A Heat Flux Of 4000 J/s Is To Be Passed
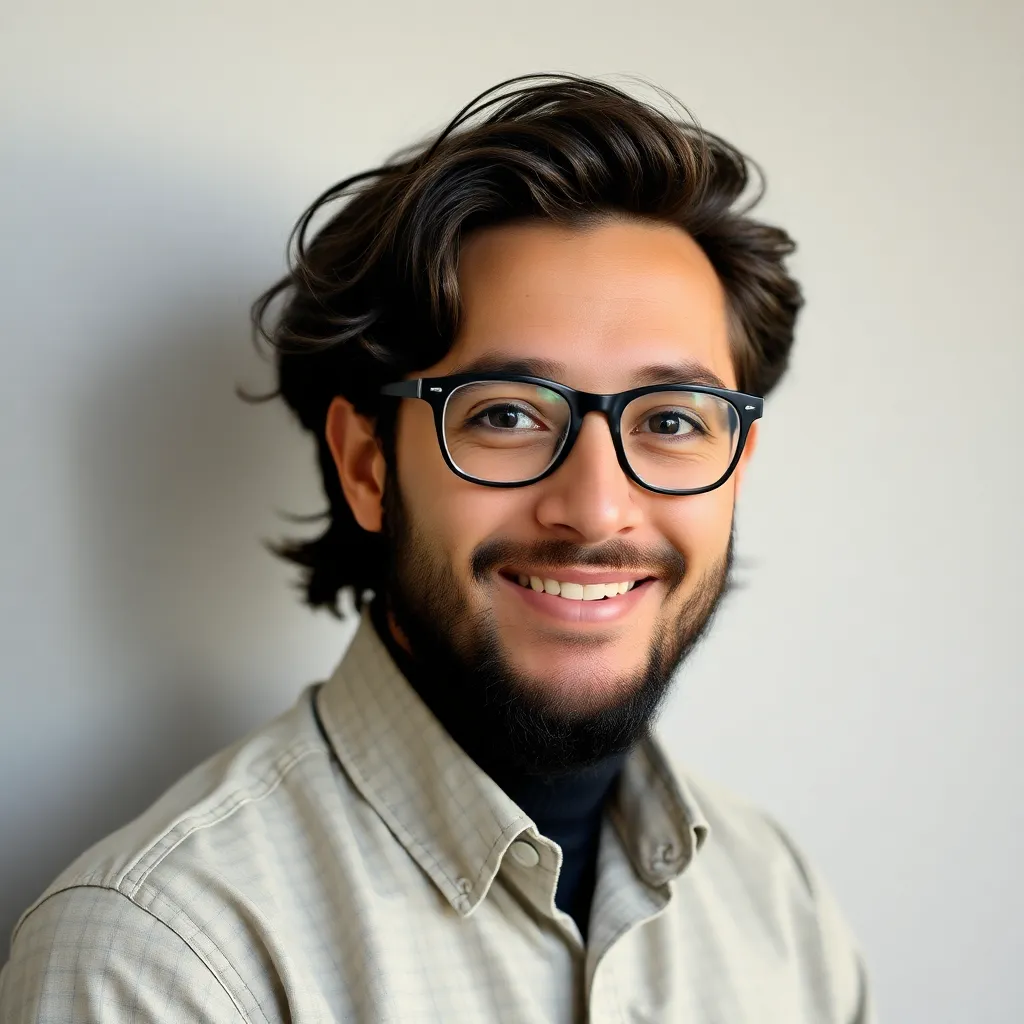
News Leon
Mar 12, 2025 · 6 min read

Table of Contents
A Heat Flux of 4000 J/s: Design Considerations and Applications
A heat flux of 4000 J/s (4 kW) represents a significant thermal load, demanding careful consideration in design and application. This level of heat transfer necessitates the selection of appropriate materials, efficient cooling mechanisms, and a deep understanding of heat transfer principles. This article delves into the complexities of managing a 4000 J/s heat flux, exploring various scenarios and offering practical guidance for engineers and designers.
Understanding Heat Flux and its Implications
Heat flux, measured in Watts per square meter (W/m²) or Joules per second per square meter (J/s/m²), quantifies the rate of heat transfer per unit area. A heat flux of 4000 J/s implies a substantial amount of heat energy being transferred. The critical factor isn't just the total heat, but the area over which this heat is distributed. A small area experiencing a 4000 J/s flux will experience significantly higher temperatures than a large area with the same total heat transfer.
Key Considerations:
- Surface Area: The smaller the area, the higher the temperature rise at the surface. This dictates the need for effective heat dissipation strategies.
- Material Properties: Material selection is paramount. Materials with high thermal conductivity are crucial for efficient heat transfer away from the heat source. Thermal diffusivity also plays a significant role, determining how quickly temperature changes propagate through the material.
- Cooling Mechanisms: Effective cooling is crucial. This might involve methods like forced convection (fans, pumps), natural convection (heat sinks), or even more advanced techniques like liquid cooling or phase-change cooling.
- Temperature Limits: Materials have temperature limits beyond which they degrade or fail. Exceeding these limits can lead to catastrophic equipment failure.
- Safety Considerations: High heat fluxes pose safety risks. Appropriate safety measures, including insulation, shielding, and warning systems, are essential.
Applications Requiring High Heat Flux Management
Several industrial and technological applications necessitate managing a heat flux comparable to 4000 J/s. These include:
1. Electronic Cooling:
High-power electronic components, such as processors in data centers or power electronics in electric vehicles, generate significant heat. Managing the heat flux generated by these components is crucial to prevent overheating and maintain operational efficiency. Advanced cooling solutions, including liquid cooling systems and heat pipes, are commonly employed.
