Device That Converts Electrical Energy Into Mechanical Energy
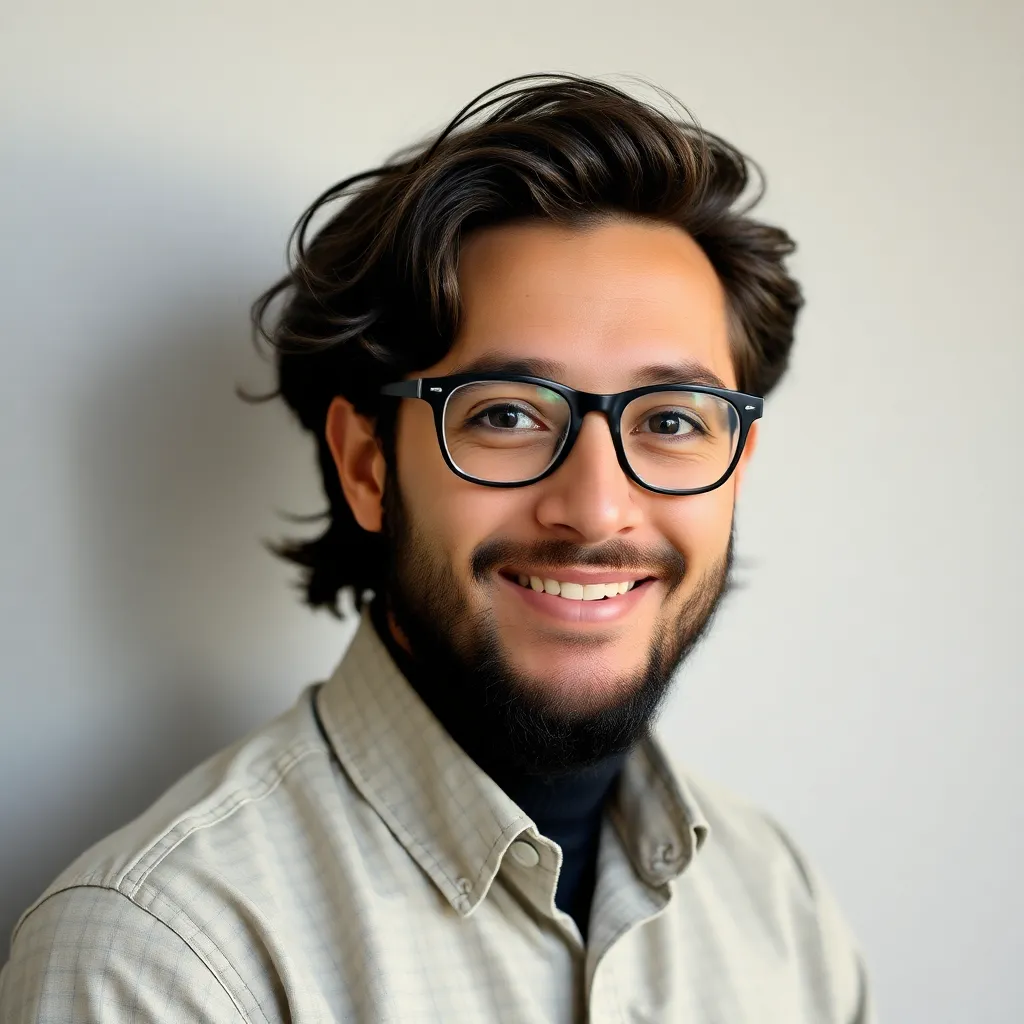
News Leon
Apr 17, 2025 · 6 min read

Table of Contents
Devices That Convert Electrical Energy into Mechanical Energy: A Comprehensive Guide
Electrical energy is a fundamental aspect of modern life, powering countless devices and systems. However, its utility extends far beyond simple illumination and computing. A crucial subset of electrical applications involves the conversion of this readily available energy into mechanical energy—the energy of motion. This conversion process underpins a vast array of technologies, from tiny actuators in smartphones to massive industrial motors driving production lines. This article delves deep into the world of devices that perform this vital energy transformation, exploring their underlying principles, diverse applications, and future trends.
Understanding the Conversion Process: From Electrons to Motion
The core principle behind converting electrical energy into mechanical energy relies on the interaction between magnetic fields and electric currents. This interaction, governed by fundamental electromagnetic laws, generates forces that can be harnessed to produce mechanical movement. The efficiency of this conversion depends on various factors including the design of the device, the materials used, and the operating conditions.
Several key mechanisms facilitate this conversion:
1. Electromagnetic Induction: The Foundation of Many Devices
Electromagnetic induction, discovered by Michael Faraday, is the cornerstone of many electromechanical devices. This principle states that a changing magnetic field induces an electromotive force (EMF) in a nearby conductor. This EMF, in turn, drives an electric current, which can then interact with magnetic fields to generate mechanical force.
2. Lorentz Force: The Driving Force Behind Movement
The Lorentz force is the fundamental force responsible for the motion in many electromechanical systems. This force acts on a charged particle moving in a magnetic field, causing it to experience a sideways deflection. In devices like electric motors, this force acts on current-carrying conductors within a magnetic field, leading to rotation or linear motion.
3. Electrostatic Forces: A Less Common but Significant Mechanism
Electrostatic forces, arising from the interaction of electric charges, can also be used to generate mechanical motion. While less common than electromagnetic mechanisms in large-scale applications, electrostatic actuators are increasingly important in micro-electromechanical systems (MEMS) due to their precise control and high speed.
