Difference Between Ac And Dc Electric Motor
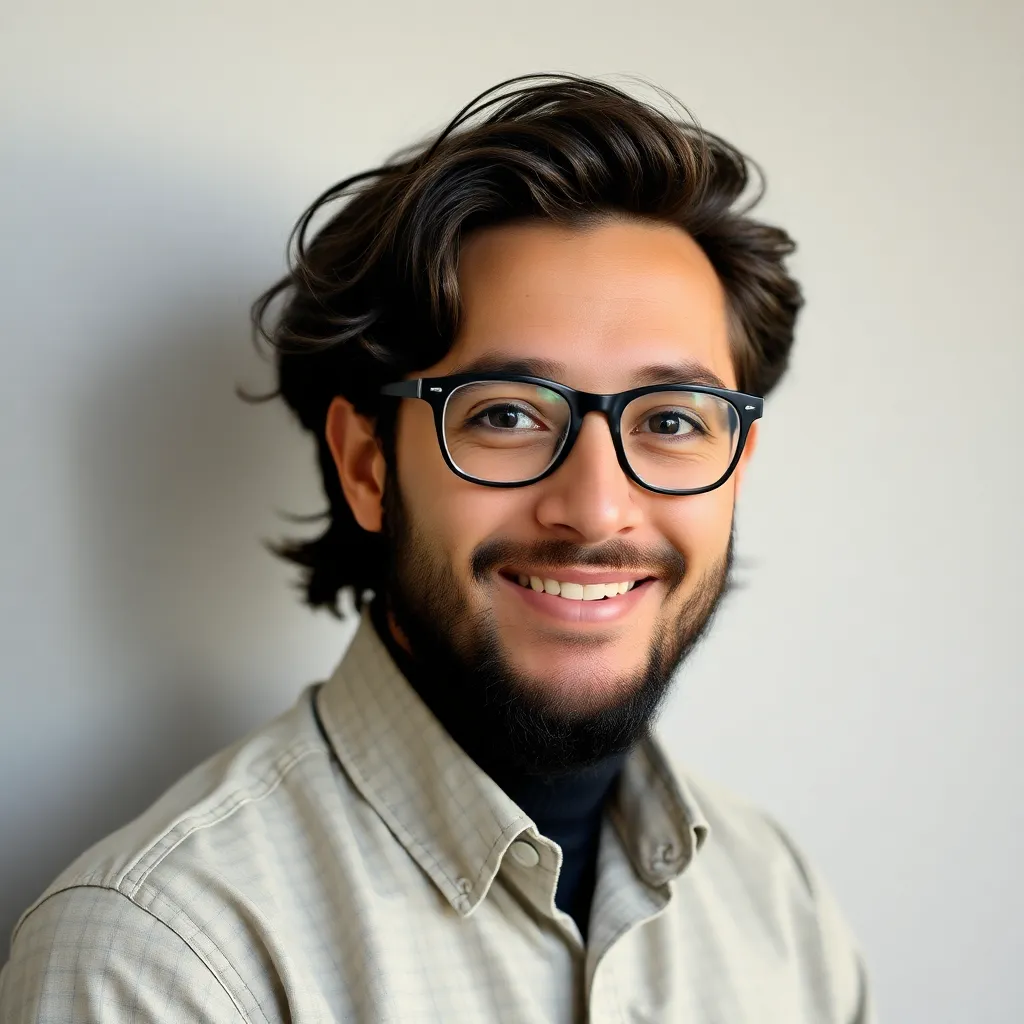
News Leon
Apr 18, 2025 · 6 min read

Table of Contents
AC vs. DC Electric Motors: A Comprehensive Comparison
Electric motors are the workhorses of modern industry and everyday life, powering everything from electric vehicles and industrial machinery to household appliances and computer peripherals. Understanding the fundamental differences between alternating current (AC) and direct current (DC) motors is crucial for selecting the right motor for a specific application. This article delves into the core distinctions between these two motor types, exploring their operating principles, advantages, disadvantages, and typical applications.
Fundamental Differences: AC vs. DC
The most significant difference between AC and DC motors lies in the type of electrical current they utilize. AC motors operate on alternating current, where the direction of current flow reverses periodically. DC motors, conversely, run on direct current, where the current flows in a single direction. This seemingly simple distinction leads to significant differences in their design, operation, and characteristics.
1. Power Supply and Commutation:
-
AC Motors: These motors are designed to operate directly from the AC mains supply, making them readily available and relatively inexpensive to use. However, the alternating current requires a specific design to induce continuous rotation, usually employing techniques like induction or synchronous principles.
-
DC Motors: These motors traditionally require a DC power source. While DC power sources are readily available in many applications, they may need rectification and filtering from the AC mains supply, adding to the cost and complexity. The commutation process (switching the current direction in the rotor) is also integral to their operation.
2. Operating Principles:
-
AC Motors: There are two primary types of AC motors: induction motors and synchronous motors. Induction motors utilize the principle of electromagnetic induction to create a rotating magnetic field that interacts with the rotor, inducing current and causing it to rotate. Synchronous motors, on the other hand, require an external DC excitation source to synchronize the rotor's rotation with the rotating magnetic field of the stator.
-
DC Motors: DC motors rely on the interaction between a magnetic field generated by the stator (field winding) and the armature (rotor winding). The armature carries the current, and the interaction between these magnetic fields produces torque and rotation. The commutation system in DC motors ensures that the current in the armature winding is switched appropriately to maintain continuous rotation.
