A Drum Rotates Around Its Central
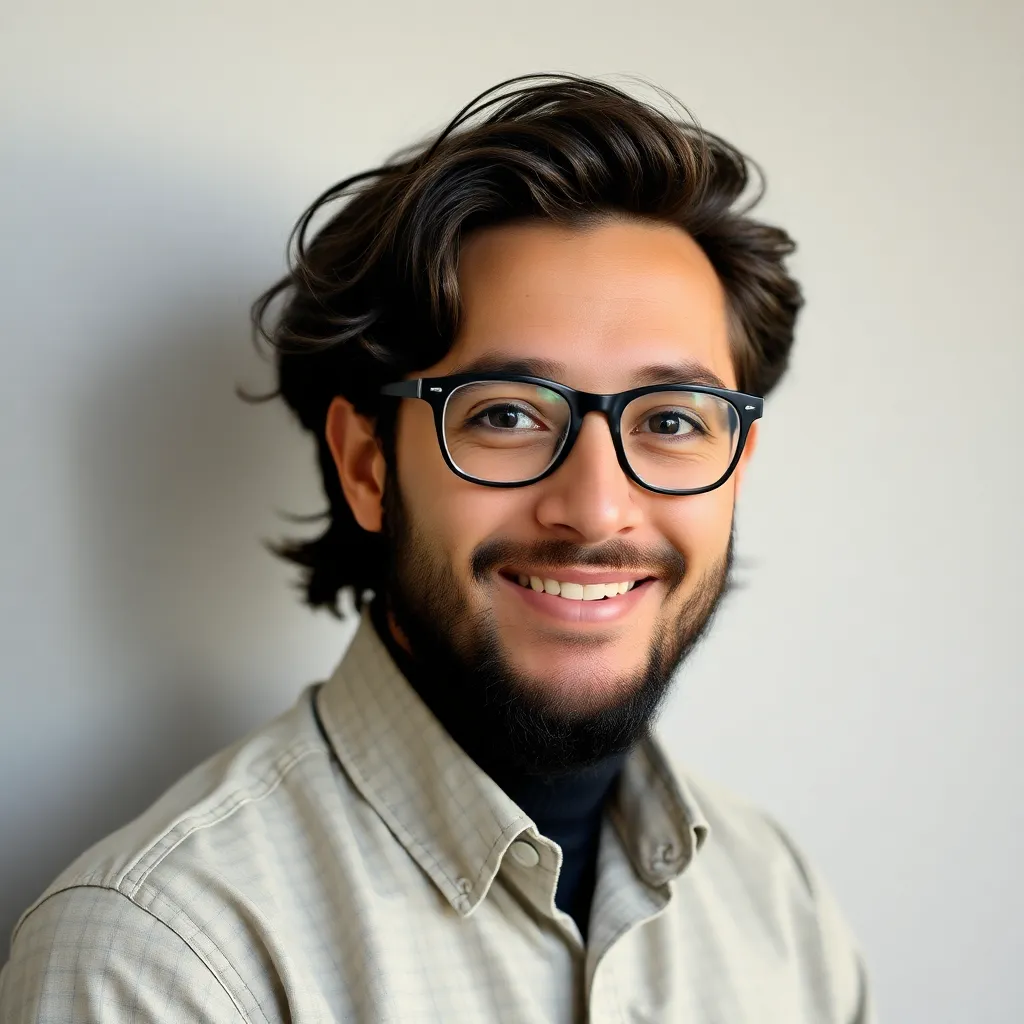
News Leon
Mar 09, 2025 · 7 min read

Table of Contents
A Drum Rotates Around Its Central Axis: Exploring the Physics and Applications
The seemingly simple act of a drum rotating around its central axis belies a rich tapestry of physics principles and a wide range of practical applications. From the humble washing machine to sophisticated industrial processes, understanding the rotational dynamics of a drum is crucial. This article delves deep into the mechanics involved, explores various applications, and touches upon the engineering challenges associated with designing and optimizing rotating drum systems.
Understanding Rotational Dynamics
At the heart of a rotating drum's operation lies the fundamental concept of rotational motion. Unlike linear motion, which involves movement along a straight line, rotational motion involves movement around a fixed axis – in this case, the central axis of the drum. This rotation is governed by several key physical principles:
1. Torque and Angular Acceleration:
The initiation and alteration of a drum's rotational speed are controlled by torque. Torque, a rotational force, is the product of the force applied and the perpendicular distance from the axis of rotation to the point where the force is applied. A larger torque leads to a greater angular acceleration, the rate of change of the drum's angular velocity (rotational speed). This relationship is analogous to Newton's second law (F=ma) in linear motion. Consider, for instance, a washing machine: the motor applies a torque to the drum, causing it to spin. The magnitude of this torque determines how quickly the drum accelerates.
2. Moment of Inertia:
The moment of inertia is a measure of an object's resistance to changes in its rotational motion. It depends on both the mass of the object and how that mass is distributed relative to the axis of rotation. A drum with its mass concentrated near the axis will have a lower moment of inertia than one with mass distributed further out. This is crucial because a higher moment of inertia requires a larger torque to achieve the same angular acceleration. In practical terms, this means that a drum filled with heavy objects will be harder to spin up to speed than an empty one.