2. Industrial Processes:
Many industrial processes, such as welding, metal casting, and chemical reactions, generate considerable heat. Controlling the heat flux is vital to ensure product quality, process efficiency, and worker safety. This often involves specialized cooling systems and thermal management techniques.
3. Energy Generation and Storage:
High heat fluxes are prevalent in energy generation and storage technologies. Solar thermal power plants concentrate sunlight to generate high temperatures, requiring robust heat management systems. Similarly, advanced batteries for electric vehicles can produce considerable heat during charging and discharging, necessitating effective cooling mechanisms to prevent thermal runaway.
4. Aerospace and Defense:
High-speed flight and aerospace applications generate significant aerodynamic heating. Managing the heat flux on hypersonic vehicles or spacecraft re-entering the atmosphere is crucial to prevent structural damage. This demands advanced materials and thermal protection systems.
Strategies for Managing a 4000 J/s Heat Flux
Effective management of a 4000 J/s heat flux relies on a multifaceted approach:
1. Material Selection:
Choosing materials with high thermal conductivity is paramount. Metals like copper and aluminum are excellent conductors and are frequently used in heat sinks and other cooling applications. However, the cost and weight of these materials need to be considered. Advanced materials like carbon nanotubes and graphene offer even higher thermal conductivity but are often more expensive and challenging to process.
2. Surface Area Enhancement:
Increasing the surface area exposed to the cooling medium enhances heat transfer. This can be achieved through the use of fins, extended surfaces, or micro-channels. These features significantly increase the surface area available for heat dissipation, leading to lower temperatures.
3. Forced Convection Cooling:
Forced convection, where a fluid (air, liquid, or gas) is actively circulated over the heat-generating surface, is highly effective for managing high heat fluxes. Fans and pumps are commonly used to enhance heat transfer rates. Liquid cooling offers superior performance compared to air cooling, especially for high heat fluxes.
4. Heat Pipes:
Heat pipes are passive devices that efficiently transport heat through a phase-change process. They utilize the latent heat of vaporization to move heat from a hot source to a cooler location. Heat pipes are particularly effective for managing high heat fluxes over relatively long distances.
5. Immersion Cooling:
Immersion cooling, where the heat-generating component is submerged in a dielectric fluid, offers an excellent method for managing high heat fluxes. The fluid directly contacts the component, leading to exceptionally efficient heat transfer. This technique is increasingly common in data centers and high-performance computing applications.
6. Phase-Change Cooling:
Phase-change cooling utilizes the latent heat of fusion or vaporization to absorb large amounts of heat with minimal temperature change. This approach provides significant thermal capacity and is suitable for managing high, transient heat fluxes. This could involve using materials that undergo phase transitions within the temperature range of operation.
Designing for a 4000 J/s Heat Flux: A Step-by-Step Approach
Designing a system to handle a 4000 J/s heat flux requires a systematic approach:
-
Define the Heat Source: Precisely determine the location, size, and characteristics of the heat source. This information is critical for selecting appropriate cooling strategies.
-
Determine the Acceptable Temperature Rise: Establish the maximum allowable temperature rise for the heat-generating component and surrounding materials. This temperature limit is dictated by material properties and safety considerations.
-
Select the Cooling Mechanism: Based on the heat source characteristics and temperature limits, choose an appropriate cooling mechanism. Consider factors such as cost, efficiency, complexity, and space constraints.
-
Design the Cooling System: Develop a detailed design of the cooling system, including the geometry of heat sinks, the flow rate of the cooling fluid, and the placement of components. Computational fluid dynamics (CFD) simulations can assist in optimizing the design for optimal heat transfer.
-
Material Selection and Analysis: Select appropriate materials based on their thermal conductivity, strength, and other relevant properties. Perform thermal analysis to ensure the selected materials can withstand the expected temperatures and stresses.
-
Prototype and Testing: Construct a prototype of the system and conduct thorough testing to validate the design and ensure it meets performance requirements. Monitor temperatures at various locations to confirm effective heat dissipation.
-
Optimization and Iteration: Based on testing results, iterate on the design to further optimize its performance. This iterative process can lead to significant improvements in efficiency and reliability.
Future Trends in High Heat Flux Management
Ongoing research and development continue to advance the field of high heat flux management:
-
Nanofluids: Nanofluids, which are suspensions of nanoparticles in conventional fluids, offer enhanced thermal conductivity and can improve the effectiveness of cooling systems.
-
Metamaterials: Metamaterials with engineered thermal properties hold promise for achieving highly efficient heat transfer.
-
Advanced Cooling Techniques: Research continues on advanced cooling techniques such as thermoelectric cooling, magnetocaloric cooling, and microfluidic cooling, offering potentially superior performance compared to traditional methods.
Managing a heat flux of 4000 J/s requires a comprehensive understanding of heat transfer principles, material science, and cooling technologies. Careful planning, meticulous design, and thorough testing are essential to ensure the success of any system dealing with such a significant thermal load. The strategies outlined in this article provide a foundation for engineers and designers tackling this challenge, paving the way for more efficient and reliable high-power systems. Continuous innovation in materials and cooling technologies will further enhance our capabilities in managing increasingly demanding heat fluxes in diverse applications.
Latest Posts
Related Post
Thank you for visiting our website which covers about A Heat Flux Of 4000 J/s Is To Be Passed . We hope the information provided has been useful to you. Feel free to contact us if you have any questions or need further assistance. See you next time and don't miss to bookmark.