Difference Between Ac And Dc Motors
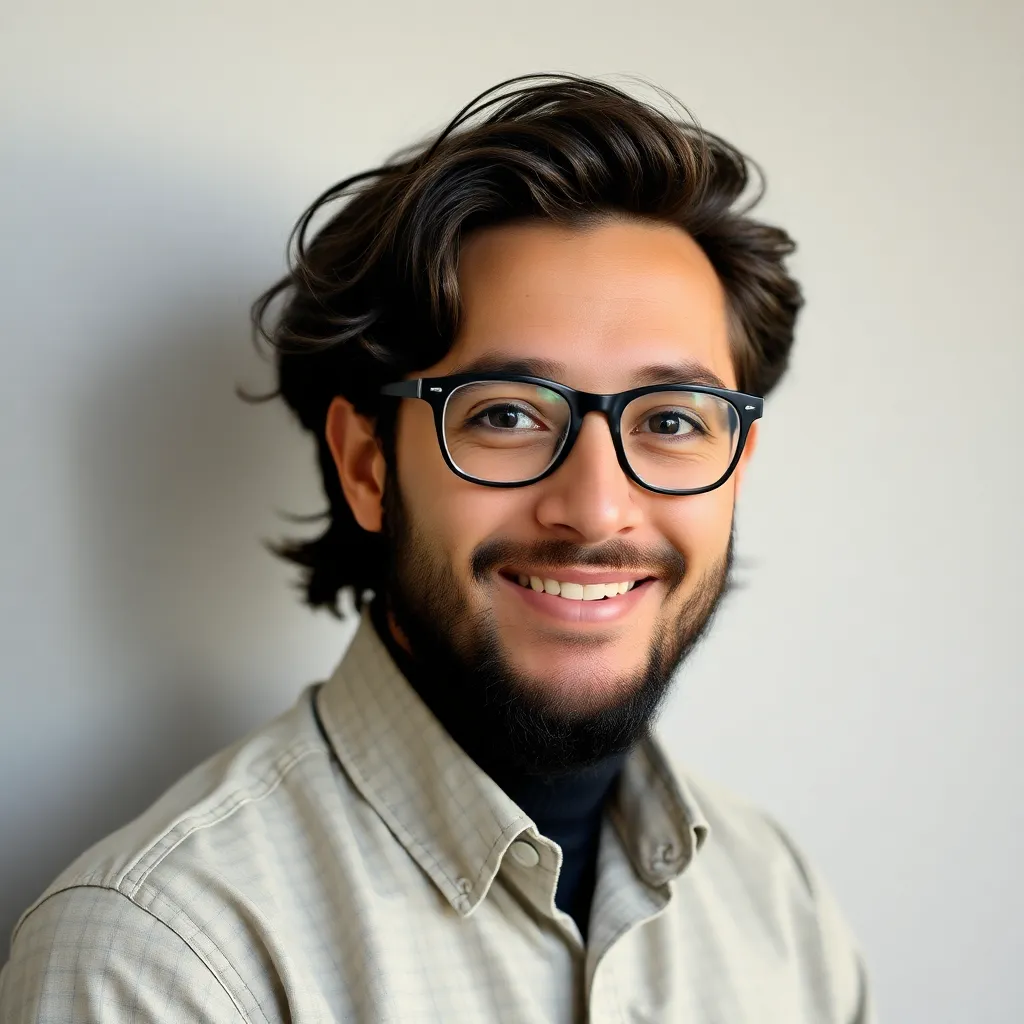
News Leon
Apr 26, 2025 · 7 min read

Table of Contents
AC vs. DC Motors: A Comprehensive Guide to Understanding the Differences
Choosing the right motor for your application can be a daunting task, especially when faced with the fundamental difference between AC and DC motors. This comprehensive guide delves deep into the distinctions between these two powerhouses, exploring their operating principles, advantages, disadvantages, and typical applications. By the end, you'll have a firm grasp of the nuances that differentiate AC and DC motors, empowering you to make informed decisions for your specific needs.