3. Angular Momentum:
Angular momentum is the rotational equivalent of linear momentum. It's the product of the moment of inertia and the angular velocity. A crucial principle of physics states that in the absence of external torques, the angular momentum of a rotating system remains constant. This is the principle of conservation of angular momentum. This explains why a figure skater spins faster when they pull their arms inward, decreasing their moment of inertia and thus increasing their angular velocity to conserve angular momentum. In a similar way, understanding angular momentum helps in designing and controlling the speed of a rotating drum.
4. Centrifugal Force:
As the drum rotates, the contents inside experience centrifugal force, an apparent outward force. This force is crucial in applications like washing machines (where it helps to squeeze water out of clothes) and centrifuges (used to separate substances of different densities). The magnitude of this force is directly proportional to the mass of the object, the square of the angular velocity, and the distance from the axis of rotation. A faster spinning drum generates a stronger centrifugal force.
Applications of Rotating Drums
The rotating drum is a ubiquitous design element across a remarkable array of applications:
1. Washing Machines:
The most common example, washing machines utilize a rotating drum to agitate clothes and water, facilitating cleaning. The centrifugal force generated during the spin cycle removes excess water, significantly reducing drying time. The design considerations here involve balancing the torque required for efficient cleaning with the durability of the drum and its bearings to withstand the repeated stresses of rotation.
2. Industrial Dryers:
Similar to washing machines, industrial dryers use rotating drums to dry various materials, from textiles to agricultural products. The design considerations here focus on efficient heat transfer and airflow to optimize drying time while preventing damage to the material being dried. Larger drums and more powerful motors are often required for industrial applications compared to domestic use.
3. Centrifuges:
Centrifuges are crucial tools in laboratories and industrial settings for separating substances with different densities. By rotating the drum at high speeds, centrifugal force separates heavier components from lighter ones. Examples include blood separation in medical diagnostics and separating solids from liquids in industrial processes. The engineering challenge here lies in achieving extremely high rotational speeds safely and accurately.
4. Rotating Kilns:
In the cement and ceramics industries, rotating kilns are used for high-temperature processing. Raw materials are fed into a long, rotating cylindrical drum that slowly moves them through a heated zone. The rotation ensures even heating and prevents material build-up. The design considerations for these kilns are substantial, requiring robust materials to withstand extreme temperatures and careful control of the rotational speed and inclination to optimize the process.
5. Conveyor Systems:
Rotating drums are sometimes integrated into conveyor systems to move materials along a path. This is especially useful for handling bulk materials or items that are difficult to transport using conventional methods. The design focuses on the appropriate surface texture of the drum and the speed of rotation to achieve optimal material flow.
6. Rotary Drums in Material Processing:
Rotating drums are widely used for various material processing tasks like mixing, blending, and grinding. These drums are often equipped with internal components to enhance the efficiency of the process. The choice of drum material, speed, and internal components heavily influence the outcome of the process.
7. Powder Coating Systems:
In powder coating applications, the rotating drum is a critical component that ensures a uniform coating of powder onto the workpiece. The speed of the drum ensures uniform distribution of the powder particles. This process is widely used in various industries for applying durable and attractive finishes.
Engineering Challenges and Design Considerations
Designing and optimizing rotating drum systems involves overcoming several significant engineering challenges:
1. Bearing Selection:
The bearings supporting the drum must withstand significant radial and axial loads, as well as high rotational speeds. The choice of bearing type (e.g., ball bearings, roller bearings) depends on the specific application, considering factors like load capacity, speed, and required lifespan. Improper bearing selection can lead to premature failure and costly downtime.
2. Material Selection:
The drum material must be strong enough to withstand the centrifugal forces and other stresses it experiences during operation. Material selection is crucial, taking into account factors like corrosion resistance, temperature resistance, and overall durability. Different materials are suitable for different applications – stainless steel is common for food processing, while more specialized alloys may be required for high-temperature applications.
3. Balancing and Vibration Control:
Unbalanced drums can lead to significant vibrations, potentially damaging the system and reducing its lifespan. Precise balancing is crucial, often achieved through careful manufacturing and the addition of counterweights to offset any imbalances. Vibration isolation techniques might also be necessary in sensitive applications.
4. Seal Design:
For applications involving liquids or gases, effective sealing is crucial to prevent leakage and maintain the integrity of the system. Seal design must account for the rotational motion and the pressures involved. Various seal types exist, each with its strengths and limitations.
5. Motor Selection and Control:
The motor must provide sufficient torque to accelerate and maintain the desired rotational speed of the drum. Motor selection depends on factors such as the drum's moment of inertia, required speed, and operating conditions. Precise speed control is often essential, requiring sophisticated control systems.
6. Safety Considerations:
Safety is paramount in designing and operating rotating drum systems, especially those operating at high speeds. Safety features such as interlocks, emergency stops, and protective casings are crucial to prevent accidents and injuries.
Conclusion:
The seemingly simple act of a drum rotating around its central axis underpins a vast array of applications across diverse industries. A deep understanding of the underlying physics, including rotational dynamics, torque, moment of inertia, and centrifugal force, is essential for designing and optimizing these systems. Addressing engineering challenges related to bearing selection, material choice, balancing, sealing, motor selection, and safety is critical for creating efficient, reliable, and safe rotating drum systems. As technology advances, we can anticipate further innovations in the design and application of this fundamental mechanical element.
Latest Posts
Related Post
Thank you for visiting our website which covers about A Drum Rotates Around Its Central . We hope the information provided has been useful to you. Feel free to contact us if you have any questions or need further assistance. See you next time and don't miss to bookmark.