An Alloy Of Copper And Tin
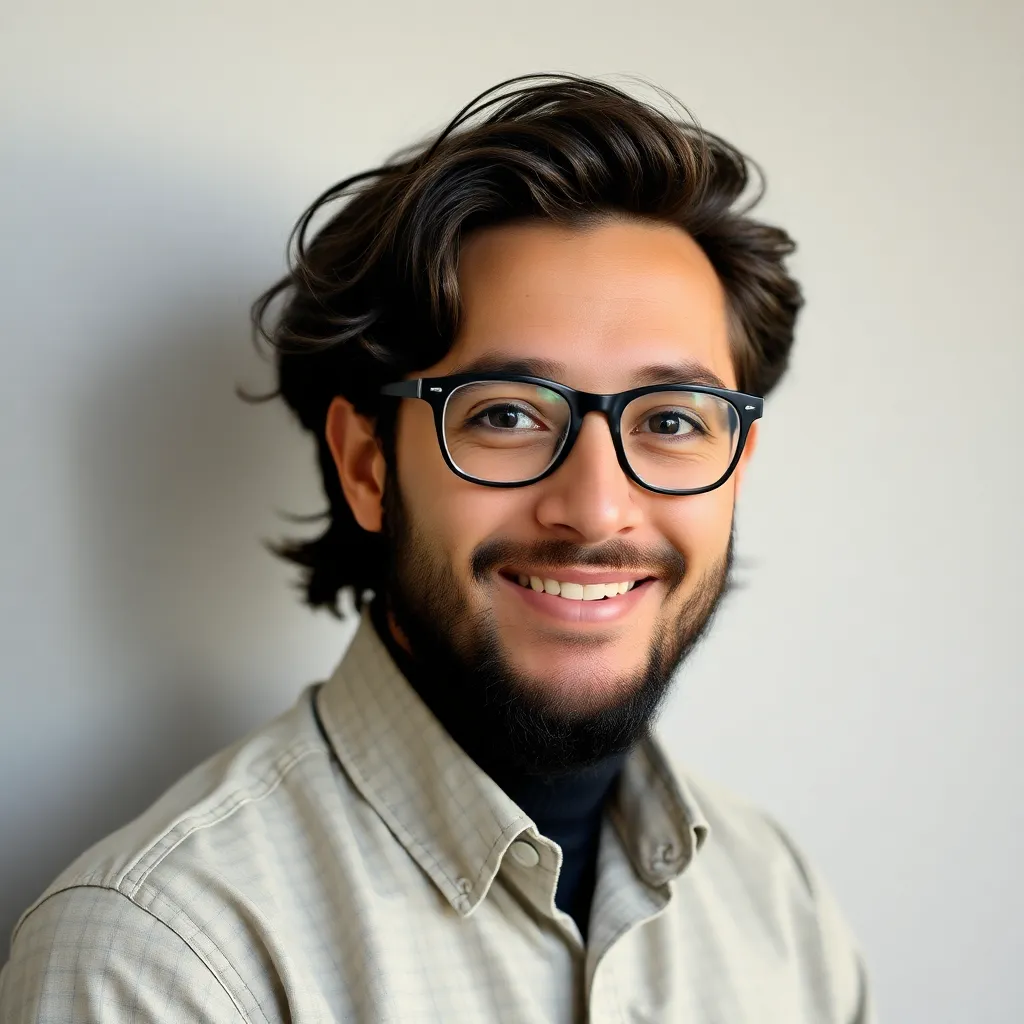
News Leon
Apr 28, 2025 · 8 min read

Table of Contents
Bronze: An Alloy of Copper and Tin – A Deep Dive into History, Properties, and Applications
Bronze, an alloy primarily composed of copper and tin, holds a significant place in human history and continues to find diverse applications in modern times. Its rich history, unique properties, and ongoing relevance make it a fascinating subject for exploration. This article will delve into the various aspects of bronze, exploring its composition, properties, historical significance, manufacturing processes, and contemporary uses.
The Composition of Bronze: More Than Just Copper and Tin
While the basic definition of bronze points to a copper-tin alloy, the reality is far more nuanced. The exact composition varies depending on the desired properties. Tin is the primary alloying element, typically ranging from 1% to 11% by weight. Higher tin content generally leads to a harder, more brittle bronze, while lower tin content results in a softer, more ductile material.
