Diff Between Ac And Dc Motor
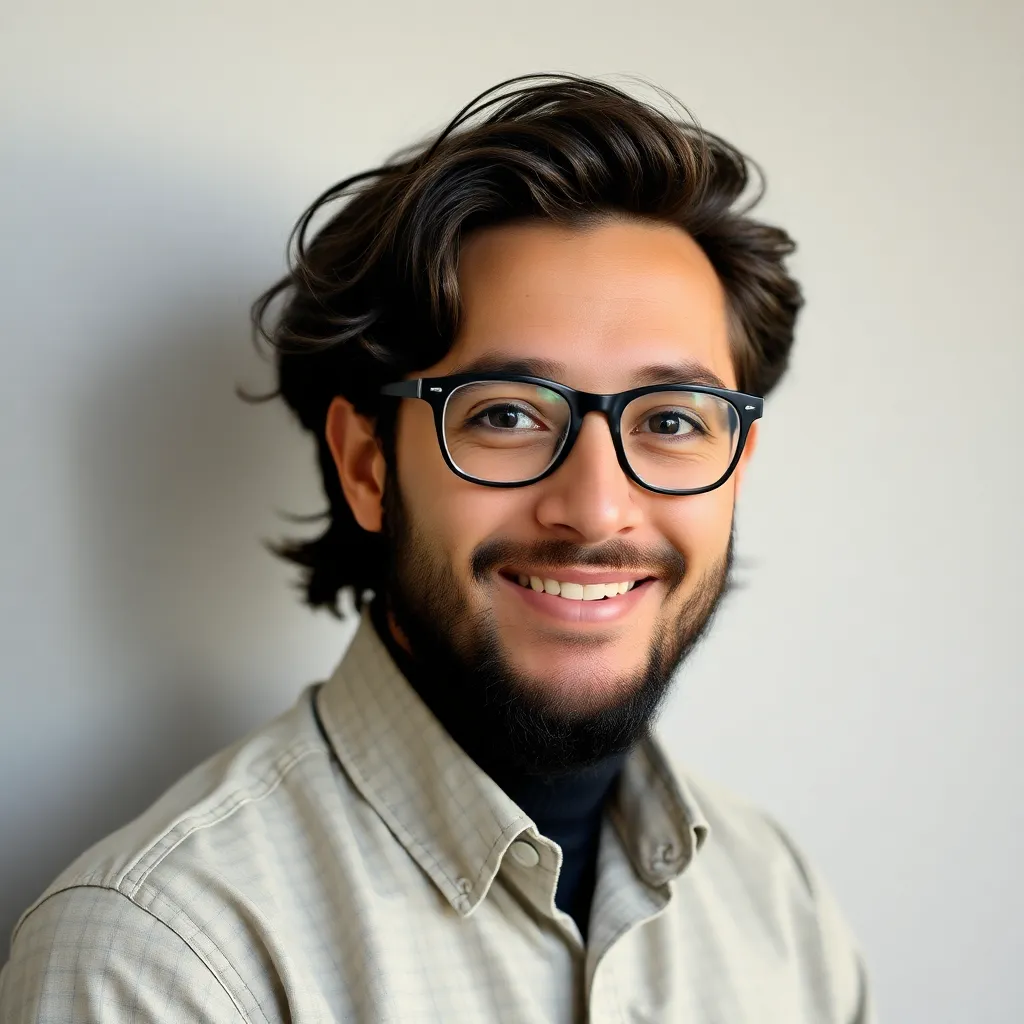
News Leon
Apr 16, 2025 · 6 min read

Table of Contents
AC vs. DC Motors: A Deep Dive into the Differences
Choosing the right motor for your application is crucial. The world of electric motors is vast, but a primary distinction lies between Alternating Current (AC) and Direct Current (DC) motors. While both convert electrical energy into mechanical energy, their underlying principles, construction, and applications differ significantly. This comprehensive guide will delve into the core differences between AC and DC motors, helping you understand their unique strengths and weaknesses.
Understanding AC and DC Power
Before diving into the motor types, let's clarify the fundamental difference between AC and DC electricity.
-
Direct Current (DC): DC electricity flows in one direction, maintaining a constant voltage and current. Batteries and solar panels are prime examples of DC power sources. Think of it as a steady stream of electrons flowing consistently in a single direction.
-
Alternating Current (AC): AC electricity, on the other hand, periodically reverses its direction. The voltage and current fluctuate sinusoidally, meaning they increase and decrease in a wave-like pattern. This is the standard form of electricity supplied to homes and industries. Imagine the electrons surging back and forth.
This seemingly simple difference in current flow profoundly impacts motor design and performance characteristics.
AC Motor Types and Characteristics
AC motors dominate industrial applications due to their robust construction, high power output, and relatively low maintenance requirements. Several types exist, each with specific advantages:
1. Induction Motors (Asynchronous Motors):
These are the most common AC motors, renowned for their simplicity, reliability, and cost-effectiveness. They operate on the principle of electromagnetic induction. A rotating magnetic field in the stator (stationary part) induces current in the rotor (rotating part), causing it to turn. No external electrical connections to the rotor are needed, simplifying their construction and maintenance.
- Advantages: High reliability, low maintenance, simple construction, robust, cost-effective.
- Disadvantages: Lower starting torque compared to DC motors, speed control can be complex and less precise. They typically require variable frequency drives (VFDs) for precise speed control.
