Able To Be Drawn Into Wire
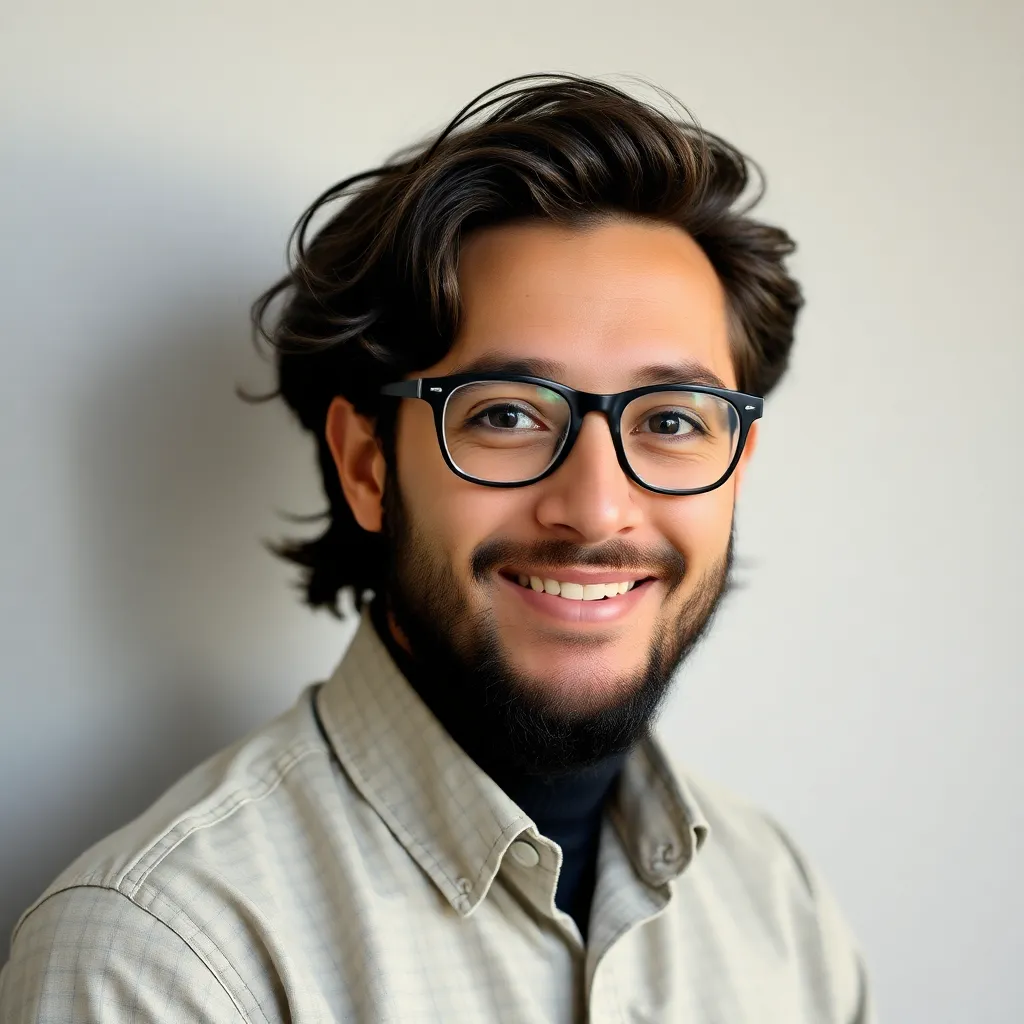
News Leon
Apr 04, 2025 · 6 min read

Table of Contents
Able to be Drawn into Wire: A Deep Dive into Ductility and its Applications
The ability of a material to be drawn into a wire, a property known as ductility, is a crucial characteristic in various industries. This property isn't simply about shaping metal; it's fundamental to the creation of countless everyday objects, from the electrical wires powering our homes to the intricate components within sophisticated electronics. Understanding ductility, its underlying mechanisms, and the factors influencing it is essential for material scientists, engineers, and anyone interested in the manufacturing process of wires and other ductile products.
What is Ductility?
Ductility, in its simplest form, refers to a material's ability to deform under tensile stress; that is, to be stretched into a thinner shape without fracturing. This deformation is typically permanent, meaning the material doesn't return to its original shape once the stress is removed. It's a crucial mechanical property often expressed as the percentage elongation a material undergoes before it breaks. High ductility implies the material can be significantly stretched before failure. The opposite of ductility is brittleness, where a material fractures with little to no plastic deformation.
Measuring Ductility: Tensile Testing
The most common method for quantifying ductility is through tensile testing. In this process, a standardized specimen of the material is subjected to a controlled tensile force until it breaks. Engineers measure several parameters, including:
- Yield Strength: The stress at which the material begins to deform plastically.
- Ultimate Tensile Strength (UTS): The maximum stress the material can withstand before failure.
- Elongation: The percentage increase in length of the specimen before fracture. This is a direct measure of ductility.
- Reduction in Area: The percentage decrease in the cross-sectional area of the specimen at the point of fracture. This provides additional information about the material's ductility.
Higher elongation and reduction in area values indicate greater ductility. These values depend heavily on factors like temperature, strain rate, and the material's microstructure.
Factors Affecting Ductility
Several factors significantly influence a material's ductility. Understanding these factors is key to selecting appropriate materials for wire drawing and other ductility-dependent applications.