However, the simplicity of just copper and tin is rarely the case. Many bronzes incorporate other elements, often referred to as alloying additions, to tailor specific properties. These additions might include:
- Zinc: Adding zinc can significantly alter the properties, leading to the creation of brass-like bronzes. This is particularly useful for enhancing corrosion resistance and improving machinability.
- Lead: Lead is added to increase machinability, making it easier to cast and shape. However, the presence of lead can negatively impact corrosion resistance.
- Aluminum: Aluminum significantly enhances the strength and corrosion resistance of bronze, making it suitable for high-performance applications.
- Manganese: Manganese improves the strength and hardness of bronze, particularly at elevated temperatures.
- Nickel: Nickel addition enhances corrosion resistance and mechanical strength, making the bronze suitable for marine and chemical environments.
- Silicon: Silicon improves fluidity during casting, resulting in better detail reproduction.
The precise blend of these elements leads to a vast array of bronze alloys, each with its unique characteristics suited to different applications. The variation in composition accounts for the broad spectrum of bronze's properties and uses throughout history and into the modern era.
The Properties of Bronze: A Versatile Material
Bronze's remarkable properties are the foundation of its enduring appeal and extensive applications. These properties arise from the synergistic interaction between copper and tin, and are further modified by the addition of other alloying elements. Key properties include:
- High Strength and Hardness: Compared to pure copper, bronze exhibits significantly improved strength and hardness, making it suitable for tools and weapons. The degree of hardness and strength varies depending on the tin content and other alloying additions.
- Corrosion Resistance: Bronze possesses excellent corrosion resistance, particularly in seawater and various chemical environments. This property is crucial for its use in marine applications and chemical processing equipment. Specific alloying additions, such as aluminum and nickel, can further enhance this resistance.
- Castability: Bronze is relatively easy to cast, allowing for the creation of intricate shapes and designs. This made it ideal for the creation of sculptures, tools, and decorative objects in ancient civilizations.
- Ductility and Malleability: While harder than pure copper, bronze retains a degree of ductility and malleability, which allows for shaping through forging, hammering, and other metalworking techniques. This property contributes to its versatility in crafting.
- Thermal Conductivity: Bronze possesses good thermal conductivity, although lower than pure copper. This property finds application in heat exchangers and other thermal management systems.
- Electrical Conductivity: While not as high as pure copper, bronze's electrical conductivity is still sufficient for certain electrical applications, particularly where corrosion resistance is also a key requirement.
The specific balance of these properties is highly dependent on the alloy's composition. This makes bronze highly customizable for specific needs, a characteristic that has ensured its continued relevance across millennia.
The Historical Significance of Bronze: The Bronze Age
The Bronze Age, spanning roughly from 3300 BCE to 1200 BCE, marks a pivotal period in human history, characterized by the widespread use of bronze for tools, weapons, and other artifacts. The discovery and mastery of bronze smelting revolutionized technology and society. This transition from the Stone Age to the Bronze Age is considered a significant technological leap, enabling advancements in agriculture, warfare, and trade.
The Bronze Age witnessed the development of sophisticated bronze casting techniques, leading to intricate and durable objects. The ability to create stronger and more durable tools facilitated advancements in agriculture, allowing for larger-scale food production and population growth. Improved weapons technology changed warfare, leading to the rise of more powerful and organized societies. The increased efficiency and durability of bronze tools and weapons spurred trade and economic development, facilitating cultural exchange and the growth of civilizations.
Famous examples of bronze artifacts from this period include:
- Bronze sculptures and statues: Many ancient civilizations, such as the Greeks and Romans, produced remarkable bronze sculptures that survive to this day, showcasing the mastery of bronze casting techniques.
- Bronze weapons and tools: Axes, swords, spears, and other tools made from bronze were superior to their stone predecessors, contributing to technological advancements.
- Bronze bells and ceremonial objects: Bronze was also used for creating bells, ritualistic objects, and decorative items, reflecting the material's artistic and symbolic significance.
The Bronze Age left an indelible mark on human civilization, establishing bronze as a foundational material in technological and societal development.
Bronze Manufacturing Processes: From Ancient Techniques to Modern Methods
The production of bronze involves a series of processes, ranging from traditional techniques employed in ancient times to sophisticated modern methods.
