Difference Between Ac And Dc Machines
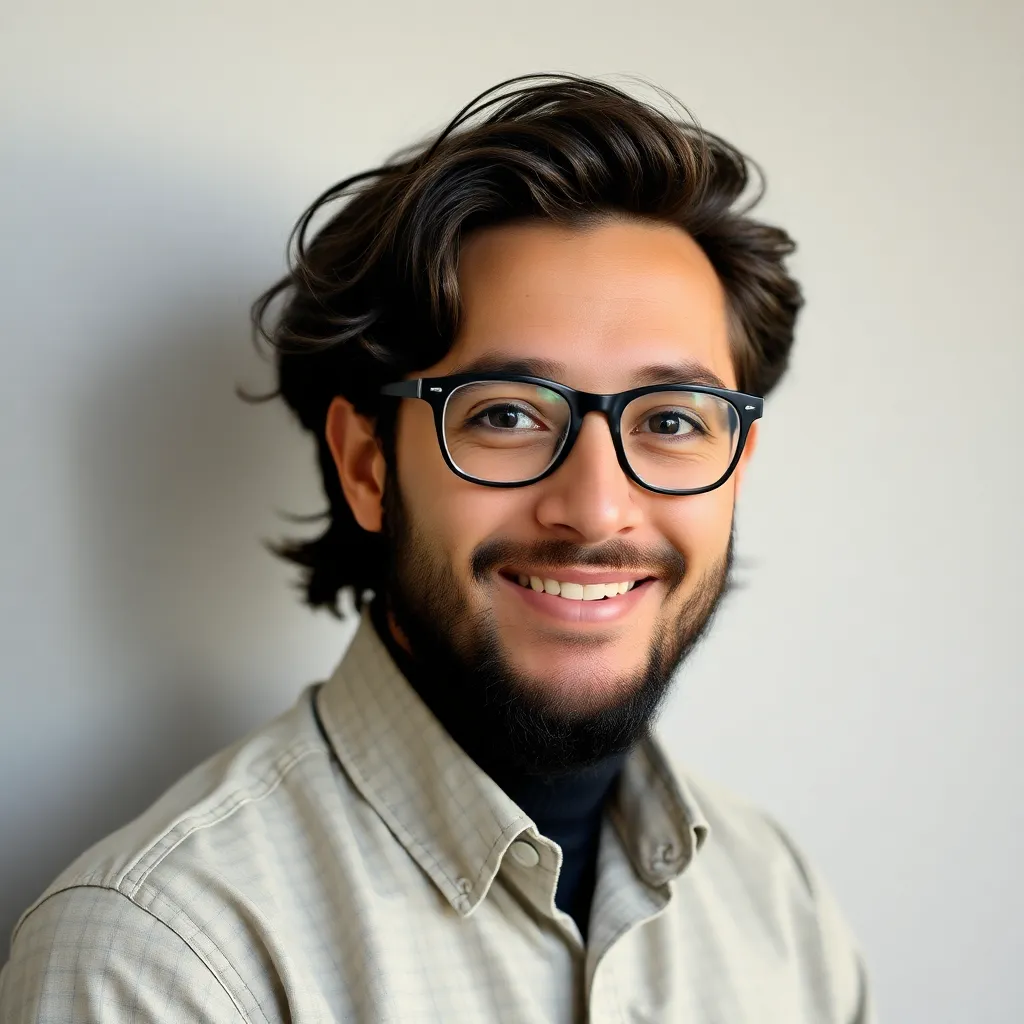
News Leon
Mar 14, 2025 · 7 min read
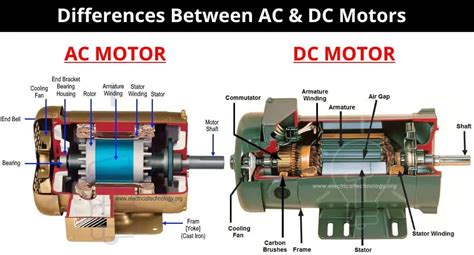
Table of Contents
AC vs. DC Machines: A Deep Dive into the Differences
The world of electrical machines is broadly divided into two categories: Alternating Current (AC) and Direct Current (DC) machines. While both serve the purpose of converting electrical energy into mechanical energy (motors) or vice-versa (generators), they differ significantly in their construction, operation, and applications. Understanding these differences is crucial for anyone working with electrical systems, from engineers to technicians. This comprehensive guide will explore the key distinctions between AC and DC machines, providing a detailed analysis of their operational principles, advantages, and disadvantages.