Understanding the Fundamentals: AC vs. DC Power
Before diving into the specifics of motor types, it’s crucial to understand the core difference between alternating current (AC) and direct current (DC) electricity.
Alternating Current (AC)
AC power is characterized by its periodic reversal of current direction. The voltage and current fluctuate sinusoidally, completing a full cycle (from positive to negative and back) at a specific frequency, usually 50 or 60 Hertz (Hz). This cyclical nature of AC power is a defining factor in how AC motors operate.
Direct Current (DC)
In contrast, DC power flows in one consistent direction. The voltage and current remain relatively constant, without the periodic reversals seen in AC. This unidirectional flow simplifies the construction and operation of DC motors.
AC Motor Types: Exploring the Variety
The world of AC motors is diverse, with several key types each boasting unique characteristics. The most common include:
1. Induction Motors (Asynchronous Motors)
These are the workhorses of the AC motor world, renowned for their robustness, simplicity, and cost-effectiveness. Induction motors operate on the principle of electromagnetic induction: a rotating magnetic field in the stator (stationary part) induces current in the rotor (rotating part), creating torque and rotation. They are further categorized into:
- Squirrel-cage induction motors: These have a robust, simple rotor construction resembling a squirrel cage, offering high reliability and low maintenance. They're widely used in various industrial and household applications.
- Wound-rotor induction motors: These feature a more complex rotor with windings and slip rings, allowing for speed control and soft starting. However, they are more expensive and require more maintenance.
Advantages of Induction Motors:
- High reliability and robustness: Simple construction leads to minimal wear and tear.
- Low maintenance: Few moving parts reduce the need for regular servicing.
- Cost-effective: Mass production keeps costs relatively low.
- Wide range of power ratings: Available in a vast array of sizes and power capacities.
Disadvantages of Induction Motors:
- Difficult to control speed precisely: Speed regulation is often limited.
- Lower efficiency at low loads: Performance can suffer when operating below their rated capacity.
- High starting current: Can cause issues with power supply systems.
2. Synchronous Motors
Synchronous motors run at a constant speed synchronized with the frequency of the AC power supply. This makes them ideal for applications requiring precise speed control, like clocks and timing mechanisms. They require a separate excitation source for their magnetic field.
Advantages of Synchronous Motors:
- Precise speed control: Maintain a constant speed regardless of load variations.
- High efficiency at full load: Operate efficiently under normal operating conditions.
- High power factor: Contribute positively to the overall power system.
Disadvantages of Synchronous Motors:
- Complex construction and higher cost: More intricate design leads to increased manufacturing costs.
- Difficult to start: Often require specialized starting mechanisms.
- Less robust compared to induction motors: Prone to damage from overload conditions.
3. Single-Phase vs. Three-Phase AC Motors
AC motors can also be classified based on the number of phases in the power supply:
- Single-phase motors: These are commonly used in household appliances due to their compatibility with standard household power. However, they generally have lower power ratings and are less efficient than three-phase motors.
- Three-phase motors: These are prevalent in industrial settings, offering higher power, efficiency, and better starting torque.
DC Motor Types: A Closer Look
DC motors, while simpler in concept compared to their AC counterparts, also come in several variations, each suited for specific applications. The major types include:
1. Brushed DC Motors
These motors use brushes and commutators to convert the DC power into a rotating magnetic field. The brushes make physical contact with the commutator, creating the necessary switching action.
Advantages of Brushed DC Motors:
- Simple construction and low cost: Relatively easy to manufacture and maintain.
- Easy speed control: Speed can be regulated by adjusting the voltage or current.
- High starting torque: Excellent for applications requiring immediate power.
Disadvantages of Brushed DC Motors:
- Limited lifespan: Mechanical wear and tear on the brushes and commutator reduce the lifespan.