1. Material Composition:
The chemical composition of a material profoundly impacts its ductility. Pure metals generally exhibit higher ductility than alloys. The presence of impurities, even in small amounts, can significantly reduce ductility by hindering the movement of dislocations, the microscopic defects responsible for plastic deformation.
Specific alloying elements can either enhance or diminish ductility. For instance, adding carbon to steel increases its strength but reduces its ductility. Conversely, certain alloying additions can improve ductility, making the material more suitable for wire drawing.
2. Temperature:
Temperature plays a critical role in ductility. Generally, increasing the temperature enhances ductility. At higher temperatures, atoms have more kinetic energy, allowing them to move more readily and accommodate the plastic deformation. This reduces the resistance to dislocation movement, making the material easier to draw into a wire. This is why many wire drawing processes are performed at elevated temperatures.
3. Strain Rate:
The rate at which a material is deformed (strain rate) also affects its ductility. Faster strain rates tend to decrease ductility, as the material doesn't have enough time to accommodate the deformation through dislocation movement. Slower strain rates generally allow for more plastic deformation before fracture, resulting in higher ductility.
4. Microstructure:
The microstructure of a material, including grain size, phase distribution, and the presence of precipitates or inclusions, significantly affects its ductility. Fine-grained materials generally exhibit better ductility than coarse-grained materials due to the increased number of grain boundaries that hinder dislocation movement. The presence of second-phase particles or precipitates can also reduce ductility by obstructing dislocation motion.
5. Processing:
The manufacturing processes involved in creating the material can also impact its ductility. For example, cold working, a process that deforms a material at room temperature, can decrease ductility by increasing dislocation density. Annealing, a heat treatment process that relieves internal stresses, can improve ductility by reducing dislocation density and promoting recrystallization.
Materials Able to be Drawn into Wire
Several materials exhibit significant ductility and are commonly drawn into wires:
1. Copper:
Copper is highly ductile and an excellent conductor of electricity, making it ideal for electrical wiring. Its high ductility allows for the creation of fine wires with minimal breakage.
2. Aluminum:
Aluminum is another highly ductile material, known for its lightweight and corrosion resistance. It's used extensively in electrical transmission lines and various other applications requiring lightweight, conductive wires.
3. Steel:
Various types of steel, with different alloying compositions, can be drawn into wires. The ductility of steel depends heavily on its carbon content and other alloying elements. Low-carbon steel is more ductile than high-carbon steel. Steel wires are used in a wide range of applications, from construction to automotive parts.
4. Gold:
Gold's exceptional ductility allows it to be drawn into extremely fine wires, sometimes even thinner than human hair. This property makes it suitable for delicate applications in electronics and jewelry making.
5. Silver:
Similar to gold, silver is a highly ductile metal used in various applications, including electrical contacts and jewelry. Its high ductility allows for the creation of fine wires with excellent conductivity.
Wire Drawing Process
The process of drawing a wire involves pulling a metal rod through a series of progressively smaller dies, reducing its diameter and increasing its length. The process is typically performed in multiple stages to achieve the desired final diameter. Lubricants are often used to reduce friction and prevent die wear.
Stages of Wire Drawing:
- Preparation: The metal rod, often called a billet, is cleaned and prepared for the drawing process.
- Pointing: The end of the billet is tapered to a point, allowing it to be easily fed through the first die.
- Drawing: The pointed billet is pulled through a series of dies, each reducing the diameter slightly.
- Annealing (Optional): Between drawing stages, annealing may be necessary to relieve stresses and maintain ductility.
- Finishing: The final stage involves cleaning and inspecting the drawn wire.
Applications of Ductile Materials and Wire Drawing
The applications of ductile materials and the wire drawing process are vast and diverse:
- Electrical Wiring: Copper and aluminum wires are essential for electrical power transmission and distribution.
- Telecommunications: Fine wires are used in telecommunications cables for signal transmission.
- Automotive Industry: Steel wires are used in various automotive components, such as springs, cables, and reinforcement structures.
- Construction: Steel wires are used in reinforcing concrete and creating cables for bridges and other structures.
- Electronics: Fine gold and silver wires are used in electronic components and integrated circuits.
- Medical Devices: Ductile materials are used in creating stents, guidewires, and other medical implants.
- Aerospace: Lightweight, high-strength wires are used in aircraft and spacecraft construction.
Conclusion
Ductility, the ability of a material to be drawn into wire, is a critical property with wide-ranging implications across numerous industries. Understanding the factors affecting ductility and the intricacies of the wire drawing process is vital for selecting appropriate materials and optimizing manufacturing processes. As technology advances, the demand for high-performance ductile materials and sophisticated wire drawing techniques will only continue to grow, driving innovation and shaping the future of various industries. Further research into enhancing ductility through material science innovations and advanced processing techniques will undoubtedly play a crucial role in advancing technological progress.
Latest Posts
Latest Posts
-
How Many Right Angles Does A Trapezium Have
Apr 11, 2025
-
During An Experiment Which Factors Are Observed And Measured
Apr 11, 2025
-
Cells Are Thin And Flat With Irregular Borders
Apr 11, 2025
-
What Are The Requirements For Photosynthesis To Occur
Apr 11, 2025
-
Is Al Oh 3 A Strong Base
Apr 11, 2025
Related Post
Thank you for visiting our website which covers about Able To Be Drawn Into Wire . We hope the information provided has been useful to you. Feel free to contact us if you have any questions or need further assistance. See you next time and don't miss to bookmark.