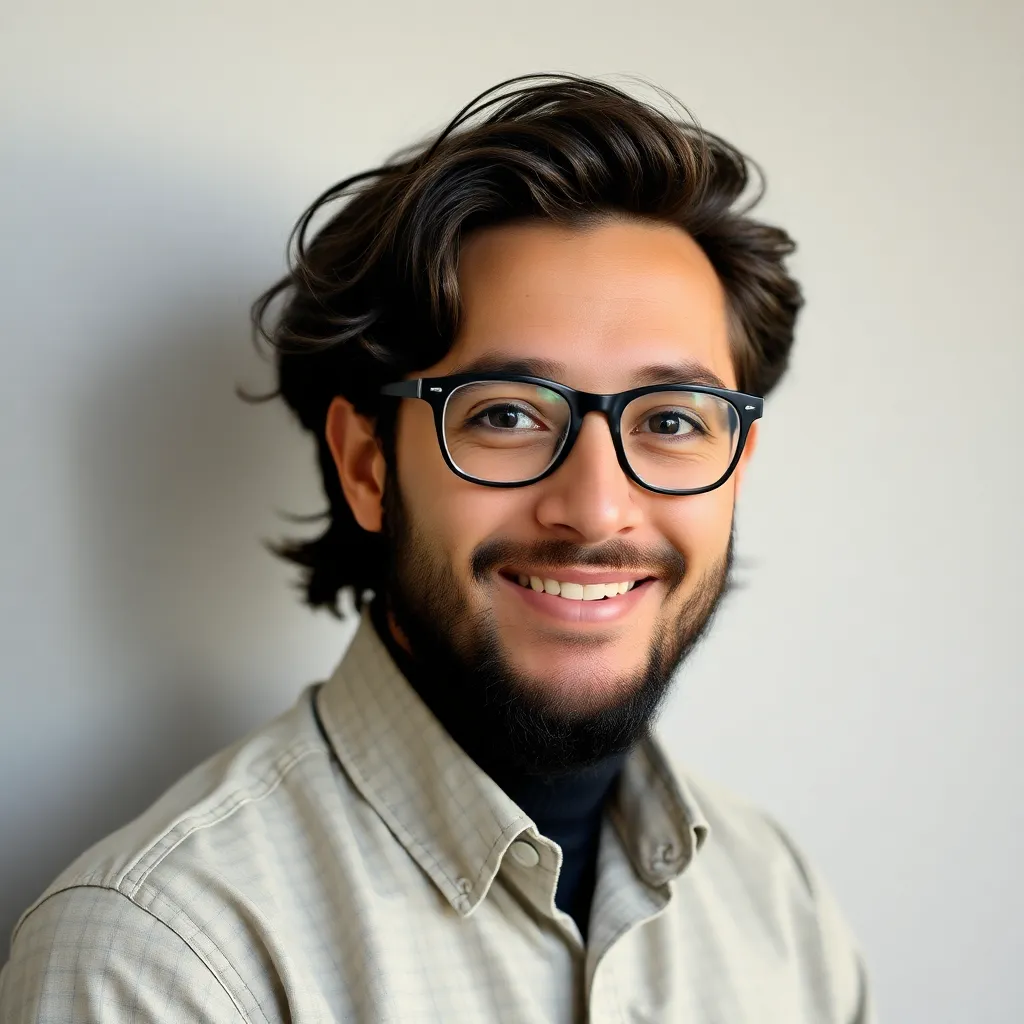
News Leon
Mar 11, 2025 · 6 min read

Table of Contents
Dinitrogen Gas Combining with Dihydrogen Gas to Produce Gaseous Ammonia: A Deep Dive
The Haber-Bosch process, a cornerstone of modern agriculture and industry, hinges on the seemingly simple reaction between dinitrogen (N₂) and dihydrogen (H₂) gases to produce ammonia (NH₃). While the equation – N₂ + 3H₂ ⇌ 2NH₃ – appears straightforward, the intricacies of this reaction, its optimization, and its profound impact on society warrant a detailed exploration. This article delves into the chemistry, thermodynamics, kinetics, industrial applications, and environmental considerations of this vital process.
Understanding the Reaction: A Chemical Perspective
The reaction between dinitrogen and dihydrogen to form ammonia is an example of a reversible reaction, meaning it proceeds in both the forward (formation of ammonia) and reverse (decomposition of ammonia) directions. The equilibrium position, which dictates the relative amounts of reactants and products at a given temperature and pressure, is crucial in determining the efficiency of ammonia production.
The Triple Bond Challenge: Kinetic Barriers
A significant hurdle in this reaction is the exceptionally strong triple bond in the dinitrogen molecule (N₂). Breaking this bond requires a substantial amount of energy, making the reaction kinetically slow at ambient conditions. This is why simply mixing nitrogen and hydrogen gases at room temperature will not result in a noticeable amount of ammonia formation. This kinetic barrier is overcome through the use of a catalyst, typically finely divided iron, which lowers the activation energy of the reaction.
Thermodynamics: Favorable Conditions for Ammonia Production
While the kinetics present a challenge, the thermodynamics of the reaction are generally favorable for ammonia formation, especially at lower temperatures. According to Le Chatelier's principle, increasing the pressure shifts the equilibrium towards the side with fewer moles of gas. Since the reaction produces two moles of ammonia from four moles of reactants, high pressure significantly favors ammonia formation. Conversely, high temperatures favor the reverse reaction (ammonia decomposition). Therefore, a careful balance between temperature and pressure is necessary to optimize ammonia production.