- Maintenance required: Brushes need periodic replacement.
- Sparking and noise: The brush-commutator contact can cause sparking and noise.
2. Brushless DC Motors (BLDC Motors)
These motors eliminate the brushes and commutators, replacing them with electronic commutation. This leads to significant advantages, including increased efficiency, longer lifespan, and quieter operation.
Advantages of Brushless DC Motors:
- Longer lifespan: No mechanical wear and tear from brushes and commutators.
- Higher efficiency: Reduced energy loss due to the absence of friction.
- Quiet operation: Significantly less noise compared to brushed DC motors.
- Precise speed control: Excellent control capabilities due to electronic commutation.
Disadvantages of Brushless DC Motors:
- Higher cost: More complex design and electronic components increase the manufacturing cost.
- Requires electronic controller: Need a sophisticated controller for operation.
3. Stepper Motors
Stepper motors provide precise rotational control, moving in discrete steps rather than continuous rotation. This makes them ideal for applications requiring precise positioning, such as printers and robotics.
Advantages of Stepper Motors:
- Precise positioning: Move in exact steps, allowing accurate control.
- Open-loop control: Position can be controlled without feedback sensors, simplifying design.
- High holding torque: Can maintain position even without power.
Disadvantages of Stepper Motors:
- Lower speed and torque compared to other DC motors: Not suitable for high-speed, high-torque applications.
- Resonance issues: Can experience vibrations and instability at certain speeds.
AC vs. DC Motors: A Comparative Overview
Feature | AC Motors | DC Motors |
---|---|---|
Power Supply | Alternating Current (AC) | Direct Current (DC) |
Construction | Generally more complex | Generally simpler |
Maintenance | Lower maintenance requirement (Induction) | Higher maintenance for brushed motors |
Speed Control | More difficult, often limited | Easier to control, particularly in DC motors |
Cost | Typically lower (Induction) | Can be higher (BLDC motors) |
Efficiency | Can be high (Synchronous) | Can be high (BLDC motors) |
Starting Torque | Lower (Induction), High (Synchronous) | Generally high |
Lifespan | Long (Induction) | Shorter for brushed, longer for brushless |
Applications | Industrial machinery, fans, pumps | Robotics, automotive, appliances |
Choosing the Right Motor: Key Considerations
Selecting the appropriate motor depends on several factors, including:
- Power requirements: Determine the required horsepower or torque.
- Speed control: Consider whether precise speed regulation is necessary.
- Starting torque: Assess the need for high starting torque.
- Operating environment: Account for temperature, humidity, and other environmental factors.
- Budget: Balance performance requirements with cost considerations.
- Maintenance: Evaluate the level of maintenance you're willing to undertake.
Conclusion
The choice between AC and DC motors is not a simple one, but rather a careful consideration of the specific needs of your application. While AC motors dominate industrial settings due to their robustness and cost-effectiveness, DC motors—especially brushless DC motors—offer superior control and efficiency in many applications. By understanding the strengths and weaknesses of each type, you can select the optimal motor for your project, ensuring optimal performance and longevity. This detailed exploration of AC and DC motors provides a strong foundation for making informed decisions, whether you're designing a complex industrial system or a small household appliance. Remember to meticulously weigh your specific requirements before making your final choice.
Latest Posts
Latest Posts
-
Do Weak Acids Have Strong Conjugate Bases
Apr 26, 2025
-
Chemical Equation For The Combustion Of Methane
Apr 26, 2025
-
Cells Contain One Set Of Chromosomes
Apr 26, 2025
-
Complementary Angles Examples In Real Life
Apr 26, 2025
-
Frog Is Carnivore Or Omnivore Or Herbivore
Apr 26, 2025
Related Post
Thank you for visiting our website which covers about Difference Between Ac And Dc Motors . We hope the information provided has been useful to you. Feel free to contact us if you have any questions or need further assistance. See you next time and don't miss to bookmark.