Fundamental Differences: AC vs. DC
The most fundamental difference lies in the nature of the current they utilize:
-
AC Machines: Operate on alternating current, where the direction of current flow reverses periodically. This reversal typically occurs 50 or 60 times per second, depending on the regional power grid. This cyclical change is characterized by a sinusoidal waveform.
-
DC Machines: Operate on direct current, where the current flows in only one direction. While the magnitude of the current might fluctuate, the direction remains constant.
This seemingly simple distinction leads to a cascade of differences in their design, operation, and characteristics.
Constructional Differences: A Closer Look
The internal construction of AC and DC machines reflects their differing current requirements:
AC Machine Construction:
-
Stator: The stationary part of the machine, containing the windings that produce the rotating magnetic field. The stator's construction varies depending on the specific type of AC machine (e.g., induction motor, synchronous motor). It often utilizes laminated steel cores to minimize eddy current losses.
-
Rotor: The rotating part of the machine, which interacts with the stator's magnetic field to produce mechanical torque. Rotor designs also differ greatly; induction motor rotors can be squirrel-cage or wound-rotor types, while synchronous motor rotors have salient or cylindrical poles.
-
Simplified Commutation: AC machines generally do not require commutators, simplifying their construction and reducing maintenance needs. The alternating current naturally reverses, eliminating the need for a mechanical switching mechanism.
DC Machine Construction:
-
Stator: The stationary part houses the field windings which create the magnetic field. These windings can be separately excited, shunt excited, series excited, or a combination thereof.
-
Rotor (Armature): The rotating part containing the armature windings. These windings cut the magnetic field lines to generate voltage (in generators) or receive current to produce torque (in motors).
-
Commutator: A crucial component in DC machines, the commutator is a segmented cylindrical structure made of copper segments. It's connected to the armature windings and facilitates the conversion of AC voltage induced in the armature to DC voltage at the terminals. This is achieved through the use of brushes, which make sliding contact with the commutator segments. This process is known as mechanical commutation.
Operational Principles: How They Work
The operational principles of AC and DC machines differ significantly due to their contrasting current types and constructions:
AC Machine Operation:
The operation of an AC machine depends on the principle of electromagnetic induction. A rotating magnetic field in the stator induces currents in the rotor windings (in induction motors), or a synchronized rotating field in the rotor interacts with the stator's field (in synchronous motors). This interaction produces a torque that drives the rotor. Different types of AC machines operate on slightly different principles, but the underlying concept remains the same.
Types of AC Machines: Several key types exist, each with specific operating characteristics:
-
Induction Motors: The most common type of AC motor, known for its robustness, simplicity, and low cost. They operate on the principle of electromagnetic induction, without requiring external excitation for the rotor.
-
Synchronous Motors: Run at a constant speed synchronized with the frequency of the supply voltage. They often require separate excitation for the rotor. These motors are used in applications requiring precise speed control.
-
Stepper Motors: Used for precise positioning applications, these motors move in discrete steps rather than continuously.
DC Machine Operation:
DC machines operate on the principle of interaction between a magnetic field and current-carrying conductors. The field windings create a magnetic field, and the current flowing through the armature windings interacts with this field, producing torque. The commutator ensures that the current in the armature windings always flows in a direction that produces a unidirectional torque.
Types of DC Machines: The type of DC machine is determined by the way the field windings are connected:
-
Separately Excited DC Machines: The field windings are powered by a separate DC source, allowing for independent control of field current and speed.