The Haber-Bosch Process: Industrial Implementation
The Haber-Bosch process is the industrial method used for large-scale ammonia synthesis. It involves several key steps:
1. Gas Purification: Ensuring Purity
The starting materials, nitrogen and hydrogen, must be highly purified to avoid catalyst poisoning. Nitrogen is typically obtained from air through fractional distillation, while hydrogen is commonly produced from natural gas via steam reforming. Impurities like carbon monoxide, sulfur compounds, and oxygen must be meticulously removed to maintain catalyst activity and prevent unwanted side reactions.
2. Compression: Achieving High Pressure
The purified gases are compressed to extremely high pressures, typically between 150 and 350 atmospheres. This is a crucial step, as it dramatically shifts the equilibrium towards ammonia formation. High-pressure compressors are energy-intensive, contributing significantly to the process's overall energy consumption.
3. Catalysis: Overcoming the Kinetic Barrier
The compressed gas mixture is then passed over a catalyst bed, usually consisting of finely divided iron with small amounts of promoters like potassium and alumina. The catalyst facilitates the breaking of the N₂ triple bond and subsequent reaction with H₂, significantly accelerating the reaction rate. The optimal temperature for the catalyzed reaction is typically between 400 and 500°C. Lower temperatures would favor the equilibrium but would be too slow kinetically, while higher temperatures would increase the rate but shift the equilibrium towards reactants.
4. Ammonia Separation and Recycling: Optimizing Yield
The ammonia produced is separated from the unreacted nitrogen and hydrogen using a process called liquefaction. Ammonia has a higher boiling point than nitrogen and hydrogen, allowing it to be condensed and separated. The unreacted gases are then recycled back to the reactor to maximize the overall yield. This recycling process is crucial to the economic viability of the process.
The Impact of the Haber-Bosch Process: A Global Perspective
The Haber-Bosch process has had an immeasurable impact on the world, profoundly shaping agriculture, industry, and the global population.
1. Revolutionizing Agriculture: Feeding a Growing Population
The largest application of ammonia is in the production of nitrogenous fertilizers. Ammonia is the basis for the synthesis of a wide range of fertilizers, including urea, ammonium nitrate, and ammonium phosphates. These fertilizers have significantly increased crop yields, enabling us to feed a rapidly growing global population. Without the Haber-Bosch process, it's highly unlikely that the current world population could be sustained.
2. Industrial Applications: Beyond Fertilizers
Beyond fertilizers, ammonia finds application in various industrial processes. It's used in the production of nitric acid, a crucial component in the manufacture of explosives, plastics, and fibers. Ammonia is also utilized in the production of polymers, pharmaceuticals, and cleaning agents.
3. Energy Consumption and Environmental Concerns: A Balancing Act
The Haber-Bosch process is highly energy-intensive, consuming a significant portion of the world's natural gas production. This energy consumption contributes to greenhouse gas emissions, a major concern in the context of climate change. Furthermore, the production and use of nitrogen fertilizers can lead to environmental problems, including water pollution (eutrophication) and nitrous oxide emissions (a potent greenhouse gas).
Optimizing the Haber-Bosch Process: Future Directions
The ongoing search for more efficient and sustainable versions of the Haber-Bosch process is a vital area of research. Several strategies are being pursued:
1. Improving Catalyst Efficiency: Enhancing Catalytic Activity
Research efforts focus on developing more efficient catalysts that can operate at lower temperatures and pressures, reducing energy consumption and greenhouse gas emissions. This involves exploring new catalyst materials and modifying existing ones to enhance their activity and selectivity.
2. Alternative Hydrogen Sources: Reducing Reliance on Fossil Fuels
The current reliance on natural gas for hydrogen production contributes significantly to the environmental footprint of the Haber-Bosch process. Research is underway to explore alternative, more sustainable sources of hydrogen, such as electrolysis powered by renewable energy sources like solar and wind.
3. Process Intensification: Minimizing Environmental Impact
Researchers are exploring innovative reactor designs and process intensification techniques to minimize energy consumption and waste generation. This includes the development of microreactors, membrane reactors, and other advanced reactor technologies.
4. Electrochemical Ammonia Synthesis: A Novel Approach
Electrochemical synthesis of ammonia offers a promising pathway for reducing energy consumption and carbon emissions. This method utilizes electricity to directly convert nitrogen and hydrogen into ammonia at lower temperatures and pressures, potentially bypassing the need for high-pressure compressors and reducing reliance on fossil fuels.
Conclusion: A Legacy of Innovation and Challenges Ahead
The Haber-Bosch process, despite its environmental drawbacks, remains a landmark achievement in chemical engineering and industrial chemistry. Its impact on global food security and industrial development is undeniable. However, the ongoing challenges related to energy consumption and environmental impact necessitate continuous research and development efforts to make ammonia synthesis more sustainable. The future of the Haber-Bosch process lies in optimizing its efficiency, minimizing its environmental footprint, and transitioning towards more sustainable sources of energy and feedstock. The ongoing innovations in catalysis, reactor design, and renewable energy integration will play a crucial role in shaping the future of ammonia production and its contribution to a sustainable world.
Latest Posts
Related Post
Thank you for visiting our website which covers about Dinitrogen Gas Combines With Dihydrogen Gas To Produce Gaseous Ammonia . We hope the information provided has been useful to you. Feel free to contact us if you have any questions or need further assistance. See you next time and don't miss to bookmark.