3. Speed Control:
-
AC Motors: Speed control in AC motors can be achieved through various methods, including adjusting the frequency of the AC power supply (using Variable Frequency Drives or VFDs) or varying the voltage. However, the ease of speed control can vary depending on the type of AC motor. Induction motors, for instance, are less easily controlled than synchronous motors.
-
DC Motors: DC motors offer excellent speed control capabilities, typically through adjusting the voltage applied to the armature or the field winding. This makes them highly adaptable for applications requiring precise speed regulation.
4. Torque Characteristics:
-
AC Motors: AC motors generally provide high starting torque, particularly induction motors, making them suitable for applications requiring high initial force. The torque-speed characteristics vary depending on the type of AC motor and can be influenced by design parameters and control methods.
-
DC Motors: DC motors offer versatile torque characteristics. By adjusting the field current, one can modify the torque-speed curve, allowing for optimized performance across different operating conditions. Certain DC motor designs can provide high starting torque while maintaining smooth operation across a wide speed range.
5. Maintenance:
-
AC Motors: AC motors generally require less maintenance compared to DC motors. Their simple construction and absence of commutators contribute to their lower maintenance needs. However, regular checks for bearing wear and insulation are still recommended.
-
DC Motors: DC motors, especially those with brushed commutators, require more frequent maintenance. The brushes wear down over time and need replacement. The commutator itself can also wear out and may require servicing or replacement. This increased maintenance requirement translates to higher operational costs.
6. Efficiency:
-
AC Motors: AC motors, particularly induction motors, are widely considered to be more efficient than DC motors across a broader range of operating conditions. Advances in AC motor technology have further enhanced their efficiency, making them a preferred choice for many energy-conscious applications.
-
DC Motors: While DC motors can be highly efficient, their efficiency can be affected by factors like brush losses and commutation losses. Nevertheless, advancements in brushless DC motors have significantly improved their efficiency, bridging the gap with AC motors in this regard.
Types of AC Motors and Their Applications:
Several types of AC motors exist, each with its strengths and applications:
-
Induction Motors (Asynchronous Motors): These are the most prevalent type of AC motor. They are robust, relatively simple, and inexpensive. Their wide range of applications includes industrial machinery (pumps, fans, conveyors), household appliances (refrigerators, washing machines), and many other common devices. They are usually preferred in applications where precise speed control isn't critical.
-
Synchronous Motors: These motors run at a speed directly proportional to the frequency of the power supply. They offer high efficiency and constant speed operation but require more complex control systems. Applications include high-precision machinery, power factor correction, and specialized industrial systems.
-
Stepper Motors: Stepper motors rotate in discrete steps rather than continuous rotation. They are frequently used in applications requiring precise positioning control, such as robotics, printing, and computer peripherals.
Types of DC Motors and Their Applications:
Several types of DC motors exist, each suited to different applications:
-
Brushed DC Motors: These motors utilize brushes to transfer current to the rotating armature. They are simple, inexpensive, and offer good speed control. However, the brushes wear out over time, requiring replacement. Applications include smaller appliances, toys, and low-power tools.
-
Brushless DC Motors (BLDC): BLDC motors eliminate the use of brushes, using electronic commutation instead. This results in longer lifespan, higher efficiency, and lower maintenance. They are commonly used in applications requiring high efficiency and precision control, such as electric vehicles, high-performance robotics, and sophisticated industrial systems.
-
Servo Motors: Servo motors are a type of DC motor combined with a feedback control system, typically using a position sensor. They are designed for precise position and speed control and are widely used in robotics, automation systems, and precision machinery.
Choosing Between AC and DC Motors:
Selecting the appropriate motor depends largely on the specific application requirements. Here are some key factors to consider:
-
Power Supply: The availability and type of power supply is a major determinant. AC motors are generally more convenient for direct connection to the mains, while DC motors may require additional power conversion equipment.
-
Speed Control: If precise and variable speed control is crucial, DC motors generally provide better options. However, advances in AC motor control (VFDs) have significantly improved their speed control capabilities.
-
Torque Requirements: Applications demanding high starting torque often favor AC induction motors, while those requiring adjustable torque-speed characteristics might benefit from DC motors.
-
Maintenance Requirements: DC motors with brushes require more frequent maintenance, while AC motors are typically lower maintenance.
-
Cost: AC motors are usually less expensive upfront than DC motors, especially considering the additional cost of power conversion for DC systems.
-
Efficiency: AC motors, particularly induction motors, usually demonstrate higher overall efficiency.
Conclusion:
The choice between AC and DC motors involves a careful consideration of various factors. While both motor types share the common purpose of converting electrical energy into mechanical work, their underlying operating principles, control mechanisms, and performance characteristics exhibit significant differences. Understanding these nuances is essential for engineers and designers in selecting the optimal motor solution for diverse applications, ensuring efficiency, reliability, and optimal performance. The ongoing advancements in both AC and DC motor technologies continue to push the boundaries of performance and efficiency, broadening the range of applications and possibilities for these essential power conversion devices.
Latest Posts
Latest Posts
-
25 Of What Number Is 6
Apr 19, 2025
-
A Demand Curve That Is Horizontal Indicates That The Commodity
Apr 19, 2025
-
The Standard Unit For Measuring Mass Is
Apr 19, 2025
-
Is Melting Candle Wax A Chemical Or Physical Change
Apr 19, 2025
-
Destruction Of Old Rbcs Is A Function Of The
Apr 19, 2025
Related Post
Thank you for visiting our website which covers about Difference Between Ac And Dc Electric Motor . We hope the information provided has been useful to you. Feel free to contact us if you have any questions or need further assistance. See you next time and don't miss to bookmark.