-
Shunt-Wound DC Machines: The field windings are connected in parallel with the armature. They exhibit relatively constant speed characteristics.
-
Series-Wound DC Machines: The field windings are connected in series with the armature. They have high starting torque but varying speed characteristics.
-
Compound-Wound DC Machines: A combination of shunt and series windings, providing characteristics of both.
Advantages and Disadvantages: Weighing the Options
Both AC and DC machines offer unique advantages and disadvantages, making them suitable for different applications:
AC Machine Advantages:
- Lower Maintenance: Simpler construction, typically lacking commutators and brushes, resulting in less maintenance.
- Higher Efficiency: Often exhibit higher efficiency, particularly at higher power ratings.
- Simplicity of Design: Generally simpler to construct and manufacture, resulting in lower costs.
- Robustness: Typically more rugged and capable of operating in harsher environments.
AC Machine Disadvantages:
- Speed Control: Can be more challenging to control speed compared to DC motors.
- Starting Torque: Some types (like induction motors) may have lower starting torque.
- Power Factor: Can exhibit lower power factors, leading to increased power consumption.
DC Machine Advantages:
- Precise Speed Control: Excellent speed control capabilities, achieved through field current adjustment.
- High Starting Torque: Generally offer higher starting torque compared to some AC motors.
- Simple Starting: Relatively simple to start and control.
DC Machine Disadvantages:
- Higher Maintenance: The commutator and brushes require regular maintenance and replacement.
- Lower Efficiency: Can be less efficient compared to AC machines, especially at higher power ratings.
- Complex Construction: More complex construction, leading to higher manufacturing costs.
- Sparking at the Commutator: Can produce sparking at high speeds or loads, leading to wear and tear.
Applications: Where They Shine
The choice between AC and DC machines depends heavily on the specific application requirements:
AC Machine Applications:
- Industrial Drives: Widely used in industrial applications such as pumps, compressors, and conveyors. Induction motors dominate this sector due to their robustness and simplicity.
- Household Appliances: Found in many household appliances, including refrigerators, washing machines, and fans.
- Power Generation: Synchronous generators are the workhorses of power generation, converting mechanical energy into electrical energy in power plants.
- High-Power Applications: AC motors are often preferred for high-power applications due to their efficiency and robustness.
DC Machine Applications:
- Precise Motion Control: Used in applications requiring precise speed and position control, such as robotics, machine tools, and elevators.
- Electric Vehicles: DC motors are used in some electric vehicles due to their precise speed control.
- Battery-Powered Equipment: Ideal for battery-powered equipment due to their efficient operation at lower voltages.
- Low-Speed, High-Torque Applications: Their high starting torque makes them suitable for applications needing significant torque at low speeds.
Conclusion: Choosing the Right Machine
The choice between AC and DC machines involves carefully weighing the advantages and disadvantages of each type against the specific requirements of the application. While AC machines generally offer higher efficiency, lower maintenance, and simpler design, DC machines excel in applications requiring precise speed control and high starting torque. A comprehensive understanding of these differences is crucial for selecting the optimal machine for any given task. The ongoing advancements in power electronics are also blurring the lines somewhat, with AC drives now offering sophisticated control capabilities that were once the exclusive domain of DC motors. However, the fundamental differences in their operating principles and constructions remain significant.
Latest Posts
Latest Posts
-
Which Of The Following Needs A Proof
Mar 14, 2025
-
Pure Substances Are Made Of Only One Type Of
Mar 14, 2025
-
A Dpt Vaccination Is An Example Of
Mar 14, 2025
-
Whats The Difference Between An Enzyme And A Hormone
Mar 14, 2025
-
An Alloy With One Of The Constituents Being Mercury
Mar 14, 2025
Related Post
Thank you for visiting our website which covers about Difference Between Ac And Dc Machines . We hope the information provided has been useful to you. Feel free to contact us if you have any questions or need further assistance. See you next time and don't miss to bookmark.