2. Synchronous Motors:
Synchronous motors operate at a constant speed, directly proportional to the frequency of the AC power supply. They achieve this by using a rotor that is magnetized or energized to synchronize with the rotating magnetic field of the stator.
- Advantages: Constant speed operation, high efficiency at rated load, power factor correction capabilities.
- Disadvantages: More complex design than induction motors, require a separate excitation source, may not self-start without assistance (often require an auxiliary starting mechanism).
3. Single-Phase AC Motors:
These are commonly found in smaller appliances like fans and pumps. They typically require a capacitor or other starting mechanism to create a rotating magnetic field.
- Advantages: Low cost, suitable for smaller applications.
- Disadvantages: Lower efficiency and power compared to three-phase motors, less robust, more prone to overheating.
DC Motor Types and Characteristics
DC motors are favored in applications requiring precise speed control and high starting torque. Different types cater to specific needs:
1. Brushed DC Motors:
These motors use brushes to transfer electricity from the stator to the commutator on the rotor. The commutator is a segmented cylinder that ensures the rotor maintains its rotation by switching the current direction.
- Advantages: Simple design, high starting torque, excellent speed control, relatively inexpensive.
- Disadvantages: Limited lifespan due to brush wear, mechanical commutation generates sparks, higher maintenance requirements, lower efficiency at higher speeds.
2. Brushless DC Motors (BLDC Motors):
BLDC motors eliminate the need for brushes, using electronic commutation instead. Sensors or hall-effect sensors detect the rotor position, allowing the electronic controller to switch the current to the appropriate stator windings.
- Advantages: Longer lifespan due to no brush wear, higher efficiency, quieter operation, more precise speed control, higher speeds possible.
- Disadvantages: More complex design, require an electronic controller, higher initial cost.
Key Differences Summarized: AC vs. DC Motors
Feature | AC Motor | DC Motor |
---|---|---|
Power Source | Alternating Current (AC) | Direct Current (DC) |
Construction | Generally simpler, more robust | Can range from simple to highly complex |
Starting Torque | Generally lower than DC motors | Generally higher than AC motors |
Speed Control | More complex, often requires VFDs | Generally easier, using voltage or PWM |
Maintenance | Lower maintenance requirements | Higher maintenance (especially brushed types) |
Efficiency | High efficiency at rated load | High efficiency (especially BLDC) |
Cost | Generally lower initial cost | Can range from low (brushed) to high (BLDC) |
Lifespan | Longer lifespan (especially induction) | Shorter lifespan (brushed), longer (BLDC) |
Applications | Industrial applications, high power | Robotics, automotive, precision equipment |
Choosing the Right Motor: Applications and Considerations
The choice between AC and DC motors depends heavily on the specific application requirements. Here’s a breakdown to help you decide:
AC Motor Applications:
-
Industrial Processes: AC motors, especially induction motors, are prevalent in heavy-duty applications like conveyor belts, pumps, fans, compressors, and factory machinery. Their robustness, reliability, and cost-effectiveness make them ideal for demanding environments.
-
High-Power Applications: When significant power is required, AC motors generally offer a more cost-effective solution compared to their DC counterparts.
-
Constant Speed Operations: While precise speed control might require a VFD, synchronous motors excel at maintaining constant speeds.
DC Motor Applications:
-
Robotics and Automation: DC motors, especially brushless DC motors, are widely used in robotics due to their precise speed control and high starting torque.
-
Automotive Industry: DC motors are found in electric vehicles, power windows, and other automotive systems.
-
Precision Equipment: Applications demanding accurate positioning and speed control, such as CNC machines and medical equipment, often leverage DC motors.
-
Portable Devices: Smaller, brushed DC motors find use in various portable tools and appliances.
Advanced Considerations: Speed Control and Efficiency
Both AC and DC motors can be controlled to vary their speed, but the methods differ:
-
AC Motor Speed Control: Variable Frequency Drives (VFDs) are commonly used to control the speed of AC motors by altering the frequency of the power supply. This is a prevalent method for achieving precise speed control in many applications.
-
DC Motor Speed Control: Pulse Width Modulation (PWM) is a common technique to control the speed of DC motors by adjusting the duty cycle of the power supply. For brushed motors, changing the voltage directly affects speed, while brushless motors rely on the electronic controller to manage speed based on PWM or other advanced control algorithms.
Regarding efficiency, while AC motors are generally efficient at their rated load, BLDC motors often exhibit superior efficiency across a wider operating range. Factors such as motor size, load, and control method all affect the overall efficiency.
Conclusion: Making the Right Choice
The selection between AC and DC motors is a multifaceted decision. Understanding their inherent differences, comparing their strengths and weaknesses, and carefully considering the specific requirements of the application are paramount to making the optimal choice. This comprehensive guide has provided a detailed overview to aid in this critical decision-making process. Remember to factor in cost, maintenance needs, power requirements, and desired levels of speed control and precision when selecting the perfect motor for your project.
Latest Posts
Latest Posts
-
What State Is Chlorine At Room Temperature
Apr 19, 2025
-
Benzaldehyde And Acetone Aldol Condensation Mechanism
Apr 19, 2025
-
Give One Example Of A Chemical Change
Apr 19, 2025
-
A Compound A Has The Formula C8h10
Apr 19, 2025
-
Is Milk Of Magnesia An Acid Or A Base
Apr 19, 2025
Related Post
Thank you for visiting our website which covers about Diff Between Ac And Dc Motor . We hope the information provided has been useful to you. Feel free to contact us if you have any questions or need further assistance. See you next time and don't miss to bookmark.