Types of Devices: A Diverse Landscape of Electromechanical Converters
The world of devices that convert electrical energy into mechanical energy is incredibly diverse, ranging in size, power output, and application. Here are some prominent examples:
1. Electric Motors: The Workhorses of Electromechanical Systems
Electric motors are arguably the most prevalent devices that convert electrical energy into mechanical energy. They come in a wide variety of types, each with its strengths and weaknesses:
-
DC Motors: These motors operate using direct current (DC) electricity. They are relatively simple in design and offer good speed control. Subtypes include brushed DC motors, brushless DC motors, and stepper motors, each suited to different applications. Brushed DC motors are characterized by the presence of brushes that make electrical contact with the commutator, which reverses the current direction in the rotor windings to maintain continuous rotation. Brushless DC motors eliminate the need for brushes, resulting in increased efficiency and longevity. Stepper motors provide precise rotational control, moving in discrete steps rather than continuous rotation.
-
AC Motors: These motors operate using alternating current (AC) electricity. They are widely used in industrial settings due to their robustness and high power output. Common types include induction motors (asynchronous motors) and synchronous motors. Induction motors are extremely common, characterized by their simplicity and relatively low cost. Synchronous motors run at a constant speed synchronized with the AC frequency.
-
Servo Motors: Servo motors are a special type of motor that allows for precise control of position, speed, and torque. They are often used in robotics, automation, and precision machinery. They commonly incorporate closed-loop feedback mechanisms to achieve precise control.
2. Linear Actuators: Generating Straight-Line Motion
Unlike rotary motors, linear actuators generate straight-line motion. These devices are crucial in various applications requiring precise linear movement, such as industrial automation, robotics, and medical devices. Types include:
-
Solenoid Actuators: These are relatively simple devices that use an electromagnet to create a linear force. They are compact and offer high force output for their size, making them suitable for various applications.
-
Piezoelectric Actuators: These actuators utilize the piezoelectric effect, where certain materials generate a mechanical deformation in response to an applied electric field. They provide extremely precise and rapid movements, often used in micro-positioning applications.
-
Electromagnetic Linear Actuators: These actuators utilize electromagnetic principles to directly generate linear motion, often employing a moving coil within a magnetic field.
3. Loudspeakers: Converting Electrical Signals into Sound
While not strictly designed for mechanical work, loudspeakers are a fascinating example of electrical-to-mechanical energy conversion. They utilize a voice coil placed within a magnetic field. The electrical audio signal drives current through the coil, causing it to move in response to the changing magnetic field. This movement of the coil drives a cone, producing sound waves.
4. Relays: Electromechanical Switches
Relays are electromechanical switches that use an electromagnet to control a mechanical switch. When an electric current flows through the electromagnet, it creates a magnetic field that attracts a switch armature, closing or opening the electrical circuit. They're used in a wide range of applications, including power switching, signal routing and protection circuits.
Applications: A Wide Range of Industries and Technologies
The applications of devices converting electrical energy to mechanical energy are vast and diverse, impacting nearly every facet of modern life:
-
Industrial Automation: Electric motors and linear actuators are fundamental to automated production lines, robotic systems, and material handling equipment.
-
Transportation: Electric vehicles rely heavily on electric motors for propulsion. Hybrid and electric trains utilize powerful electric motors for traction.
-
Robotics: Precise and powerful motors are essential components of robots used in various fields, including manufacturing, healthcare, and exploration.
-
Home Appliances: From washing machines and refrigerators to fans and blenders, countless household appliances utilize electric motors.
-
Medical Devices: Precise actuators and motors are used in medical devices such as surgical robots, drug delivery systems, and prosthetics.
-
Computer Peripherals: Printers, scanners, and hard drives all rely on electric motors for their mechanical functions.
-
Aerospace: Electric motors and actuators play crucial roles in flight control systems, satellite positioning, and other aerospace applications.
Future Trends and Innovations
The field of electromechanical energy conversion is constantly evolving. Several trends are shaping the future of these devices:
-
Increased Efficiency: Ongoing research focuses on improving the efficiency of electromechanical devices, reducing energy loss and minimizing environmental impact. Advanced materials and optimized designs are key areas of development.
-
Miniaturization: The development of MEMS technology is driving the creation of increasingly smaller and more efficient electromechanical devices, opening up new applications in micro-robotics, sensor technology, and medical devices.
-
Smart Actuators: Integration of sensors and microcontrollers into electromechanical devices enables smart actuators that can adapt their performance based on real-time feedback, enhancing control precision and system efficiency.
-
Sustainable Materials: The use of sustainable and environmentally friendly materials in the construction of electromechanical devices is becoming increasingly important, reducing the environmental footprint of these essential technologies.
Conclusion
Devices that convert electrical energy into mechanical energy are indispensable components of modern technology. Their diverse applications span a vast range of industries, impacting our lives in countless ways. As research and development continue, we can expect further innovations in efficiency, miniaturization, and functionality, leading to even more widespread adoption and integration into future technologies. The ongoing evolution of these devices promises to shape the future of countless industries and applications, further enhancing our capacity to harness the power of electricity for a wide array of mechanical tasks and innovative advancements.
Latest Posts
Latest Posts
-
A Man Was Killed In His Office Riddle
Apr 19, 2025
-
The Ultimate Source Of Energy That Powers The Sun Is
Apr 19, 2025
-
Is Air A Solution Or Mixture
Apr 19, 2025
-
Is A Webcam An Input Device
Apr 19, 2025
-
Lines Of Symmetry In A Star
Apr 19, 2025
Related Post
Thank you for visiting our website which covers about Device That Converts Electrical Energy Into Mechanical Energy . We hope the information provided has been useful to you. Feel free to contact us if you have any questions or need further assistance. See you next time and don't miss to bookmark.