Traditional Methods:
- Crucible Melting: In ancient times, bronze was typically made by melting copper and tin together in crucibles, usually clay pots, heated over charcoal fires. This method required careful control of temperature and composition to achieve the desired alloy properties.
- Casting: Once molten, the bronze was poured into molds, typically made of sand or clay. This method allowed for the creation of intricate shapes and designs. The development of lost-wax casting, where a wax model is coated with clay and then melted out, allowed for incredibly detailed bronze sculptures.
- Hammering and Forging: Bronze could also be shaped through hammering and forging, enabling the creation of tools and weapons. This method required skilled craftsmanship to achieve the desired form and strength.
Modern Methods:
Modern bronze production employs more sophisticated techniques, including:
- Induction Melting: Induction melting offers precise temperature control and allows for the production of large quantities of bronze with consistent composition.
- Continuous Casting: Continuous casting provides a highly efficient method for producing bronze in the form of billets, rods, or other shapes.
- Precision Casting: Investment casting, a more advanced version of lost-wax casting, allows for extremely high-precision bronze parts.
- Powder Metallurgy: Powder metallurgy techniques enable the production of bronze components with complex shapes and controlled porosity.
These modern methods have improved the efficiency, precision, and consistency of bronze production, enabling the creation of high-quality bronze components for a wide range of applications.
Contemporary Applications of Bronze: A Material for the Modern Age
Despite its ancient origins, bronze remains a vital material in the 21st century, finding applications in various industries. Its unique combination of properties makes it a suitable choice for many demanding applications.
- Marine Applications: Bronze's exceptional corrosion resistance makes it ideal for marine environments. It is commonly used in marine hardware, propeller shafts, and other components exposed to seawater. Its durability in saltwater makes it an economical choice in these applications.
- Bearings and Bushings: Bronze's excellent wear resistance and low friction make it an excellent material for bearings and bushings in machinery. Its self-lubricating properties reduce wear and extend the lifespan of mechanical components.
- Statues and Sculptures: Bronze continues to be a preferred material for creating statues and sculptures due to its durability, castability, and aesthetic appeal. The artistic tradition of bronze sculpting spans centuries and continues to inspire artists today.
- Musical Instruments: Bronze alloys are used in the construction of musical instruments, such as bells, cymbals, and gongs, due to their ability to produce resonant and pleasing sounds. The precise composition of the bronze alloy is crucial in determining the tonal quality of the instrument.
- Electrical Applications: While its conductivity is lower than copper, bronze finds use in certain electrical applications where corrosion resistance is paramount. It can be found in electrical connectors, switches, and other components exposed to harsh environments.
- Architectural Applications: Bronze is increasingly used in architectural applications, such as roofing, cladding, and decorative elements, due to its durability, aesthetic appeal, and resistance to weathering.
These applications showcase the versatility and continuing relevance of bronze in a technologically advanced world. Its unique blend of properties, combined with ongoing advancements in manufacturing techniques, ensure its continued use for many years to come.
Conclusion: A Timeless Material
Bronze, an alloy of copper and tin, holds a unique position in the history of human civilization and continues to play a significant role in modern technology. From its origins in the Bronze Age to its diverse applications in contemporary industries, bronze has demonstrated its versatility, durability, and aesthetic appeal. Its unique properties, resulting from the careful balance of copper, tin, and other alloying elements, ensure that this ancient material remains relevant and vital in the 21st century and beyond. The ongoing innovation in bronze production methods further enhances its potential, making it a material worth studying and appreciating for its rich history and continuing importance in our world.
Latest Posts
Latest Posts
-
Which Of The Following Nitrogen Bases Is Unique To Rna
Apr 28, 2025
-
Tannenbaum And Schmidt Model Of Leadership
Apr 28, 2025
-
How Many Genotypes In A Trihybrid Cross
Apr 28, 2025
-
Do Isotopes Have Same Chemical Properties
Apr 28, 2025
-
Is Co A Element Or Compound
Apr 28, 2025
Related Post
Thank you for visiting our website which covers about An Alloy Of Copper And Tin . We hope the information provided has been useful to you. Feel free to contact us if you have any questions or need further assistance. See you next time and don't miss to bookmark.